Globale Qualitätsstandards für Komplexität-Kunstwerke
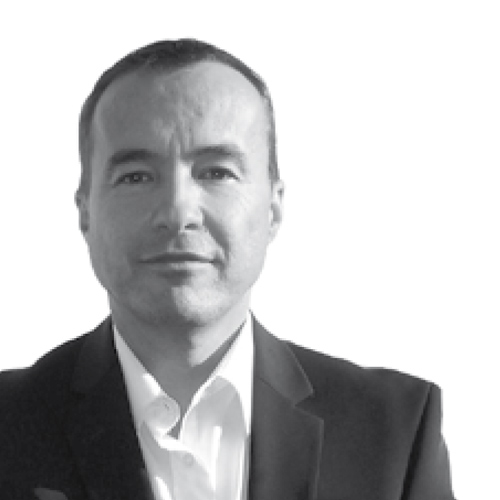
Operative Exzellenz abgesichert durch Qualitätsmanagement-Software
Mit über 20 Standorten weltweit ist die Miba AG als Zulieferer für die Motorenund Fahrzeugindustrie ein erfahrener Global Player. Im Projekt ‚one.miba‘ schafft das Unternehmen eine einheitliche und ausrollbare Prozess- und IT-Landschaft in den vier Schlüsselbereichen Technologie- und Produktentwicklung, Supply Chain Management und Qualität. So beherrscht Miba nicht nur die zunehmende Komplexität seiner Märkte besser, sondern stellt auch eine hohe Transparenz im Qualitätsmanagement sicher. Familienkutsche, Freizeit-Rennwagen oder zweites Wohnzimmer: Autofahrer betrachten ihr Fahrzeug je nach Nutzen ganz unterschiedlich. Seltener jedoch ist die Wahrnehmung als ‚Komplexitäts-Kunstwerk‘. Dabei besteht zum Beispiel ein VW Tiguan aus rund 25.000 Einzelteilen. So viele Komponenten wirtschaftlich in kurzer Zeit mit höchsten Qualitätsansprüchen zu verbauen, ist eine Komplexitätsdimension. Die zweite Dimension liegt in der logistischen Zusammenführung der Teile, von denen, je nach Fahrzeugtyp, bis zu 70 Prozent von Zulieferern stammen können. So produziert auch die Miba AG zahlreiche Automotive-Komponenten wie Zahnräder, Kettenräder, Zahnriemenräder, Hauptlagerdeckel oder Öl- und Wasserpumpen, die in bester Qualität und perfekter logistischer Koordination an Kunden rund um die Welt geliefert werden müssen.
Die Grundierung: Koordinierte IT-und Geschäftsprozesse
Analog zu einer grundierten Leinwand, bildet die IT-gestützte Operational Excellence nicht nur die stabile Grundlage, sondern spielt eine Schlüsselrolle in den globalen Wertschöpfungsketten von Miba. Mit dem Programm ‚one.miba‘ hat das Unternehmen die hierfür erforderliche Prozess- und IT-Landschaft an bereits acht globalen Produktionsstandorten geschaffen. „Bei ,one.miba‘ geht es vor allem um das möglichst perfekte Zusammenspiel zwischen Mitarbeitern und IT – und zwar über sprachliche, kulturelle und technologische Grenzen hinweg“, erklärt Günter Reittinger, Leiter des Qualitäts-Projektes bei der Miba AG. „Es gab bei Projektbeginn klare Anforderungen an die Prozesslandschaft. Diese muss nicht nur über stabile, sichere und sinnvoll standardisierte Prozesse verfügen, sondern auch auf weitere Standorte leicht ausrollbar sein. Außerdem sollen die Mitarbeiter Best Practices austauschen und so zum Beispiel Ideen zur Qualitätssteigerung schnell miteinander teilen können.“
Mit Unterstützung der Unternehmensberatung ROI und des IT-Dienstleisters IBS AG startete Miba im Juni 2013 ein gesondertes Projekt für den Schlüsselbereich Qualität, dessen Abschluss bis Mitte 2015 geplant ist. „Bei zwei Themen darf man sich in globalen Netzwerken keine Nachlässigkeit erlauben: erstens sind Disziplin, Effizienz und Transparenz in den Qualitätsprozessen ständig zu prüfen und zu verbessern. Zweitens benötigt man IT-Strukturen, die Qualitätsdaten aus möglichst vielen Stationen der Wertschöpfungskette zu jeder Zeit verfügbar und auswertbar machen. Genau dies treiben wir mit Erfolg im Qualitätsprojekt voran – schon in den ersten Monaten ist der Aufwand für Qualitätsarbeit deutlich gesunken“, sagt Günter Reittinger.
Die richtige Maltechnik: Klare Abläufe dank Qualitätsregelkreis
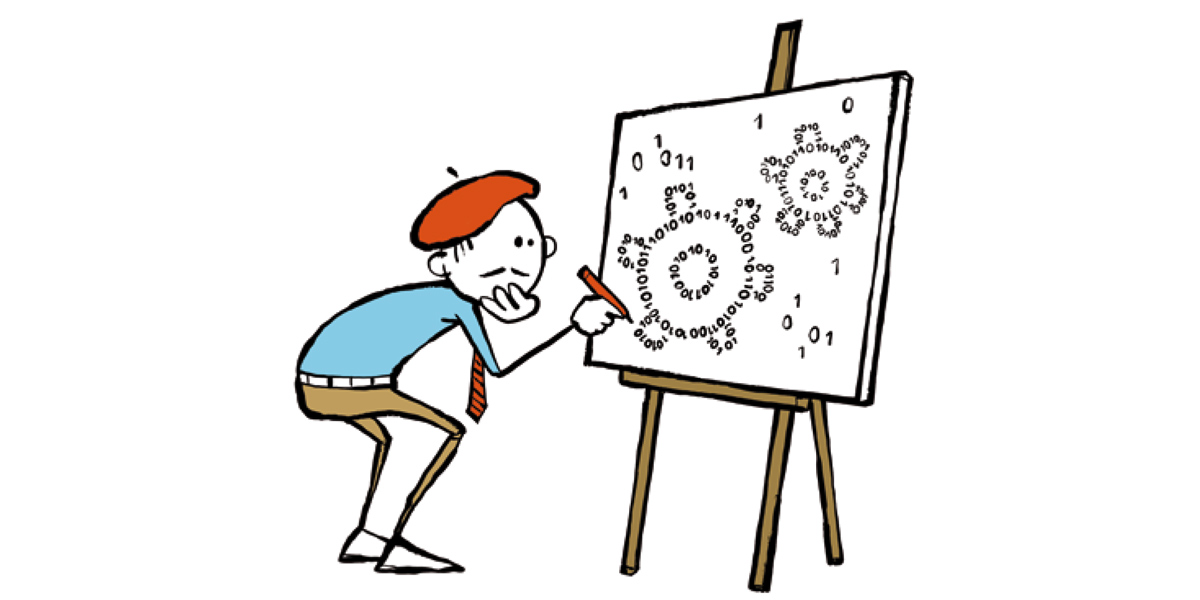
Um diese Ziele zu erreichen, entschied sich das Projektteam für eine IT gestützte Umsetzung des Qualitätsregelkreises. Mit dieser Methode verbesserte das Team die Qualitätsprozesse der Fertigungsstandorte anhand von vier ineinandergreifenden Etappen:
1. PLAN: Entwicklung einer Qualitätsstrategie mit konkreten Zielen bzw. KPI
2. DO: Umsetzung der Qualitätsvorausplanung
3. CHECK: Prüfdaten sammeln und analysieren, Audits durchführen
4. ACT: Maßnahmen ableiten, Produktverbesserungen initiieren und eine erfolgreiche Umsetzung der Strategie sicherstellen
Realisierbar waren diese Schritte jedoch nur mit der Implementierung einer neuen CAQ-Software (CAQ = Computeraided quality, Qualitätsmanagement Software). Um ein möglichst konkretes Bild von deren Leistungsanforderungen zu erhalten, bezog das Projektteam den Unternehmensvorstand, die Qualitäts-Manager und die Key-User ein. Dies bedeutete zwar in der Implementierungsphase einen hohen Kommunikations- und Abstimmungsaufwand, zahlte sich jedoch durch eine schnelle Anwendbarkeit der Software im operativen Tagesgeschäft aus. „Wir konnten den Aufwand in mehreren Arbeitsabläufen deutlich reduzieren. Außerdem können die Mitarbeiter nun auf alle relevanten Daten zugreifen, um im Falle einer Reklamation die Ursache schnellstmöglich zu ermitteln und zu beheben“, erläutert Günter Reittinger. „Wichtig für einen gelungenen Rollout dieses Vorgehens in anderen Standorten sind sowohl technische als auch organisatorische Schritte. Das können Handbücher, aber auch regelmäßige Trainings sein. Zentral ist zudem, Maßnahmen und Entscheidungen für die Mitarbeiter strukturiert und vollständig zu dokumentieren.“
Den eigenen Qualitäts-Stil finden: Fehler reduzieren, Best Practices teilen
Obwohl das Projekt noch nicht abgeschlossen ist, realisierte das Team den Rollout in allen acht Werken, die SAP/ CAQ einsetzen. Die Produktionsstandorte verfügen somit bereits heute über
• standardisierte Qualitäts-Prozesse (z.B. für interne und externe Reklamationen),
• einheitliche Schnittstellen beim ERPSystem und der Betriebsdatenerfassung,
• eine verbesserte Prozessintegration (z.B. hinsichtlich eines Prüfplans, der Reklamationsabwicklung und des Produktentstehungsprozesses)
• eine einheitliche und zeitnah verfügbare Datenbasis sowie ein standardisiertes und standortübergreifendes Reporting.
„Vor allem die einheitliche Datenbasis ist mit Blick auf die Zukunft eine typische ‚Big-Data-Herausforderung‘, die wir jetzt gelöst haben. Denn damit können wir nicht nur die Leistung der einzelnen Standorte auf Knopfdruck abrufen, sondern auch im Standortnetzwerk flexibler handeln. Mit den softwaregestützten Benchmarkings und Fehleranalysen ermitteln wir Qualitätsengpässe und Best Practices schneller und leiten entsprechende Maßnahmen direkt ein“, so der Projektleiter. Den nächsten Projektschritten sieht Günter Reittinger entsprechend optimistisch entgegen: „Wir planen derzeit den Roll-Out auf die Werke in China und ein Werk in England. Dabei werden wir auch weiterhin mit einer koordinierten Weiterentwicklung der vorhandenen Standards die Komplexität im Management des Netzwerkes senken und die Qualität unserer Produkte erhöhen.“
IBS AG
Als weltweit tätiges Softwareunternehmen bietet die IBS AG seit 1982 Softwarelösungen und Dienstleistungen für das Produktivitätsmanagement in Industrieunternehmen. Gemäß der Unternehmensphilosophie ‚The Productivity Advantage‘ hat sich die IBS AG zur Aufgabe gemacht, CAQ-, LIMS- und MES-Lösungen zu entwickeln und zu implementieren, die dazu beitragen, Geschäftsprozesse des Kunden zu optimieren und die Produktivität von Unternehmen zu steigern. Die IBS AG gehört zum Siemens-Konzern.
www.ibs-ag.de
Miba AG
Die Miba AG ist ein führender strategischer Partner der internationalen Motoren- und Fahrzeugindustrie. Das bereits 1927 gegründete Unternehmen beschäftigt an über 20 Standorten weltweit mehr als 4.300 Mitarbeiter. Die Miba Produkte – Sinterformteile, Gleitlager, Reibbeläge, Leistungselektronik- Komponenten und Beschichtungen – sind in Fahrzeugen, Zügen, Schiffen, Flugzeugen und Kraftwerken zu fi nden.
www.miba.com