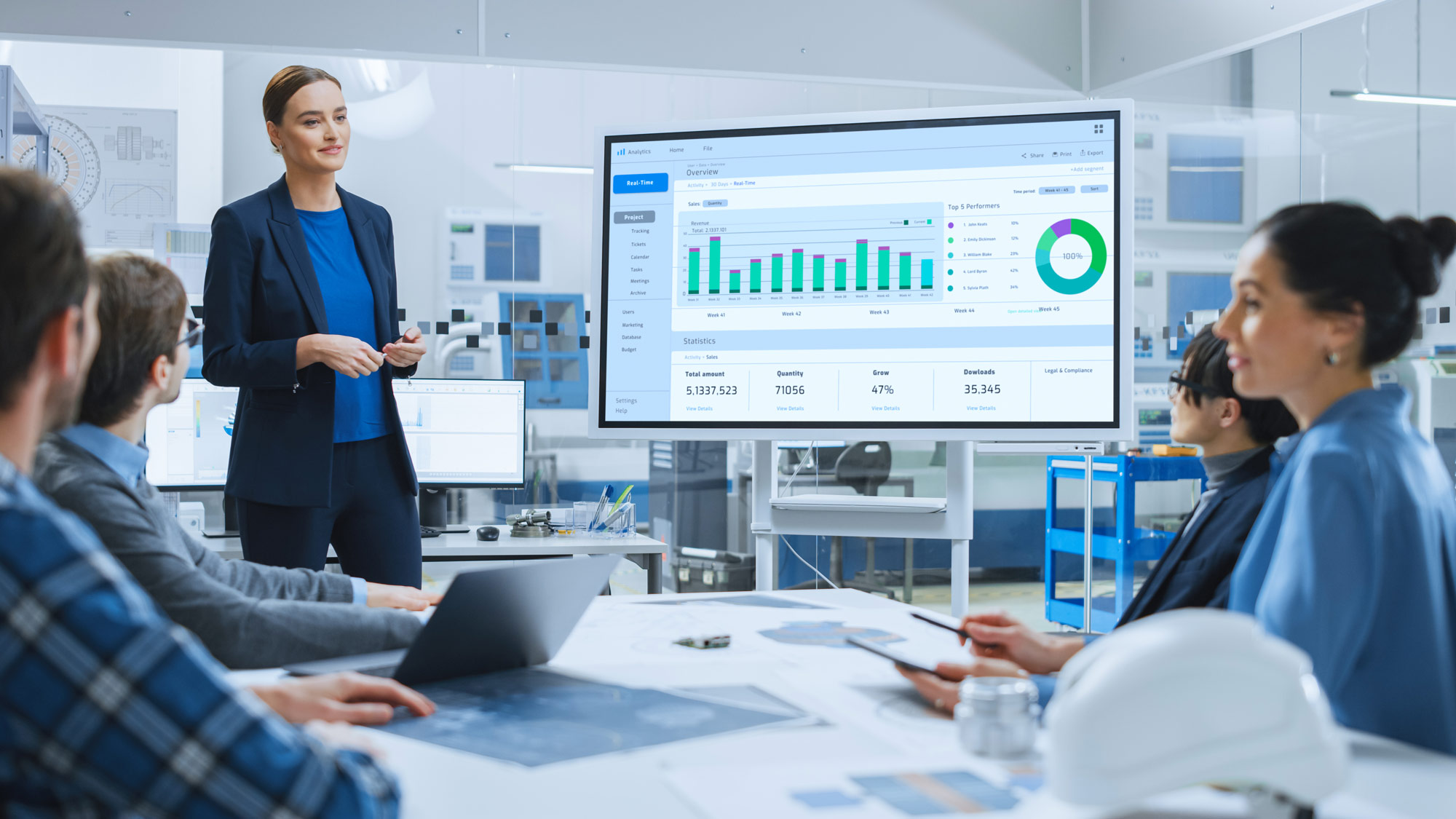
Prozesse stabilisieren und Kosten senken
Lamb Weston / Meijer steigert das Leistungsniveau seiner Werke.
Als eine der wichtigsten Nutzpflanzen der Welt ist die Kartoffel der entscheidende Protagonist in diesem Fallbeispiel. Die Nachfrage nach Kartoffelprodukten steigt weiterhin deutlich. Das erfordert von allen Akteuren im Markt, möglichst viele Schritte im Wertschöpfungsprozess kontinuierlich zu verbessern, sei es z.B. durch einen ökologischen Anbau oder mit neuen Technologien und anderen Innovationen bei der Verarbeitung. In diesem Fall baute das niederländische Unternehmen Lamb Weston / Meijer seine Position als weltweiter Branchenführer im Markt der Tiefkühlkartoffelprodukte weiter aus. Mit EFESO reduzierte es u.a. die Betriebskosten in der Fertigung seiner größten Werke, verbesserte die Planungsprozesse und realisierte in acht Monaten Einsparungen von insgesamt 4,5 Millionen Euro.
Herausforderung
Lamb Weston / Meijer ist Branchenführer im globalen Markt der Tiefkühlkartoffelprodukte. Mit EFESO will das Unternehmen Betriebskosten reduzieren und eine kontinuierliche Verbesserung der Produktionsprozesse erreichen.
MEHREFESO Lösungsansatz
Durchführung eines sechsmonatigen Verbesserungsprogramms mit Ergebnispräsentationen in zweimonatigen Zyklen. Zudem wurde ein Performance Control Systems (PCS) eingeführt.
MEHRLessons Learned
Im Fokus sollten nicht nur Kostensenkungen stehen. Wichtig ist zudem, die Mitarbeiter:innen in der Produktion zur kontinuierlichen, proaktiven Verbesserung der Arbeitsabläufe zu befähigen und zu motivieren.
MEHRFertigungsabläufe im Blick
Lamb Weston / Meijer liefert Tiefkühlkartoffelprodukte und dehydrierte Kartoffelflocken an Kunden im Foodservice, Quick Service, in der Industrie sowie im Einzelhandel im EMEA-Wirtschaftsraum. Mit 1.400 Mitarbeiter:innen betreibt das Unternehmen sechs Produktionsstätten in drei Ländern. Um seine Marktposition zu stärken und auszubauen, nahm es die Fertigungsabläufe in den beiden größten Werken genau unter die Lupe. Es galt, die Zuverlässigkeit des Produktionsprozesses zu verbessern und zugleich Kosten an allen Standorten zu senken. Diese Ziele sollten mit Trainings und Maßnahmen zur Stärkung der Unternehmenskultur untermauert werden. Im gemeinsamen Projektteam entwickelten Lamb Weston / Meijer und EFESO Lösungswege für diese Aufgaben.
Einsparungen von 4,5 Millionen Euro wurden in acht Monaten realisiert.
Lösungsansatz von EFESO
Im Vorfeld des Projektes erstellte das Unternehmen einen High-level Business Case für die beiden größten Produktionsstandorte, um Verbesserungspotenziale transparent zu machen und Leitlinien für das Projekt mit EFESO sowie für den Roll-out in den weiteren Werken zu schaffen. Für diesen Business Case stellte Lamb Weston / Meijer ein Team aus jungen Führungskräften und „High Potentials“ aus mehreren Standorten zusammen. Dieses Team sollte sich ausschließlich darauf konzentrieren, die erforderlichen Veränderungen im weiteren Projektverlauf zu steuern.
Alle acht Wochen wurden die erreichten Ergebnisse festgehalten.
Außerdem mussten die Fertigungsteams in den Standorten trainiert werden, um eine Kultur der kontinuierlichen Verbesserung aufzubauen und weiterzuentwickeln. Da EFESO über Expertise für genau diese Leistung in hochspezialisierten Branchen verfügt, entschied sich Lamb Weston / Meijer für die Zusammenarbeit. Der Lösungsansatz des gemeinsamen Projektteams konzentrierte sich auf zwei Elemente:
- ein sechsmonatiges Verbesserungsprogramm, in dem die erreichten Ergebnisse alle acht Wochen in separaten Abschnitten festgehalten und von den Mitgliedern der Werksleitungsteams regelmäßig vor den Lenkungsausschüssen präsentiert wurden.
- die Einführung und Nutzung eines Performance Control Systems (PCS), das direkt mit einem Verbesserungskreislauf verknüpft ist, unterstützt durch Human Dynamics (HD).
Lessons Learned
Als zentraler Erfolgsfaktor erwies sich die Fähigkeit des Projektteams, die Mitarbeitermotivation und die „menschliche Dynamik“ in den Business-Case-Projekten an beiden Standorten zu berücksichtigen. Wichtig war, das Interesse und die Energie der hochmotivierten Belegschaft nicht nur auf die Ziele der Kostensenkung zu lenken, sondern diese darüber hinaus für eine kontinuierliche, proaktive Verbesserung der Arbeitsabläufe zu sensibilisieren und zu befähigen.
Außerdem profitierte das Unternehmen davon, dass eine intensive Zusammenarbeit des Projektteams mit dem Standortteam (Management und Mitarbeiter:innen) gelang – vom ersten Tag an bis zum Projektabschluss. Dies stellte sicher, dass die Verantwortung für die implementierten Verbesserungen übernommen wurde. Auch die wöchentliche Kommunikation über Fortschritte und Erfolge erhöhte das Engagement.
Die Aufmerksamkeit für Verbesserungen sollte sich nicht nur auf Kostensenkungen richten.
Erfolgsmodell von EFESO
Das Verbesserungsprogramm startete mit einem Bootcamp, in dem EFESO das zentrale Steuerungsteam dahingehend trainierte, wie die Methoden und Tools, u.a. eine Root Cause Analysis (Fehler-Ursachen-Analyse) oder Human Dynamics (HD), eingesetzt werden können. Danach erfolgte eine ganzheitliche Analyse des gesamten Standortsystems: zum aktuellen Process Control System (PCS), zur Overall Equipment Effectiveness (OEE), zu Materialverlusten sowie dem HD-Status. Anhand dieser Ergebnisse konzipierte und realisierte das Projektteam die erste Welle an Verbesserungen, an die sich eine zweite direkt anschloss.
In der Analysephase identifizierte das Projektteam Engpässe und Verluste. Der bereits vom Unternehmen erstellte High-level Business Case wurde dabei in einen detaillierten Business Case umgewandelt. Um die Verluste und Engpässe zu beseitigen, arbeiteten mehrere Verbesserungsteams nun mit HD-Methoden, etwa in Workshops, 1-on-1-Gesprächen mit den Maschinenbedienern oder im Dialog mit weiteren Mitarbeiter:innen. Dabei stand u.a. im Vordergrund, Widerstände zu verstehen sowie Rollen und Verantwortlichkeiten zu klären – aber zu zeigen, wie man ein konstruktives Feedback gibt und erhält.
In zwei Verbesserungswellen wurden Engpässe und Verluste behoben.
Projektergebnisse der Werksstandorte
Mit diesem Erfolgsmodell von EFESO erzielte das Unternehmen eindeutige Resultate im erfolgreich abgeschlossenen Projekt:
- Einsparungen von insgesamt 4,5 Millionen Euro innerhalb von acht Monaten realisiert
- Gesamtanlageneffektivität um 2,2% im einen sowie um 3,6% im zweiten Werk erhöht
- 55% bzw. 21% weniger Abfall in den beiden Werken
- Qualitätsmängel in einem Werk um 32% reduziert