Verbesserung der Qualität und Prozessstabilität
Unternehmen sind in Zeiten von digitaler Transparenz einem hohen Druck ausgeliefert, sich bei ihren Kunden und gegenüber der Konkurrenz zu behaupten. Nur eine große Rückrufaktion wegen Qualitätsproblemen kann ausreichen, eine Marke zu beschädigen und bedeutende Wettbewerbsvorteile zu verlieren. Der Ansatz der Qualitätsführerschaft und die Etablierung einer Zero-Defect-Kultur rücken daher zunehmend in den CEO-Fokus und werden zu einem bedeutenden Element in der Unternehmensstrategie.
Diese Entwicklung wird durch weitere Trends getrieben:
- Neben der Positionierung im externen Wettbewerb wird Qualität zunehmend auch wesentlicher Hebel zur Steigerung der Profitabilität gesehen
- Die Komplexität von Produkten und damit verbundenen Services nimmt weiter zu und erhöht mit einem damit einhergehenden steigenden Anteil von Software und Elektronik die Anforderungen in der Qualitätsabsicherung
- Immer kürzere Produkt- und Entwicklungszyklen begrenzen die Testzeiten und erfordern stabile Produktneuanläufe
- Regionen- und Markenübergreifende Baukästen und Plattformkonzepte potenzieren das Risiko von Qualitätsproblemen
- Sinkende Wertschöpfungstiefe erfordert Qualitätsmanagement über globale Lieferketten hinweg
- Digitalisierungs- und Analytics-Tools bieten völlig neue Ansätze im Qualitätsmanagement hin zu Qualität 4.0
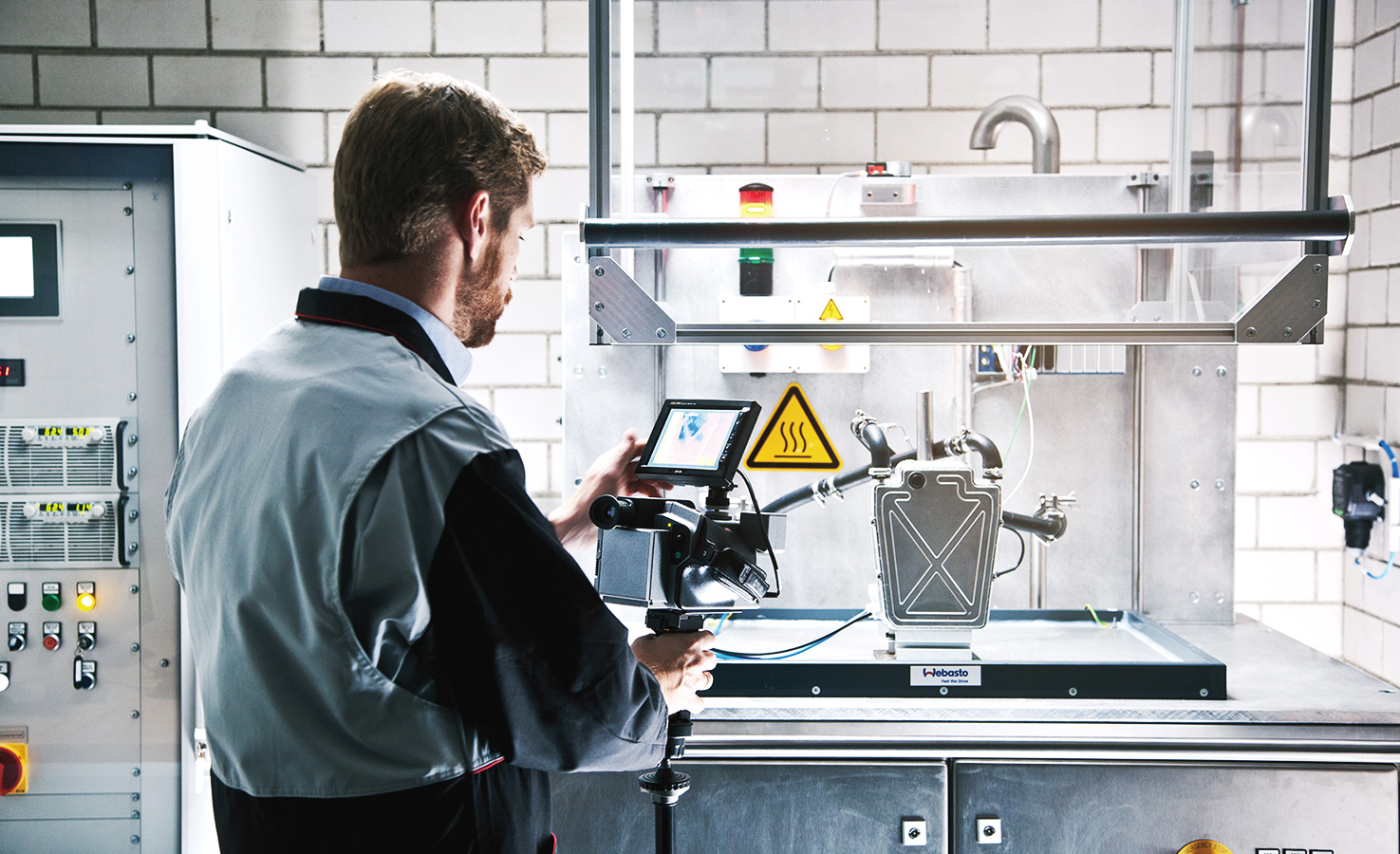
Vor diesem Hintergrund muss das Qualitätsmanagement neu aufgestellt und positioniert werden - in der Entwicklung beginnend über die gesamte Supply Chain und Wertschöpfungsprozesse hinweg bis hin zur Service- und Aftersales-Organisation.
Dabei geht es nicht nur um eine weiterentwickelte Organisation und Integration der Qualitätsbereiche, sondern primär auch um den Aufbau einer Null-Fehler-Kultur im Unternehmen mit stabilen und beherrschten Prozessen und einem einheitlichen Qualitätsbewusstsein und -verständnis über alle Ebenen hinweg. Dazu kommt die konsequente Nutzung neuester Technologien und der damit verbundene Know-how-Aufbau.
In diesem anspruchsvollen Umfeld ist die Unternehmensberatung EFESO ein zuverlässiger und erfahrener Partner und unterstützt Unternehmen von der Supply Chain über die Entwicklung und Produktion bis hin zum Kundenservice mit individuellen Programmen und Initiativen:
- Präventive Qualitätsabsicherung in der Produktentwicklung: Implementierung von Best-Practice-Prozessen und Methoden zur Reifegradabsicherung und Qualitätsvorausplanung. Absicherung von Prozessfähigkeiten und -freigaben. Professionalisierung und Absicherung von Produktneuanläufen. Robust Design durch Nutzung von Simulation Testing und Artificial Intelligence-Anwendungen, z.B. für FMEAs.
- Qualität in der Supply Chain: Lieferantenentwicklungsprogramme zur Absicherung der Produkt- und Prozessqualität in Anlauf und Serie. Task Forces zur Ursachenanalyse und Behebung von aktuellen Qualitätsproblemen. Programme zum Aufbau professioneller Strukturen zur Qualitätssicherung von Kaufteilen. Digitales Supplier-Performance-Tracking.
- Operative Qualitätsoffensiven und Programme zur Qualitätskostensenkung: Schaffung von Transparenz zu den „wahren Total Cost of Quality“ und deren Ursachen entlang der Wertschöpfungskette. Prozess-Stabilisierung und In-Line-Prozess-Kontrolle im Shop Floor. Schaffung kurzer Qualitätsregelkreise, eindeutiger Qualitätsstandards und schnell wirksamer Problemlösungsroutinen. Umsetzung Right-First-Time-Programme in indirekten Unternehmensfunktionen. Qualifizierung von Mitarbeiter:innen und Führungskräften zum Aufbau einer Null-Fehler-Kultur.
- Qualität 4.0. / Real Time Quality Control: Einsatz von Industrie 4.0 Technologien (Sensorik, Software) zur prädiktiven Qualitätsabsicherung über Echtzeitkontrolle von Produktion und Qualität. Aufbau digitaler Zwillinge, automatisierte Fehlererkennung, Nutzung von Advanced Analytics zur lernenden und automatisierten Ursachenanalyse. Real Time Visualisierung von Qualitätsdaten und Empfehlung zur Fehlerbehebungsansätzen. Umsetzung von Machine-Learning-Konzepten. Einsatz von Smart Tools für Produktions- und Qualitätsmitarbeiter:innen.
Der Aufbau einer Null-Fehler-Kultur ist kein Selbstläufer, sondern muss als Transformationsprozess verstanden werden. Dieser baut zum einen auf den klassischen Lean- und Qualitätsmanagement-Methoden auf, nutzt zum anderen aber sehr konsequent die umfassenden Möglichkeiten aus Digitalisierung und Analytik. Wenn es darüber hinaus gelingt, die Fähigkeiten und Qualifikationen der Mitarbeiter:innen und Führungskräfte entlang dieser Ansätze weiterzuentwickeln, dann erlaubt diese Strategie umfassende Möglichkeiten Qualitäts-, Ausschuss-, Nacharbeits- und Reklamationskosten signifikant zu senken und gleichzeitig die Produktivität der operativen Bereiche zu steigern.