„Das Team bestimmt den Erfolg der Transformationsreise.”
Experte: Moritz Heide, Vice President, RITTAL Digital Operations | 14.09.2023 | Teilen auf in
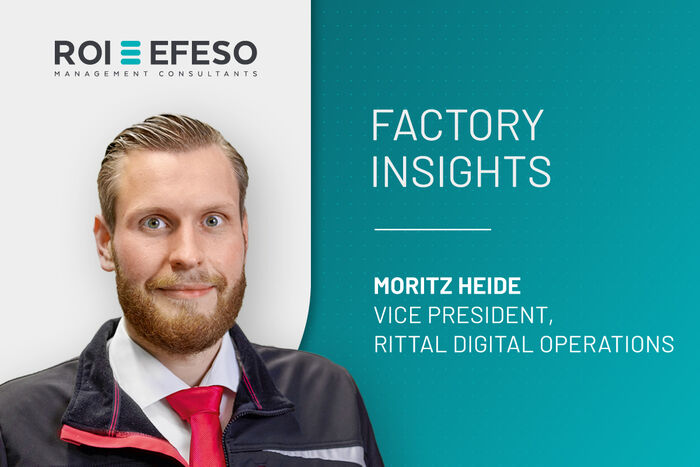
Herr Heide, wie wird aus einem Werk eine „Lights-out Factory“?
Moritz Heide: Der Weg dorthin lässt sich in vier Abschnitte unterteilen: Transparenz, Kollaboration, Autonomie und schließlich eine vorausschauende Selbststeuerung. Smart Factories befinden sich heute in der Regel in den ersten beiden Abschnitten, wobei sie je nach Fertigungskontext unterschiedliche Etappenziele umsetzen.
Unser Impuls ist, in jedem Fall zuerst Transparenz herzustellen: wie laufen die Fertigungsprozesse ganz konkret ab? Wie valide sind die erfassten Daten? Eignen sie sich für Folgeanalysen, z.B. wenn ein digitaler Produkt- oder Prozess-Zwilling entstehen soll? In unserem Werk sind wir mit genau diesem Zielbild einer transparenten Fabrik gestartet und haben zuerst grundlegende Themen geklärt: stimmt die Stückzahl? Wird der Maschinenzustand richtig interpretiert? Welche manuellen Abgleiche müssen mit dem Shopfloor vorgenommen werden?
Es lohnt sich, in die Klärung solcher Fragen die nötige Zeit zu investieren. Denn eine entsprechend valide Datenbasis bildet das Fundament für den Aufbau aller weiteren Digitalisierungs- und Automatisierungsmaßnahmen. Dazu zählt ein gutes Dashboarding – die vielleicht wichtigste Schnittstelle zwischen den Handgriffen in der Linie und der Datenkomplexität in der IT-Infrastruktur. Das Dashboard sollte den Mitarbeitern einen intuitiven Einstieg in die Datenwelt eröffnen – und zwar systemübergreifend! Nur wenn der Zugriff auf alle „Datentöpfe“ und alle Systeme in der Fabrik möglich ist, führt das zu neuen, wertvollen Erkenntnissen.
Womit wir auch schon im Bereich der Kollaboration angelangt sind …
Moritz Heide: Richtig – in der kollaborativen Fabrik geben uns die IT-/OT-Systeme Rückmeldungen, die wir aber in der Regel noch manuell auswerten und daraus Handlungsentscheidungen selbst ableiten. In der Verantwortung der Technologie liegt es etwa, Fehler und Anomalien in den Fertigungsabläufen zu erkennen und Entscheidern wie dem Fertigungsleiter entsprechende Maßnahmen vorzuschlagen. Hier sollte man übrigens auf die Feinabstimmung im Informationsaustausch achten: es geht ja nicht darum, z.B. nur Aufträge neu zu priorisieren. Sondern darum, das IT-/OT-System ständig mit neuen Daten zu versorgen, es zu befähigen, dazuzulernen. Nur so kann es Vorschläge machen, die schon bei einzelnen Arbeitsschritten zu einem Maximum an Effizienz führen.
Sobald solche Regelschleifen bereichsübergreifend vollautomatisch und autonom ablaufen, befinden wir uns in einer sich selbst optimierenden Fabrik. Wir kennen die Abweichung und versuchen, diese Situation zu adaptieren, den Fertigungsprozess zu adaptieren, die Umplanung anzustoßen, die logistische Versorgung anders anzustoßen, eine Maschine entsprechend anders anzusteuern.
Wird dies mit Predictive Analytics ergänzt, eröffnen sich weitere Optionen. Etwa bei der Koppelung der Schichtplanung mit Wetterdaten oder beim Thema Energieverbrauch, wenn die Fabrik im wahrsten Sinne des Wortes Maschinen, Anlagen und Lichter passend zur Auftragslage, der eigenen Energieversorgung und zugekauften Ressourcen vom Energiemarkt steuert. Genau dieses vorausschauende Handeln macht das Werk dann zur Lights-Out Factory.
Am RITTAL-Standort Haiger fertigen Sie Schaltschränke für die Industrie. Auf welchem der genannten Wegabschnitte ordnen Sie Ihr Werk ein?
Moritz Heide: In Haiger bewegen wir uns zwischen Kollaboration und Autonomie. Man darf sich das aber nicht als linearen Prozess vorstellen – es gibt Fertigungssegmente, in denen man bei Veränderungen immer mal wieder auf die ersten beiden Phasen zurückgeht, bei anderen blicken wir schon in Richtung der vierten Phase. Allerdings profieren wir auch von der Greenfield-Erstellung des Werkes: wir konnten eine neue Systemarchitektur aufbauen und viele neue Standards setzen, etwa bei der Maschinen- und Anlagensteuerung. Für Bestandsfabriken ist es hingegen immer wesentlich anspruchsvoller, erst einmal die transparente Fabrik als notwendige Grundlage zu verwirklichen.
"Wer IT-/OT-Systeme zum Lernen befähigt, kann ein Maximum an Effizienz erzielen."
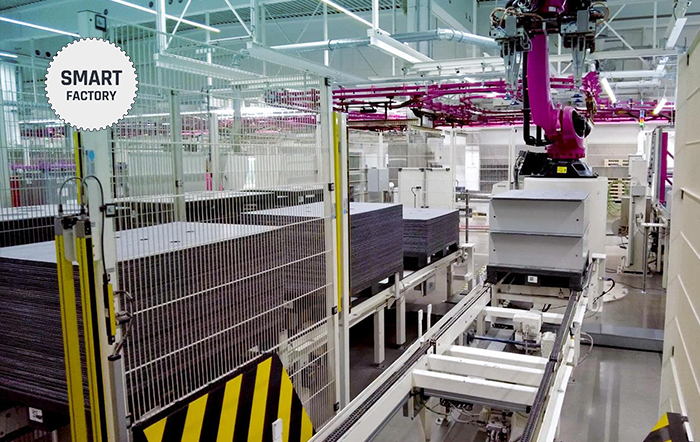
Das RITTAL-Werk in Haiger ist Preisträger des INDUSTRIE 4.0 AWARD.
Hier erfahren Sie mehr über die Lösung im Videobeitrag.
Welche Erfahrungswerte konnten Sie bislang sammeln, die auch für andere Fertigungsunternehmen wertvoll sein könnten?
Moritz Heide: Das allerwichtigste Thema ist das Team, mit dem Sie sich im Unternehmen auf die Transformationsreise begeben. Dieses Team macht den Erfolg aus. Da muss man ehrlich zu sich sein – sind es Silicon Valley Data Scientists, die sich am wohlsten fühlen, wenn sie abgeschottet programmieren? Oder sind es eher pragmatische Maschinenbau-Ingenieure oder Elektrotechniker? In unserem Markt sehen wir einen sehr starken Personalbedarf im Bereich zwischen Elektrotechnik und klassischer IT. Wir brauchen eine Kombination aus beiden Rollen, um zur transparenten Fabrik zu gelangen. Denn es geht ja zuerst darum, die Daten aus der Sensorik, aus der Anlagentechnik – also eigentlich aus der Elektro- und Automatisierungstechnik – in eine geeignete IT-Systemarchitektur zu integrieren. Mit all den Schnittstellen und Datenmodellen, die im Hintergrund notwendig sind.
Wir profitieren sehr davon, dass wir beim Aufbau des Werkes ein entsprechendes Team aufstellten: Elektrotechniker, SPS-Programmierer, IT-Experten für Datenbanken und die Systeminfrastruktur, die vom ersten Tag an zusammengearbeitet haben. Daraus entwickelte sich eine Art Bindeglied in der Organisation. Und das erwies sich wiederum als entscheidender Punkt, um valide Daten zu erhalten und die Prozesse am Ende ins Laufen zu bringen.
Wenn es darum geht, andere Fertigungsunternehmen auf ihrem Weg Richtung Smart Factory zu unterstützen, hat sich die Verbindung der Kompetenzen verschiedener Domänen aus unserer Unternehmensgruppe als hilfreich erwiesen. Eplan und RITTAL treiben den Aufbau des Digitalen Zwillings von Maschinen und Anlagen voran und machen die Daten im Betrieb nutzbar. Cideon steigert die Datendurchgängigkeit rund um den digitalen Produktzwilling mit Expertise in CAD/CAM, PDM/PLM und Produktkonfiguration. Das ONCITE Digital Production System (DPS) der German Edge Cloud macht dann die Daten der Fertigungsprozesse transparent und damit optimierbar.
Nun sind aber gerade in Brownfield-Werken diese Daten häufig in unterschiedlichen Systemen und voneinander getrennten Quellen über die Organisation hinweg verteilt …
Moritz Heide: Daher plädiere ich absolut dafür, solche „Silo-Strukturen“ aufzubrechen, sowohl im Brownfield- als auch im Greenfield-Szenario. Das war eine weitere, wichtige Erfahrung für uns: man muss Datensilos sehr früh auflösen bzw. darf es erst gar nicht zulassen, dass sie entstehen. Das erreicht man mit einer zentralen Plattform. Zudem sollte man von Anfang an sicherstellen, dass man ständig alle für den Fertigungsprozess wichtigen Daten auf dieser Plattform einspeist. Also zum Beispiel aus den Steuerungen, aus einem Leitsystem, aber auch aus den Leitsystemen der fahrerlosen Transportfahrzeuge.
So wird klar, welche Daten überhaupt wichtig sind. Das Vorgehen befähigt aber vor allem das Team dazu, Erkenntnisse zu gewinnen: welche Abhängigkeiten gibt es zum Beispiel zwischen Intralogistik und Produktion? Wer wartet da auf wen? Und natürlich bei den klassischen Shopfloor-Themen: wer ist eigentlich verantwortlich für meinen Effizienzverlust? Diese Analyse in Minuten statt in Stunden oder Tagen zu erhalten, ohne bei jeder Problemstellung von einer Lösung aus der IT-Abteilung abhängig zu sein, ist ein enormer Vorteil.
Wie sind Sie beim Aufbau Ihrer IT-/OT-Infrastruktur vorgegangen? Welche Ansatzpunkte haben sich im Sinne der „transparenten Fabrik“ als besonders hilfreich erwiesen?
Moritz Heide: Erstens, die Digitalisierungsstrategie für das Werk modular aufzubauen. Das kann sich aber auf alle genannten Phasen beziehen. Wir haben bei der Zusammenstellung unseres Modulkataloges zum Beispiel festgestellt, dass die Module „Dashboarding“, „Worker Guidance“ und „Energiemonitoring“ essenziell sind. Über die Auseinandersetzung mit diesem Modulkatalog erreicht man also im Team ein gemeinsames Verständnis davon, was die „transparente Fabrik“ überhaupt ist.
Zweitens sind Low-Code-/No-Code fähige IT-Systeme wichtig. Eine entsprechende Plattform befähigt etwa Excel-Profis, schnell Dashboards und kleine Analysen zusammenzubauen. Im Idealfall werden die dann gleich als Standardbaustein in die Systemarchitektur übertragen – erneut ein Prozess, der in kurzer Zeit abgeschlossen sein kann, ohne das Know-how von IT-Profis dafür zu beanspruchen.
Oder digitale Assistenten übernehmen diese Aufgaben …
Moritz Heide: Die Erwartung ‚die KI oder ein Bot lösen mein Problem‘ birgt Risiken. Wer so startet, kann schnell sehr viel Geld für eine kaum signifikante Prozessverbesserung ausgeben. Kommerziell verwendbare LLMs oder Chat-GPT-Ableger aufwändig und kostenintensiv mit EU-Daten zu trainieren, kann ein Schnellschuss sein.
Wir finden für viele Probleme regelbasierte Lösungen, die keine KI benötigen – sondern einfach eine smarte, automatische Regelungstechnik. Allerdings darf sich diese eben nicht wie in der Vergangenheit nur auf eine Einzelmaschine oder eine Produktionslinie beziehen. Sie muss die gesamte Fabrik abbilden und, wie beim Thema Energie, Daten aus dem äußeren Umfeld aufnehmen und diese in den Kontext der aktuellen Fertigungssituation setzen.
"Viele Probleme benötigen keine KI zur Lösung – sondern eine smarte, automatische Regelungstechnik."
Über Moritz Heide
Moritz Heide ist Vice President RITTAL Digital Operations bei der RITTAL GmbH & Co. KG. Zuvor war er in unterschiedlichen Führungspositionen im Unternehmen tätig, u.a. als Head of Digital Processes, OT Maintenance and Work Preparation beim Greenfield-Aufbau des Industrie 4.0-Werkes am Standort Haiger.
![]() |
Thank you for Signing Up |

