THEMEN & NEWS
Beiträge und Interviews zu aktuellen Fach-, Technologie- und Branchenherausforderungen, Informationen zu unseren Beratungsangeboten, Seminaren und Events sowie Unternehmensthemen:
Hier erfahren Sie, was EFESO bewegt.
Durchbrechen der Komplexitätsschallmauer
Lean Production beruht auf dem Prinzip der Komplexitätsreduktion. Doch angesichts steigender Anforderungen moderner Produktionssysteme im Hinblick auf die von den Kunden geforderte Geschwindigkeit, Flexibilität und Varianz stoßen klassische Lean-Ansätze immer häufiger an ihre Grenzen. Eine Trainingssimulation von ROI sensibilisiert Mitarbeiter für die Folgen steigender Anforderungen im Fertigungsprozess und zeigt gleichzeitig neue Wege für einen digital unterstützten Lean Production-Ansatz auf.
Ein Traktoren-Hersteller erhöht auf einen Schlag die Zahl seiner Ausstattungsvarianten um ein Vielfaches. Die Folgen in der Produktion sind sofort spürbar: Durchlaufzeiten verlängern sich, die Fehlerrate in der Montage nimmt zu und bereits erlernte Lean-Prinzipien werden wieder aufgegeben. Als Reaktion führt das Unternehmen digitale Systeme, wie etwa Sequenced Material Staging oder Intelligentem Routing, in der Montage ein – mit Erfolg: Die Produktivität gewinnt wieder an Fahrt, die Qualität verbessert sich. Die Montagelinie läuft trotzt höherer Variantenvielfalt stabil.
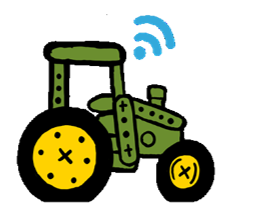
Die Grenzen der Vereinfachung
Was sich normalerweise innerhalb von Jahren oder sogar Jahrzehnten abspielt, erfolgt hier in 2-3 Stunden. Denn das beschriebene Szenario ist keine reale Montage, sondern Teil der ROI-Lean Digital-IoT-Simulation. Dort erleben die Teilnehmer im Zeitraffer das, was sich in vielen Unternehmen meist schleichend vollzieht: Hohe kundenspezifische Individualisierung, immer kürzere Lieferzeiten und umfassendere Produkt-Features sorgen für mehr Komplexität und höheren Steuerungsaufwand. Trotz lean-optimierter Prozesse wachsen Fehleranfälligkeit und Verschwendung im System; der Anteil der nicht-wertschöpfendenden Tätigkeiten nimmt extrem zu. Kurzum: die klassischen Lean-Ansätze stoßen an ihre Grenzen – die Prozesse sind vom Menschen nicht mehr beherrschbar.
Genau hier setzt die ROI-Simulation an und unterstützt den Übergang vom klassischen Lean Production- hin zu einem Lean Digital-Ansatz. Dazu wird der Montage-Prozess eines Traktorenherstellers mithilfe von Lego-Bauteilen nachgespielt. In drei Spielrunden übernehmen bis zu acht Teilnehmer verschiedene Aufgaben, wie etwa Montage-Tätigkeiten, Logistik und Qualitätskontrolle, mit dem Ziel innerhalb einer siebenminütigen Schicht möglichst viele Traktoren fehlerfrei zu produzieren. Von Runde zu Runde verändern sich dabei die Rahmenbedingungen für die Teilnehmer, um sie für die steigende Komplexität im Montageprozess und mögliche Gegenmaßnahmen zu sensibilisieren:
- Spielrunde 1: Klassisch optimierte Lean Production mit einer Variante
In der ersten Runde der Simulation wird eine einzige Produktvariante des Traktors in einer nach Lean-Prinzipien optimierten Montagelinie gefertigt. An fünf Montage-Arbeitsplätzen führen die Teilnehmer standardisierte Montage-Prozesse durch. Die benötigten Bauteile werden just-in-sequence vom Routenzug angeliefert. Die Teilnehmer erleben, wie eine ausgetaktete Montagelinie unter Berücksichtigung der klassischen Lean-Prinzipen, wie One-Piece-Flow oder Kanban-Nachschubsysteme eine hohe Produktivität und geringe Fehlerquote ermöglicht.
- Spielrunde 2 – Lean Production mit stark erhöhter Komplexität (über Varianz)
In Spielrunde zwei wird die Zahl der Produktvarianten von einer auf über 10.000 Varianten erhöht. Dadurch steigt die Komplexität im Gesamtprozess: So übernimmt, zusätzlich zu den bisherigen Rollen, ein Teilnehmer die Fertigungssteuerung, indem er die zu den Kundenaufträgen passenden Stücklisten zusammenstellt und in die Montage einsteuert. An den Montagearbeitsplätzen selbst steigt die Komplexität, indem die Mitarbeiter dort plötzlich mit unterschiedlichen Montageschritten und neuen Arbeitsanweisungen konfrontiert sind, die sie erst heraussuchen müssen. Diese zusätzlichen Arbeitsschritte führen schnell zu einer Lähmung des Gesamtsystems. Konnten in der ersten Spielrunde noch 14 Traktoren gefertigt werden, sind es in dieser Runde durchschnittlich zwei Stück. Die Teilnehmer erleben dadurch, wie die meist schleichenden Veränderungen im Produktionssystem die Produktivität massiv beeinflussen können und klassische Lean-Prinzipen angesichts zunehmender Komplexität alleine nicht mehr greifen.
- Spielrunde 3 – Lean Production mit stark erhöhter Komplexität und Unterstützung durch Industrie 4.0-Elemente
In Runde drei wird die Montagelinie von analoger auf digitale Steuerung umgebaut. Statt schriftlicher Arbeitsanweisungen, Produktionsaufträgen und Stücklisten in Papier befinden sich an den einzelnen Montagestationen Tablets, die mit einer cloudbasierten Produkt-Datenbank verknüpft sind. Neue Aufträge werden über einen Produktkonfigurator direkt dort eingespeist. Die dazugehörigen Auftragsdetails sind in einem RFDI-getaggten Behälter hinterlegt. Durch Scannen des Behälters an jeder Arbeitsstation erhalten die Montagemitarbeiter jeweils die passende Arbeitsanweisung und Visualisierung auf ihrem Tablet. Zudem werden nur die Teile just-in-time angeliefert, die für den jeweiligen Arbeitsschritt tatsächlich benötigt werden. Diese und weitere Industrie 4.0-Element verringern die Such- und Prüfaufwände entlang der Montagelinie erheblich. Die Teilnehmer erleben dadurch, wie digital vernetzte Technologien und Assistenzsysteme die gestiegene Komplexität im Montageprozess beherrschbar machen, Prozessstabilität und Produktivität sichern und eine Lean Production sinnvoll ergänzen.
Komplexität auslagern statt reduzieren
Die Simulation sensibilisiert Produktionsverantwortliche für die Weiterentwicklung ihrer Produktionssysteme und Lean-Ansätze – und zwar in zweifacher Hinsicht: Einerseits, indem sie erlebbar macht, wie eine Komplexitätszunahme im Montage- bzw. Logistikprozess das Gesamtsystem massiv beeinflussen und klassische Lean-Methoden zur Beherrschung der Komplexitätszunahme nicht mehr ausreichen. Andererseits, indem sie die Möglichkeiten digitaler Assistenzsysteme im Montageprozess praktisch demonstriert und die Vorteile für die Teilnehmer aufzeigt.
Dadurch wird deutlich, dass Lean und Industrie 4.0 nicht nur aufeinander aufbauen, sondern auch ein gemeinsames Ziel verfolgen, nämlich die Beherrschung von Komplexität. Allerdings unterscheidet sich dabei die Herangehensweise: Denn während Lean Arbeitsprozesse so klar wie möglich definiert und in beherrschbare Einzelteile zerlegt, nehmen digitale Lösungen die Komplexität vom Menschen weg, lagern sie aus, und halten Sie vom Mitarbeiter fern.
Für ein nachhaltig erfolgreiches Produktionssystem, das den heutigen Anforderungen an Flexibilität und Varianz gerecht werden möchte, müssen beide Komponenten berücksichtigt werden. Das gilt in der Simulation ebenso wie in der industriellen Wirklichkeit.