THEMEN & NEWS
Beiträge und Interviews zu aktuellen Fach-, Technologie- und Branchenherausforderungen, Informationen zu unseren Beratungsangeboten, Seminaren und Events sowie Unternehmensthemen:
Hier erfahren Sie, was EFESO bewegt.
Interview
„KI schafft einen Mehrwert, sobald sie Synergieoptionen sichtbar macht.“
Experte: Dr.-Ing. Uwe Steinkötter, Partner, EFESO | 31.10.2024 | Teilen auf in
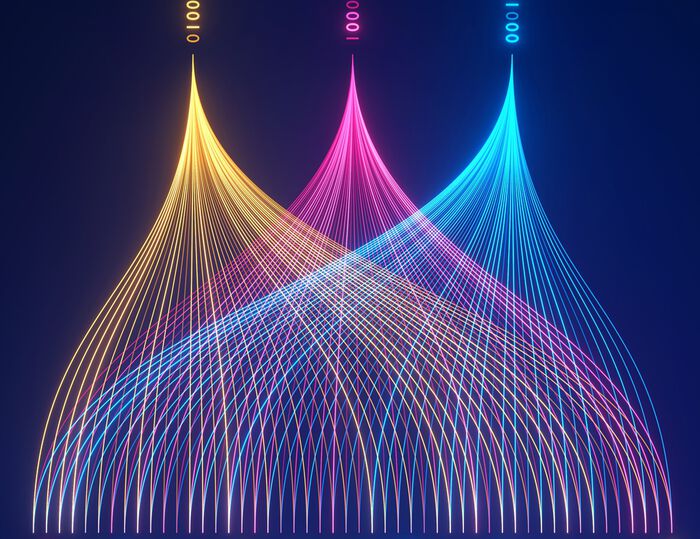
Industrial Recommendation Engine: Fertigungsdaten mit KI richtig nutzen
Herr Dr. Steinkötter, Fertigungsunternehmen erleben ihre Digitalisierung zuweilen als „Fahrt mit angezogener Handbremse“: sie erfassen bereits gigantische Datenmengen aus Maschinen und Prozessen, analysieren und visualisieren komplexe Informationen z.B. im Shopfloor Management – aber bemerken zugleich, dass der Impact ihrer IT-Investitionen größer sein könnte. Woran liegt das?
Uwe Steinkötter: Weil diese Schritte – Erfassen, Korrelieren, Visualisieren, Bewerten von Daten – per se nicht trivial sind und auch von progressiven Unternehmen viel abverlangen. Dennoch sind damit erst einmal nur die Grundlagen erfüllt, um bei der industriellen Digitalisierung mitzuspielen. Der Eindruck, mit bereits getätigten Investments nicht das volle Potenzial zu nutzen, kann auf zwei Versäumnisse zurückgehen. Zum einen, wenn in Digitalisierungsprojekten die „Sollbruchstelle“ zwischen Strategie und Umsetzung nicht kritisch hinterfragt wurde, etwa: Wie realistisch sind die gesetzten KPI? Was geschieht konkret in der Umsetzungsphase, wenn Strategieberater oder IT-Dienstleister nicht mehr mit an Bord sind?
Zum anderen entfaltet industrielle Digitalisierung ihr Potenzial, sobald man Vorstöße über das Feld der Fertigung hinaus unternimmt – erst in weitere direkte, dann indirekte Bereiche und perspektivisch sogar in Ökosysteme mit anderen Unternehmen. Hier ist man in Deutschland in der Regel mit der Situation konfrontiert, dass die IT-Infrastrukturen der Fertigung noch komplett abgekapselt sind von einem Cloud- oder anderen IT-Umfeld. Wer etwa noch Fertigungsrechner mit Windows XP nutzt und sich mit den Datenschutzrichtlinien für Cloud-Computing beschäftigt, will meist keine Eins-zu-eins-Verbindungen herstellen. Und bei der Ausarbeitung der Alternativen sollte man erneut die eben genannten Fragen beantworten können. Allerdings mit der Ergänzung, dass sich IT-Security-Investitionen rentieren, wenn bestimmte Situationen eben nicht eintreten. Das ist also gesondert zu betrachten neben den klassischen OEE, Taktzeit- und Effizienz-Themen.
Nun erleben wir aber auch, wie Künstliche Intelligenz (KI) die technologischen Rahmenbedingungen der industriellen Digitalisierung neu definiert. Wie beurteilen Sie diese Entwicklung?
US: Am Einsatz von KI führt für die Industrie kein Weg vorbei – aber KI löst auch keine Probleme per „Plug & Play“. Die Stärken von KI liegen heute darin, viele unterschiedliche Informationen auszuwerten und Prozessalternativen zu simulieren, also eher das Gesamtbild der Handlungsoptionen einer Fertigung bzw. weiterer Operations-Bereiche zu skizzieren und zu verbessern.
Die zwingende Voraussetzung dafür sind Informationen, die nach konkreten Vorgaben für die IT/OT-Architektur sowie zu den benötigten Daten von den Mitarbeitern erfasst werden. Eine solche Vorstellung, ein solches „Datenbild“ ist in vielen Unternehmen aber noch gar nicht vorhanden. Stattdessen wird nach Einzelfällen entschieden, etwa wenn ein Pilotprojekt aus dem Ruder läuft und das geplante Investment schon nach kurzer Zeit hinterfragt wird. Oftmals starten solche Pilotprojekte mit Anlagen oder Maschinen, mit deren Spezifikationen und Themen die Mitarbeiter bereits sehr gut vertraut sind – für die Datensammlung ist das sinnvoll, im „Datenbild“ aber eben nur eine „Farbe“ neben anderen.
Welches Vorgehen empfehlen Sie stattdessen?
US: Die direkte Arbeit an der Maschine verbleibt - datenseitig gesehen - von der Cloud entkoppelt. Die Auswertungen der Leistung, Betriebszustände etc. werden am Shopfloor vorgenommen, in die Cloud gespielt und mit dem einem gewissen Versatz in die Maschinennähe zurückgespiegelt, um Entscheidungen zu treffen. Dabei sollte man bereits die Themen bzw. Auswertungen nach „Echtzeit, Nahechtzeit, Langzeit“ unterteilen. Wer das nicht nur bei einem Piloten, sondern bei allen besonders relevanten Maschinen umgesetzt hat, kommt der Verwirklichung des Datenbildes seiner Fertigung ein großes Stück näher.
Die richtige Wahl der Zeitspanne ist hierbei wichtig: dies eröffnet unterschiedliche Optionen, zeitnah in den Prozess eingreifen bzw. ihn steuern zu können. Zudem sind die Kosten für die Auswertungsgeschwindigkeit in der Cloud zu berücksichtigen. Einige Entscheidungen wie der Wechsel von Filtern oder Werkzeugen in den Anlagen haben einen gewissen Vorlauf und müssen daher nicht in Echtzeit oder Nahechtzeit getroffen werden – entsprechend lassen sich Kosten im Cloud-Computing einsparen.
KI löst keine Probleme per „Plug & Play“.
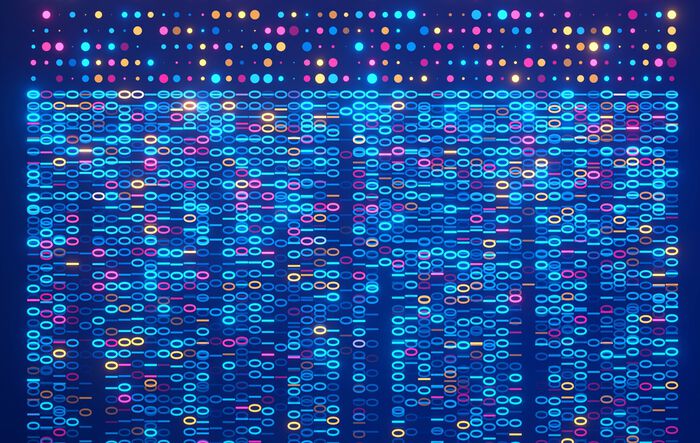
Ab welchem Punkt sollten sich Investitionen in KI-Technologien als nützlich erweisen?
US: Spürbare Nutzeneffekte ergeben sich meiner Erfahrung dann, wenn zusätzlich zum Menschen eine KI das das beschriebene Datenbild der unterschiedlichen Maschinen im gesamten Fertigungsprozess „betrachtet“. KI schafft hier einen Mehrwert, sobald sie Synergieoptionen sichtbar macht, die man an der Einzelmaschine nicht wahrgenommen hat. Und die auch ein Mitarbeiter mit seinem Erfahrungswissen nicht sehen kann, da er gar nicht weiß, was in den vorherigen Prozessschritten passiert ist. Diese KI-relevanten Aspekte – Überwachen, Simulieren, Prognostizieren, Handlungsempfehlungen geben – erfordern die Auswertung einer ganzheitlichen Systematik.
Gibt es weitere Voraussetzungen für einen solchen KI-Einsatz?
US: Eventuell muss die IoT-Infrastruktur erweitert werden, um zusätzliche Daten zu erfassen. Je nach Einsatzfeld z.B. Sensorik zu relevanten Messwerten oder Tracking-Technologie zum Aufbau digitaler Prozesszwillinge in der Fertigung und in den Lieferketten. Der gemeinsame Nenner besteht darin, all diese Daten in einen einheitlichen Daten-Pool einzubringen. Mit dieser Datenbasis lohnt es sich, zwei Varianten der Auswertung zu erstellen: einmal mit einer Wissenslogik, also z.B. durch einen Data Analyst – und zusätzlich vorgabenfrei, etwa eine Mustererkennung über Power BI. So gewinnt man bereits viele, oftmals ganz neue Erkenntnisse.
Das erfordert allerdings auch einen gewissen Reifegrad beim Grundlagenwissen, der sich je nach Fertigungskontext unterschiedlich bemisst. Im Kern geht es darum, einen digitalen Produktzwilling zu erstellen – was wurde zu welcher Zeit auf welcher Maschine gefertigt? Wo befindet sich welches Produkt oder welche Komponente in der internen oder externen Logistik? Im Endeffekt sollte das Produkt also eindeutig zugeordnet werden können, damit die KI die Prozesssteuerung effektiv unterstützen kann.
Erfahren Sie von Dr.-Ing. Uwe Steinkötter, wie Sie die Digitalisierung im Unternehmen ergebnisorientiert vorantreiben.
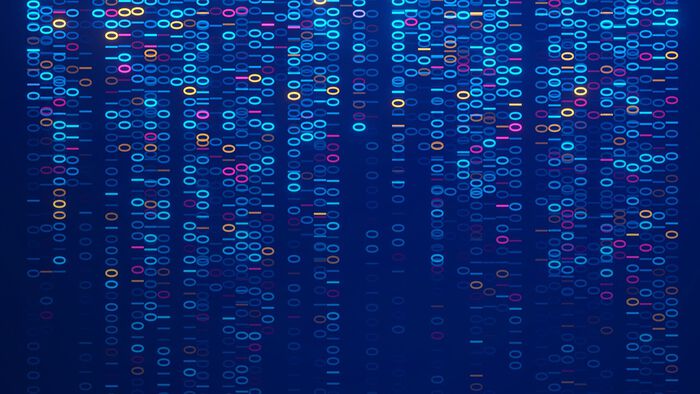
Perspektivisch kann die KI also nicht nur kontrollieren und warnen, sondern auch proaktiv Handlungsempfehlungen geben. Solche „Recommendation Engines“ (deutsch: Empfehlungssysteme) schlagen uns z.B. auf Web-Portalen und Social-Media-Plattformen personalisiert Produkte und Themen vor, die sie aus unserem Online-Verhalten ableiten. Wie können Unternehmen eine „Industrial Recommendation Engine“ aufbauen?
US: Das hängt zuerst davon ab, ob sie eine Massenfertigung betreiben – oder hochspezialisiert in Losgröße 1 bzw. in sehr geringen Stückzahlen fertigen. Im ersten Fall wird die „Industrial Recommendation Engine“ im Vorfeld mit Daten und Parametern aus der Fertigung trainiert, lernt also selbstständig anhand dieser Informationen. Das sind in der Regel Use Cases zu klassischen Themen wie Qualitätskontrolle bzw. Fehlererkennung: zuerst lernt das System z.B., was ein Fehler ist oder ein „Gutteil“ und ein „Schlechtteil“, häufig über Bilderkennungssoftware.
Hier haben wir übrigens die Erfahrung gemacht, dass KI in einem solchen Lernprozess menschliche Logik adaptieren kann: waren die Trainingsbilder mit den Symbolen „Daumen rauf“ und „Daumen runter“ gekennzeichnet, achtete die KI nach kurzer Zeit nur noch auf diese Parameter – schließlich wurde sie ja aus ihrer „Sicht“ so trainiert. In diesem Fall sind also gut überlegte Trainingsregeln wichtig. Außerdem benötigen wir eine hohe Masse an Vorgängen, um überhaupt erst ein Schlechtteil aus dem Prozess zu erhalten und dann eine Korrelation zu den vorherigen Prozessschritten herstellen zu können. In einer gut aufgestellten Fertigung sprechen wir von 1-3ppm, also einem bis drei Schlechtteilen pro einer Millionen Teile insgesamt.
Bei der Einzelfertigung steht diese statistische Masse aber nicht zur Verfügung …
US: Richtig, bei geringen Stückzahlen wie in einer Anlagenfertigung wird KI anhand anderer Parameter trainiert. Hier identifiziert sie eher Fehler bei den Rüstvorgängen, fehlende bzw. falsche Werkzeuge und Materialien oder Montagefehler im Produkt. Der Aufbau einer „Industrial Recommendation Engine“ bezieht sich hier also eher auf eine assistierende Kontroll- und Empfehlungsfunktion, die den Arbeitsprozess erleichtert und absichert. Natürlich ließen sich auch in diesem Fall Produktparameter wie Schweißnähte fotografieren und als Datenbasis zur Fehlersenkung im KI-Training verwenden. Diese Datenbasis sollte man aber zwecks besserer Einordnung mit generischen Schweißdaten oder Daten von Maschinenherstellern anreichern und abgleichen.
Ein KI-Einsatz mag wirtschaftliche KPI adressieren, zugleich wird er aber auch die Entwicklung der Organisation und Kultur im Unternehmen beeinflussen. Welche Erfahrungen und Empfehlungen aus Best Practice Projekten können Sie hierzu nennen?
US: Erwartungsmanagement ist immer wieder ein wichtiges Thema – wie erwähnt kuriert KI in den seltensten Fällen Probleme im Schnellverfahren. Wir zeigen in unseren Digitalisierungsprojekten daher realistische, fallbezogene Perspektiven auf, bei KI und auch bei allen anderen Technologien. Dabei arbeiten wir z.B. genau heraus, welche Technologie für welchen Einsatzzweck am sinnvollsten ist. Bei KI-Anwendungen geht es inzwischen auch häufiger um das Thema „Entscheidungsgewalt“. Diese verbleibt in der Regel beim Mitarbeiter, aber dank KI trifft er diese Entscheidungen eben anhand einer größeren Datenbasis und besseren Prognosegenauigkeit. Die KI ist also aktuell in der Assistentenrolle und wird dort auch voraussichtlich noch in den nächsten Jahren verortet sein.
Der Change-Aspekt des Themas ist aber tatsächlich sehr wichtig. Wenn KI als Assistent immer mehr Mitarbeiter befähigt, immer mehr Entscheidungen zu treffen, verändert das das Verständnis und die Aufgaben von Führung enorm. Allein durch die zeitliche Taktung: stellt die KI Informationen viel schneller zur Verfügung, müssen auch mehr Entscheidungen auf untere Ebenen delegiert werden. Einige Regel-Meetings mit der Leitungsebene können schnell passé sein, wenn Maschineneinrichter und -bediener alle relevanten Daten direkt zur Verfügung stehen und damit Schritt für Schritt auch Entscheidungskompetenzen verlagert werden. Best Practice Unternehmen lösen das mit der entsprechenden Befähigung dazu, aus der einen Richtung „loszulassen“ – und aus der anderen, diese Rolle annehmen und übernehmen zu können.
Mehr erfahren über Digitalisierungslösungen für die Industrie
Digitalisierung, Industrie 4.0 und IIOT >
![]() |
Thank you for Signing Up |

