DIGITAL TWIN
Kunden profitieren von Prozessübergreifender Qualität
Interview mit Daniel Schnitzler, Head of Supply Chain Management, Bilsing Automation GmbH
1 Vollumfängliche Simulation der Saugfertigkeit
2 Vorteile in der Fertigungslinie
3 Standardsoftware genügt nicht
Herr Schnitzler, Ihr Unternehmen bildet den Vulkanisationsprozess der Saugerfertigung virtuell ab – was muss man sich darunter vorstellen?
Wir fertigen Sauger, insbesondere für den Bereich Rohbau- und Presswerksautomation. Problematisch bei der Vulkanisation ist, dass man Fehler im Prozess nicht sofort am Produkt Bilsing Automation GmbH erkennen kann, sondern dass sich diese Fehler erst nach einigen Monaten beim Kunden feststellen lassen, etwa durch einen erhöhten Verschleiß der Sauger. Der nachträgliche Austausch kostet ein Vielfaches, als wenn der Fehler direkt im Prozess behoben wird. Der digitale Twin bildet hierbei nicht nur die Vulkanisation an sich, sondern auch vor- und nachgelagerte Stufen als Modell ab. Somit besitzen wir eine vollumfängliche Simulation unserer Saugerfertigung.
Mit digitalen Modellen der Fertigungslinie können Sie verschiedene Produkfertigung virtuell ab ablaufen lassen. Welche Vorteile ergeben sich daraus für Ihre Kunden?
Der digitale Twin ermöglicht es uns unter anderem, qualitätsrelevante Aspekte zu analysieren. Insbesondere schauen wir uns den Einfluss von vor- oder nachgelagerten Stufen der Vulkanisation an. Die Lagerung der Sauger bzw. des Rohmaterials hat zum Beispiel einen erheblichen Einfluss auf die Haltbarkeit der Produkte, da sie bei falscher Lagerung schneller hart und damit spröde werden. Der Twin hat hierbei zu einer deutlichen Verbesserung der Prozesse der Lagerung des „work in progress“- Materials geführt, sodass wir die Haltbarkeit der Sauger verbessern konnten. Somit stellen wir eine prozessübergreifende Qualität sicher – wovon letztendlich unsere Kunden profitieren, da sie Produkte mit einer erhöhten Haltbarkeit gegenüber vergleichbaren Wettbewerbsprodukten erhalten.
Welche besonderen 4 Herausforderungen gibt es bei Pressen- und Robotbewegungen in der Automobilindustrie und wie hilft Ihr Twin, diese zu bewältigen?
Der Twin hilft uns, eine holistische Sicht auf den Gesamtprozess zu erhalten. Bei anderen Modellen ist die Reduktion auf den Kernprozess oftmals zu scharf, sodass wichtige Aspekte nicht abgebildet werden.
Als Beispiel möchte ich die oftmals universellen Simulationen aus gängigen Softwaresystemen anführen. Sicherlich lässt sich hiermit einfach feststellen, welche Übergaben der einzelnen Prozessschritte nicht optimal verlaufen und wo es so zu Wartezeiten kommt, zum Beispiel bei einer Warteschlange vor dem Werkzeuglager, was zu ungeplanten Stillständen der Maschinen führt. Die Auswirkung einer falschen Temperatur des Härteofens, da falsche Papiere vorlagen, lässt sich aber nicht simulativ im Rahmen von Standardsoftware betrachten.
Wie entwickeln Sie Ihren Digital Twin zukünftig weiter?
Zurzeit führen wir Digital Twins im Bereich der CNC-Fertigung ein. Hintergrund ist, dass wir angefangen haben, einen Teil der Vorarbeiten für den Bilsing-Werkzeugbau in Tschechien vorzufertigen, der auf die Herstellung von Hitzeschutzblechen spezialisiert ist. Die Prozesse für das Fräsen eines Werkzeugs sind jedoch andere als für Teile, die in der Automation benötigt werden (Toleranzen etc.). Ziel ist es, vor- und nachgelagerte Stufen zu glätten, um so die Produktivität der Engpassmaschinen zu erhöhen.
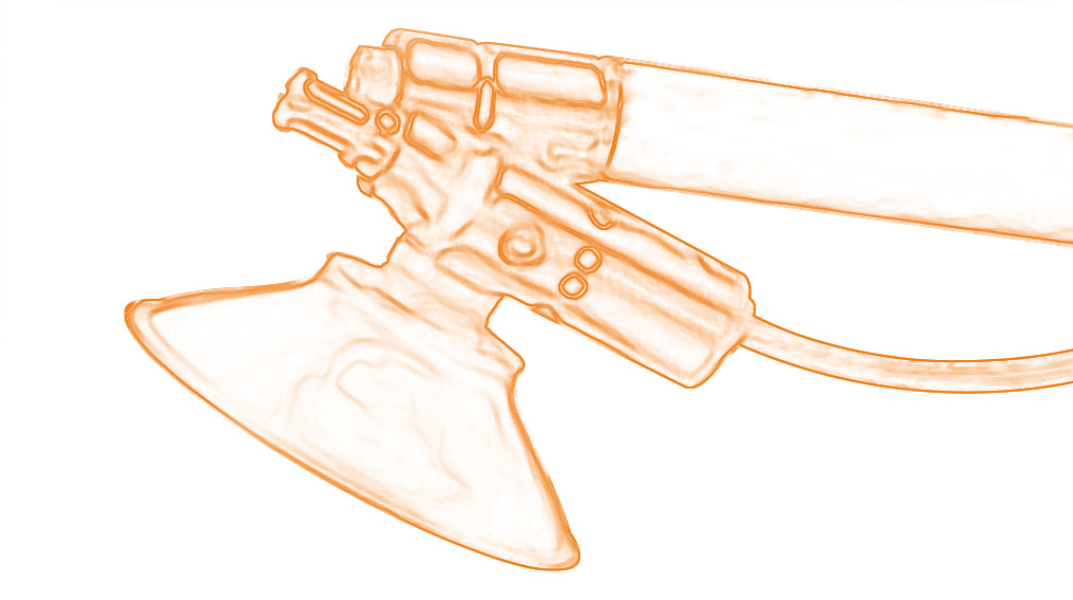