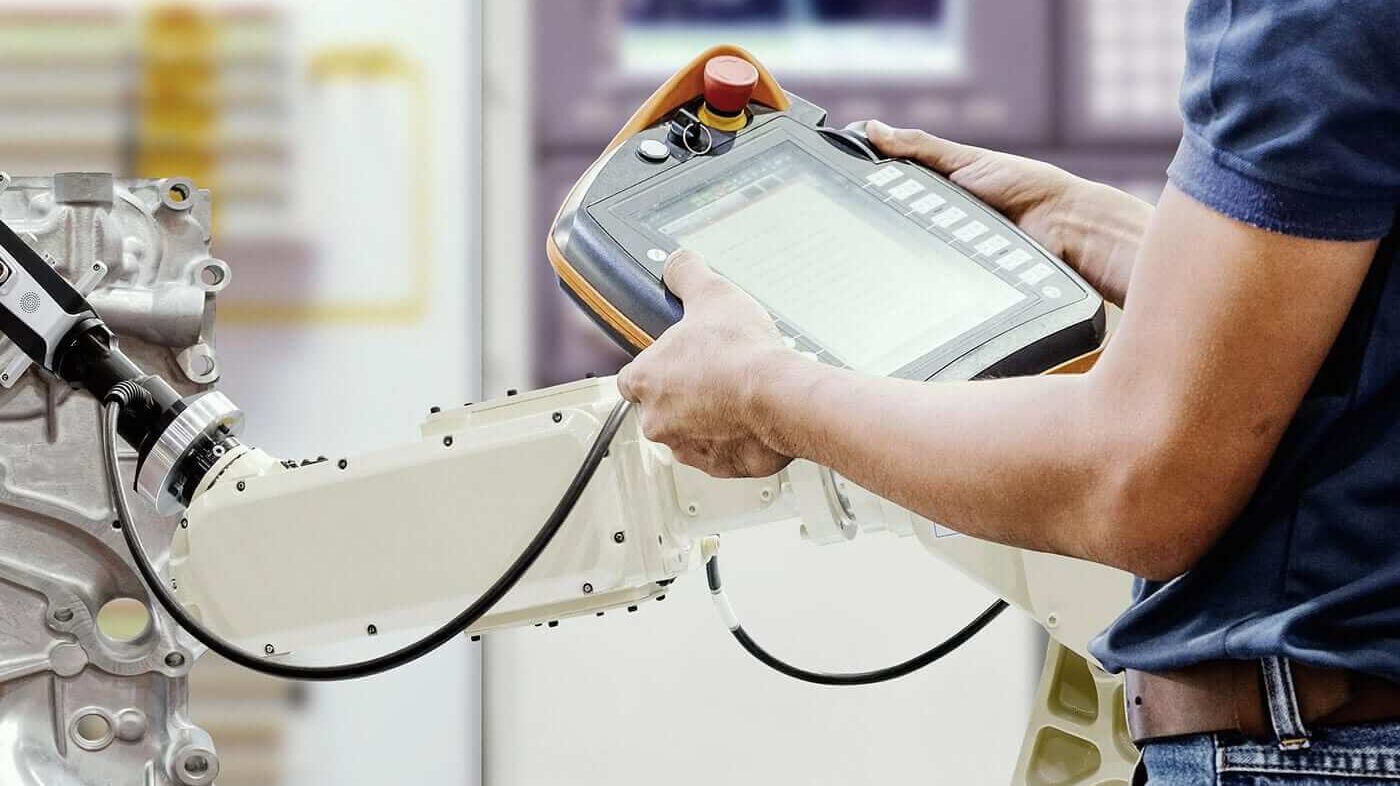
Elektromobilität: Neue Fertigungsprozesse
Predictive Quality und Produktion
Ein 1st-Tier-Automobilzulieferer stand vor der Aufgabe, elektromechanische Komponenten für ein zukünftiges E-Mobil-Fahrzeugkonzept zu entwickeln. Bei einer steilen Anlaufkurve zur gewohnten Serienqualität des Kunden musste das Unternehmen dazu eine neue Fertigungstechnologie mit neuen Materialien umsetzen. Gemeinsam mit ROI-EFESO erweiterte es seine dazu erforderlichen Kernkompetenzen.
Herausforderung
Mit den Anforderungen der E-Mobilität und Digitalisierung des Produktes sieht sich ein Automobilzulieferer mit gleich zwei Paradigmenwechsel in seinem Kerngeschäft konfrontiert. In einem seiner Werke etabliert das Unternehmen adäquate Lösungsansätze für die Fertigung eines „neuen Produkts“ mit komplett neuen Planungs- und Produktionsprozessen.
MEHRROI-EFESO Lösungsansatz
ROI-EFESO entwickelte ein zukunftsorientiertes, modulares Gesamtkonzept mit Fokus auf Reduzierung von Ausschuss durch „Predictive Production“ und „Predictive Quality“ in der Fertigungslinie. Ein „Digitaler Prozess Zwilling“ spielt hierbei eine zentrale Rolle.
MEHRLessons Learned
Traditionelle Strukturen in den IT- und Fertigungsprozessen müssen überdacht und harmonisiert werden. Die richtige Nutzung der vorhandenen und der zukünftig anfallenden Daten erweist sich als Schlüssel zum Erfolg.
MEHRROI-EFESO Erfolgsmodell
Die anbieterunabhängige Beratung sowie das Ergebnis eines neu aufgesetzten Prozesses als Gesamtpaket überzeugten. Es wurde ein Reifegrad erreicht, der eine Weiterentwicklung zu skalierbaren IIoT-Architekturen und Smart Factory auf Basis Künstlicher Intelligenz zulässt.
MEHRNeue Fertigungsverfahren für die Mobilität der Zukunft
Unternehmen der Automobilbranche sind heute mit der Herausforderung konfrontiert, mehr als nur einen gravierenden Umbruch in ihrem Markt zu meistern: so bringt das autonome Fahren eine völlig andere Art der Funktionalität und Kommunikation im Fahrzeug mit sich – das Produkt wird digital. Zudem sind alternative, umweltschonendere Antriebskonzepte dringend notwendig. All diese Veränderungen haben Auswirkungen auf den gesamten Produktentstehungsprozess. Wie in diesem Fall eines 1st-Tier-Automobilzulieferers, der vor der Aufgabe stand, elektromechanische Komponenten für ein zukünftiges E-Mobil-Fahrzeugkonzept zu entwickeln. Bei einer steilen Anlaufkurve zur gewohnten Serienqualität des Kunden musste das Unternehmen dazu eine neue Fertigungstechnologie mit neuen Materialien umsetzen. Mit ROI-EFESO erweiterte das Unternehmen seine dazu erforderlichen Kernkompetenzen.
Aufgrund der außergewöhnlich hohen Komplexität der Aufgabenstellung war es im ersten Schritt wichtig, die bisherigen Methoden und Prozesse in Industrial Engineering und Prozessplanung zu hinterfragen und neue, geeignete Alternativen zu definieren. Dass keinerlei Erfahrungswerte hierzu vorlagen, machte die Aufgabe nicht einfacher: die bisher eingesetzten Werkzeuge waren autark und die bereits erfassten Daten in Datensilos isoliert. Die vorhandenen Erfahrungswerte wurden weder ausreichend analysiert, noch systematisch für die Weiterentwicklung und Optimierung genutzt.
Prozesse verstehen und modifizieren
Bereits bei Projektstart war dem Team, das sich aus neun Mitarbeiter:innen des Kunden und drei ROI-EFESO Berater:innen zusammensetzte, daher eines klar: es musste die Prozesse, Tools, Abläufe und Planungen komplett untersuchen und hinterfragen. Zudem sollten bisher händische Prozesse automatisiert, Daten erhoben, verknüpft und analysiert werden. Bereits eingesetzte Softwarelösungen untersuchte das Team auf Anpassungen hin und etablierte eine entsprechende Analytics-Plattform für den Proof-of-Concept.
Verifizierungen mit Digital Prozess Twin
Parallel war der Aufbau von neuen Kompetenzen erforderlich. Das Projektteam hob die bisherige Isolierung der jeweiligen Fertigungs- und Prozessdaten auf und identifizierte die für den zukünftigen Produktionsprozess erforderlichen Tools. Mit Hilfe eines Digital Prozess Twin ließen sich dabei erste Verifizierungen durchführen – unabhängig von der laufenden Produktion, aber bereits mit Echtzeitdaten. Als nächste Entwicklungsstufe im Projekt plant das Unternehmen den zukünftigen Einsatz von künstlicher Intelligenz in einer Smart Factory, um somit einen entscheidenden Wettbewerbsvorteil sicher zu stellen.
Predictive Quality und Produktion
Als Schlüssel zum Projekterfolg erwiesen sich vorausschauende Bewertungen und Analysen: So bildete das Projektteam über den Digital Prozess Twin Einflussgrößen ab und entwickelte Prozesse digital weiter, in dem es diese variierte und optimierte. Dadurch wurden die Analysen sukzessive immer weiter verfeinert und die Güte der Vorhersagen ständig präziser. Zudem verknüpfte das Team die vorhandenen Daten erstmalig, so dass sich diese nun als Echtzeit-Prozessdaten direkt auswerten lassen.
Aussagekräftiges Prozessmodell
Aus den mehr als 200 Variablen identifizierte es die entscheidenden Einflussgrößen und erstellte daraus ein aussagekräftiges Modell für einen Prozess, der bis dato noch nicht richtig verstanden wurde. Die Kenntnis über die bestehende Herausforderung, die identifizierten Parameter mit dem größten Einfluss auf den Prozess und die historischen Daten als Basis gewährleisten eine gute Genauigkeit hinsichtlich der Handlungsbedarfe. Ein weiterer entscheidender Vorteil dieser Vorgehensweise: für jeden Prozessbereich visualisierte das Projektteam die relevanten Daten in Dashboards, je nach Nutzer bzw. Nutzergruppe. Dies unterstützt den sicheren Umgang der Mitarbeiter:innen mit den prozessorientierten Daten maßgeblich.
Prädiktive Prozessentwicklung und -regelung
Die sehr gute Datenqualität der bisher angefallenen, aber nicht verwendeten Daten erwies sich als ideale Basis für die prädiktive Regelung des Produktionsprozesses. Schritt für Schritt ermittelte das Team die für den Prozess relevanten Daten und brachte diese mittels Algorithmen in Korrelation. Zum einen näherte man sich somit den letztendlich bestmöglichen Prozessen und Produktionsregelungen an, zum anderen sorgte die schrittweise erfolgende Durchführung für die neuen Fertigungsprozesse dafür, dass die Mitarbeiter:innen von Anfang an in die neue Vorgehensweise eingebunden waren.
Ein weiteres zentrales Projektziel lag darin, die beschriebene Vorgehensweise im Sinne eines modularen Einsatzes auf weitere, bereits in Betrieb befindliche Fertigungslinien erweitern zu können. Dies wurde durch die Planung und den Einsatz einer durchgehenden Digitalisierungsplattform und einer skalierbaren IoT-Architektur erreicht.
Zukunftsorientierte Lösung
In Summe ging es in diesem Projekt nicht darum, eine spezifische Lösung zu suchen und zu etablieren. Im Gegenteil, gemeinsam mit ROI-EFESO entwickelte und etablierte der Automobilzulieferer eine völlig neue, komplexe, skalierbare und somit zukunftsorientierte Lösung zur Prozessoptimierung und –steuerung. Die neuen Werkzeuge sind nicht nur auf einer spezifischen Anlage anwendbar, sondern können auf alle bestehenden Fertigungseinheiten in allen Werken ausgerollt werden. Entsprechend kann das Unternehmen nun notwendige Veränderungen – vor allem durch technologische Weiterentwicklungen und die daraus entstehenden Anforderungen – schnell und flexibel in die bestehenden Fertigungs- und Qualitätsmanagementprozesse integrieren.