THEMEN & NEWS
Beiträge und Interviews zu aktuellen Fach-, Technologie- und Branchenherausforderungen, Informationen zu unseren Beratungsangeboten, Seminaren und Events sowie Unternehmensthemen:
Hier erfahren Sie, was EFESO bewegt.
INDUSTRIE-4.0-PRÄMISSEN FÜR DIE SMART FACTORY
Wie Motorhauben, Türen, Heckklappen und Fahrzeugdächer mit zukunftsweisenden Industrie-4.0-Technologien gefertigt werden, ist seit dem Sommer 2021 am Stadtrand von Halle (Saale) in Aktion erlebbar. In etwa zwei Jahren entstand dort auf der grünen Wiese ein Presswerk zur Karosserieteilefertigung. Als Joint Venture von Porsche und der Schuler AG bündelt das „Smart Press Shop“-Werk die Kompetenzen eines Autoherstellers und Pressenbauers, um gemeinsam neue Produkte zu entwickeln und zu realisieren. Dabei agiert Smart Press Shop wie ein neutraler Lieferant am Markt, alle Anlagenparameter sind kompatibel zu Daimler, BMW und dem VW Konzern.
Ein Highlight des Werkes ist der vollständig autonome Einrichtungsprozess für die Bereitstellung der Presswerkzeuge, der eine wettbewerbsfähige Produktion von Kleinserien ermöglicht. Geschlossene Kreisläufe und der Betrieb mit erneuerbaren Energien minimieren zudem die CO2-Emissionen bei der Herstellung der Außenhautteile aus Aluminium oder Stahl. Die Anzahl von Anbietern entsprechender Komponenten geht seit einigen Jahren zurück, während zugleich die Anforderungen an die Produktqualität steigen. Vor diesem Hintergrund entstand die Idee, das smarte und voll vernetzte Presswerk auf Basis von Industrie-4.0-Technologien zu realisieren.
Automatisierung steigert Effizienz
Das Werk ist mit einer zukunftsweisenden, vertikal und horizontal integrierten IT-Infrastruktur ausgestattet, um einen höchstmöglichen Grad an Konnektivität auf allen Ebenen zwischen Maschinen und Arbeitern herzustellen. Doch die Zielsetzung des Projektes umfasst mit sieben Industrie-4.0-Prämissen noch viel mehr als das:
- Vertikal und horizontal integrierte IT-Infrastruktur: Von Anfang an sollen Datensilos vermieden und der Datenfluss trotz höchster IT-Sicherheit gewährleistet werden. Alle Maschinen und Anlagen sind über PLCs verbunden und in der Cloud vernetzt.
- Automatisierte, selbstoptimierende Prozesse: Dabei geht es nicht nur um rein physische Prozesse, sondern auch um automatisierte Auftrags- und Rückmeldungsvorgänge, (selbst-)optimierende Richthilfen und kamerabasierte Prozessüberwachung.
- 100-prozentige papierlose Prozesse in Produktion und Verwaltung
- Digitale Dokumentation: Dazu zählt u.a. das Thema Werkerführung. Zwecks Transparenz und Prozessoptimierung werden auch manuelle Prozesse digital zurückgemeldet.
- Echtzeitdaten überall und jederzeit verfügbar: Alle von den Anlagen erzeugten Informationen sind jederzeit und überall einseh- und analysierbar.
- Ressourcenschonende ProduktionR durch geschlossene Kreisläufe (Close Group Material), z.B. sortenreines Recycling von Aluminium im Closed Loop.
- Digitaler Produkt- und Prozesszwilling: Alle erzeugten Maschinen-, Bediener-, Produkt- und Prozessdaten werden auf Produktebene gespeichert und sind für den Kunden rückverfolgbar. Dies wird zudem für Big Data Analytics genutzt.
Bereits in der Anlaufphase der Produktion zeigte sich, dass dieser Ansatz in der Praxis greift und signifikante Ergebnisse bringt. So erledigt das Fertigungsteam aufgrund eines vollautonomen Rüstvorgangs bei der Presswerkzeugbereitstellung das Rüsten der Pressenlinie mindestens 50–70 % schneller als jedes andere Presswerk. Dies ermöglicht eine wettbewerbsfähige Produktion von Kleinserien.
Eine zentrale Rolle spielen hierbei zwei Schwerlastkräne mit jeweils 65 Tonnen. Diese können parallel und vollautomatisch die Anlagen der Presslinie je nach eingehenden Produktionsaufträgen mit den richtigen Werkzeugen bestücken. Dabei ist nicht nur das Werkzeuglager vollautomatisch verwaltet, auch die Werkzeugablage erfolgt automatisch durch optische Sicherheitstechnik: Das tonnenschwere Presswerkzeug wird von einem autonomen Werkzeugkran an- und abtransportiert, automatisiert eingespannt und Medien werden automatisch gedockt. Auf diese Weise beträgt die Gesamtrüstzeit für das Einrichten der Maschine inkl. Beladung und Distanzierung nur drei Minuten. Die Zeit für die Produktionsvorbereitung, also für den Zu- und Abtransport von sechs Werkzeugen an die Linie, lässt sich im Vergleich zu einem herkömmlichen Presswerk halbieren oder sogar dritteln.
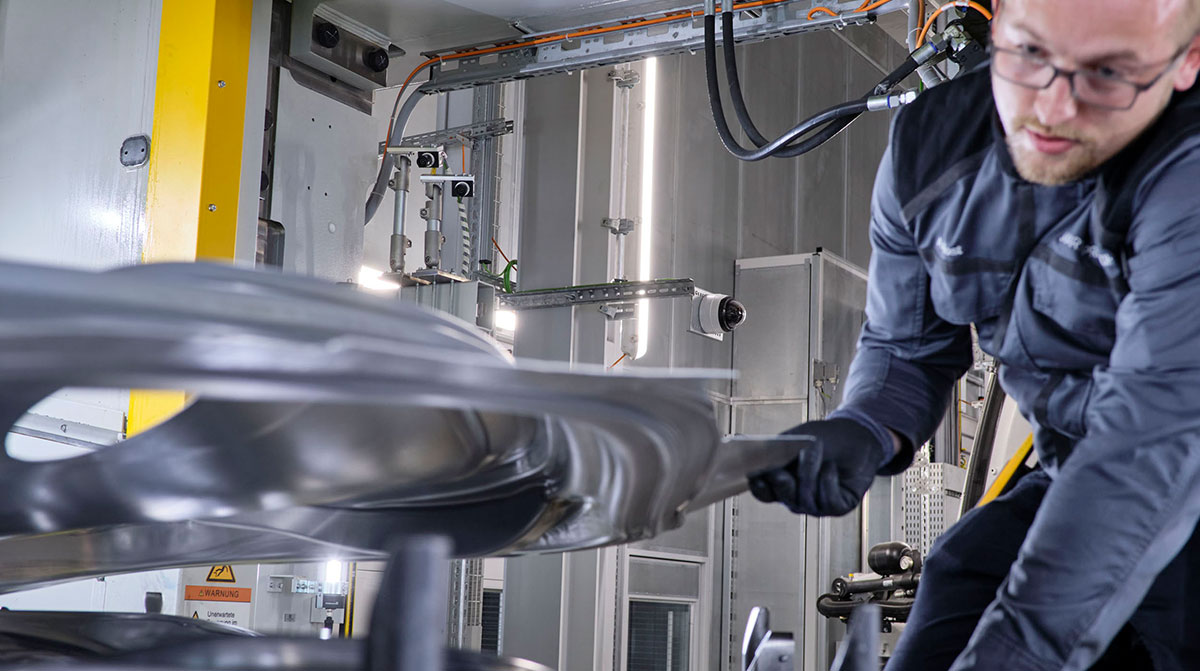
Erhöhte Produktivität bei gesenktem Ressourcenverbrauch
Als First Mover musste das Team des Smart-Press-Shop-Projektes klassische Herausforderungen der Industrie 4.0 bewältigen, etwa fehlende Standards in Bereichen wie der IT-Sicherheit oder der digitalen Dokumentation mit eigenen Lösungen ausgleichen. Dabei konnten bereits große Nutzenvorteile erzielt werden: Alle Arbeitskräfte ebenso wie sämtliche Maschinen und Anlagen sind über die Cloud vernetzt und sämtliche Prozesse liefern Echtzeitdaten, die jederzeit und überall einsehbar sind. So lässt sich jedes produzierte Teil durchgängig rückverfolgen. Positive Ergebnisse stellen sich allerdings nicht „automatisch“ nur anhand der Verfügbarkeit neuer technologischer Tools ein. Die Akzeptanz dieser Instrumente seitens der Mitarbeiter sicherzustellen erwies sich als entscheidender Bestandteil und Erfolgsfaktor des Projektes.
Die Leistungskennzahlen der Smart Factory sprechen für sich: Mit einer Beschleunigung der Bearbeitungsprozesse sind die Vorlaufzeiten um ein Viertel reduzierbar. Allein die Rüstzeiten sind durch vollautonomes Rüsten um etwa 60 % verkürzt. Somit sind auch Losgrößen möglich, die 60 % kleiner sein können, sowie 30 bis 60 % geringere Lagerbestände.
Aber natürlich ist auch eine hochdigitalisierte Smart Factory nie komplett ausgereift. In Zukunft wird die Produktionsplanung in hohem Maße durch KI unterstützt werden. Aktuell erfolgt die Planung vorwiegend manuell, um das Personal auf die Prozesse zu schulen. Darüber hinaus sollen die Mitarbeiter in den nächsten Jahren verstärkt mobile Geräte wie Smartwatches nutzen.
Eine andere Weiterentwicklung betrifft das Qualitätsmanagement. Dort ist eine optische Qualitätskontrolle geplant, die kamerabasiert und mit KI-Unterstützung eine vollständig automatisierte Fehlererkennung und eine bauteilbezogene Fehleranalyse von Fertigteilen ermöglicht. Das macht Abweichungen zum vorgegebenen Perfektionsgrad schnell und zuverlässig sichtbar und erlaubt einen geschlossenen Qualitätsregelkreis für die Smart Factory.
Einsatzfeld: Automobilindustrie
Herausforderung
Neubau einer Smart Factory mit modernster IT-Infrastruktur; hohe Vernetzung der Maschinen und Arbeiter auf allen Ebenen, 100-prozentige papierlose Produktion sowie hohe Produktivität bei geringem Ressourcenverbrauch als wichtigste Zielsetzungen für den Betrieb des Werkes.
Lösung
Umsetzung von sieben Industrie-4.0-Prämissen mit einer vertikal und horizontal integrierten IT-Infrastruktur als zentralem Element; alle Maschinen und Anlagen über Programmable Logic Controller (PLC) verbunden; Verarbeitung von zeitsensitiven Informationen und Befehlen per speicherprogrammierbarer Steuerung (SPS) und Supervisory Control and Data Acquisition (SCADA); alle Systeme ab MES-Ebene in der Cloud gehostet.