THEMEN & NEWS
Beiträge und Interviews zu aktuellen Fach-, Technologie- und Branchenherausforderungen, Informationen zu unseren Beratungsangeboten, Seminaren und Events sowie Unternehmensthemen:
Hier erfahren Sie, was EFESO bewegt.
Warnsignale im Management-Cockpit
Wie E-Mobility die Kräfteverhältnisse in der Automobilindustrie verändert
Von Michael Jung, Vorstand, ROI Management Consulting AG
Bei den bisherigen automobilen Evolutionsschritten hat sich ein kleines Detail über Jahrzehnte hinweg nicht verändert: das gefährlich rote Glimmen der Warnleuchte im Cockpit, die einen Motordefekt signalisiert. Als ähnlich unheilvoll, aber von vielen Kfz-Laien sträflich unterschätzt, gilt die Öl-Kontrollleuchte. Wer ihr Signal missachtet, setzt eine fatale Kettenreaktion in Gang: Kein Öldruck bedeutet keine Kolbenschmierung, was zum Kolbenfresser führt – womit man wiederum beim kapitalen Motorschaden wäre.
Dieses Schreckensszenario wird definitiv der Vergangenheit angehören, falls sich die rein elektrische Antriebsvariante tatsächlich mittel- oder langfristig beim Fahrzeugbau behaupten sollte. Denn der Elektroantrieb ersetzt die hochkomplexen Bestandteile des „Verbrenners“: Neben Motorgehäuse und Zylinderkopf sind zahlreiche Systemkomponenten – etwa für Luftzufuhr, Kraftstoffversorgung, Zündung oder Schmierung – nicht länger notwendig. An ihre Stelle tritt der Elektromotor und -antrieb, der mit neuen Komponenten wie dem Batterie- und Ladesystem, der Leistungselektronik oder speziellen Klima-/Heizungssystemen (s. Grafik S. 5) auf rund 210 Bestandteile kommt – eine enorme Komplexitätsreduktion im Vergleich zum durchschnittlichen Verbrennungsmotor mit rund 1.400 Teilen.
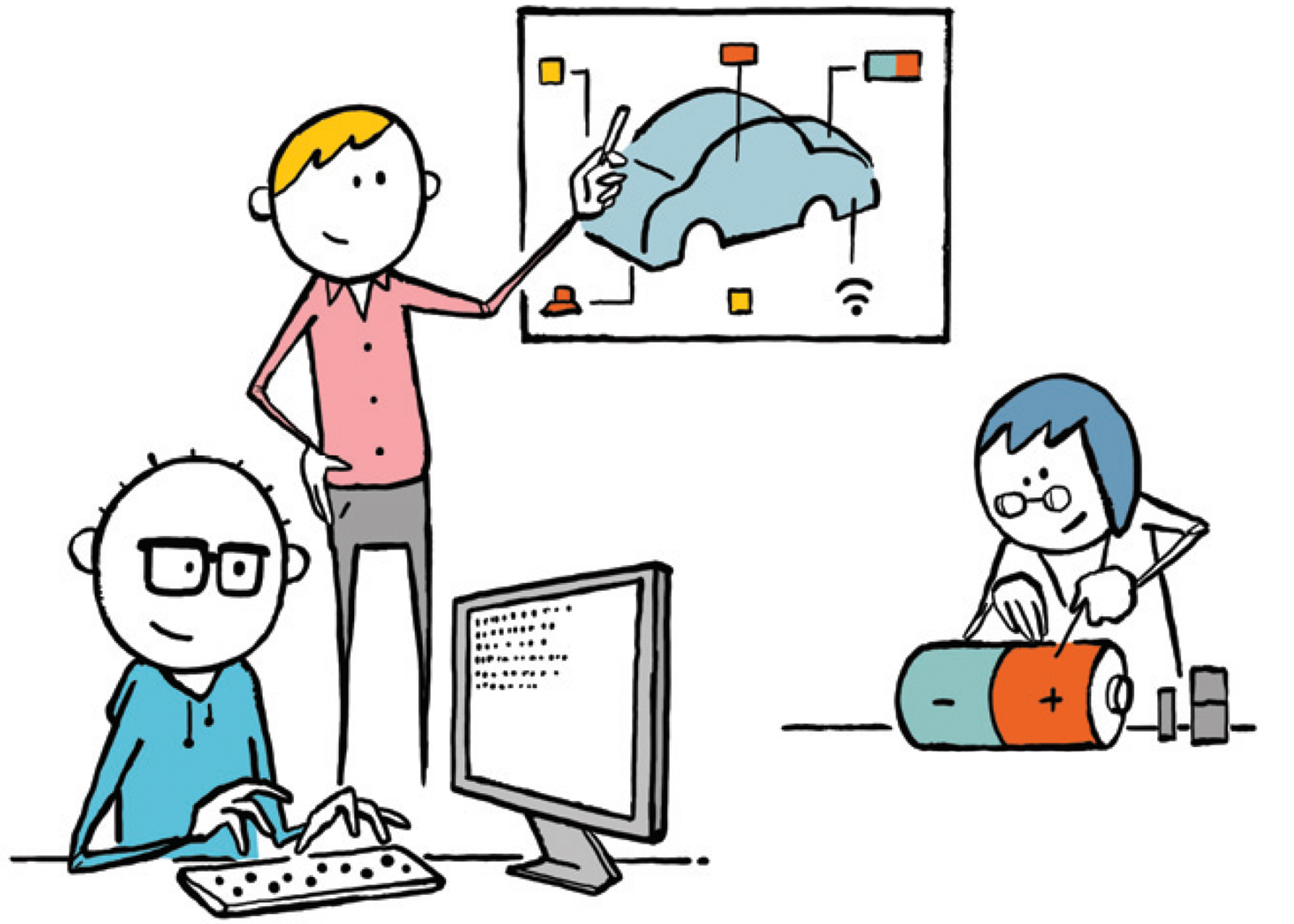
Für die Automobilbranche, die bislang technologische Innovationen und Kundenwünsche im relativ klaren Rahmen der Entwicklungszyklen ihrer Modellreihen adaptieren konnte, bedeutet diese Entwicklung eine entscheidende Zäsur. Denn der Lebenszyklus eines Fahrzeugs – von der Entwicklung und Produktion über die Nutzung und schließlich Entsorgung – verändert sich komplett (s. Grafik S. 7) und somit die entsprechenden, über gut ein Jahrhundert gewachsenen Wertschöpfungsstrukturen und Kräfteverhältnisse in der Branche. Besonders gravierende Veränderungen stehen in drei Dimensionen an: der Zuliefererstruktur, der Hersteller-/Zuliefererbeziehung sowie beim Aufbau neuer, IT- bzw. softwaregetriebener Kompetenzen in F&E.
Zulieferer: Spezialisten unter Druck
Viele Automobilzulieferer standen in den letzten Jahren hinsichtlich elektromobiler Innovationen kaum vor großen Herausforderungen – die Nachfrage nach reinen E-Fahrzeugen am Markt stagnierte und damit auch die Bereitschaft ihrer Kunden, ihre Modellpolitik zugunsten dieser Antriebsvariante wesentlich zu verändern. Der Fokus der Innovation lag stattdessen auf Themen wie dem „Downsizing“, also Effizienzsteigerungen beim klassischen Verbrennungsmotor, wodurch einige Motorenhersteller und motornahe Zulieferer sogar ein Umsatzwachstum verbuchen konnten. Doch in genau dieser Fokussierung, das vorhandene Produkt immer besser zu machen, liegt mittel- und langfristig ein erhebliches Risiko. Denn sollte es tatsächlich zu einem signifikanten Anstieg des Anteils rein elektrischer Fahrzeuge kommen, wie ihn Branchenexperten für den Zeitraum 2020 bis 2040 vorhersagen, geraten vor allem spezialisierte Zulieferer extrem unter Druck: Finden sie keine Alternativen zu Produkten wie Nockenwellen, Turboladern oder Einspritzpumpen, wird ihr Geschäft erheblich schrumpfen oder sogar ganz verschwinden. Allerdings variieren die Prognosen, auf welche konkreten Entwicklungen die deutsche Zulieferindustrie sich nun tatsächlich einstellen sollte, seit Jahren zwischen zwei Extremen: Während das eine Lager Tausende von Arbeitsplätzen in Gefahr sieht und den Vorsprung asiatischer Wettbewerber bei Batterietechnologien beklagt, beschwören andere Marktstudien die Chancen neu entstehender Arbeitsplätze in der Fertigung der neuen E-Komponenten.
Sicher ist: Die Beschäftigungseffekte in der Automobilproduktion werden von einer Komplexitätsreduktion geprägt sein. Einige der neuen Komponenten könnten dabei ein starkes Marktvolumen generieren, etwa die „elektrische Maschine“ als Kernstück des elektrifizierten Antriebsstrangs. Allein für dieses Bauteil prognostiziert die „Strukturstudie BWe mobil 2015“ einen Zuwachs des Marktvolumens auf fast 21 Milliarden Euro bis 2025 bzw. gut 38 Milliarden Euro bis 2030 gegenüber dem Jahr 2013. Die wesentlichen Treiber könnten hier die zunehmende Hybridisierung sowie der steigende Anteil batterieelektrischer Fahrzeuge am globalen Absatz sein (vgl. Strukturstudie BWe mobil 2015, S. 55). Das Beispiel verdeutlicht zudem, dass ein Strukturwandel in der Zulieferindustrie nicht über Nacht, sondern in Phasen erfolgt. Für die besonders relevanten Wertschöpfungsinhalte der elektrischen Maschine sind auch bereits Fertigungs- und Montagekonzepte vorhanden – allerdings muss die Effizienz bei deren Umsetzung für eine kostengünstige Produktion noch verbessert werden.
„Die Beschäftigungseffekte in der Automobilproduktion werden von einer Komplexitätsreduktion geprägt sein.“
Michael Jung
E-Kooperationen: Verschiebung in der Wertschöpfungskette
Aus der Perspektive des Autokäufers mögen reine E-Modelle noch Exotenstatus haben – doch in der Automobilindustrie hat sich die Einstellung zum elektrischen Antriebsstrang bereits deutlich geändert, seit Batterien immer günstiger und leistungsstärker werden und vor allem Tesla zeigt, dass sich reine E-Autos eben doch massentauglich entwickeln, herstellen und verkaufen lassen. Die Elektrifizierung des Antriebsstrangs wird daher die heutigen Grenzen in der Wertschöpfungskette zwischen Automobilherstellern und Zulieferern deutlich verschieben. War die Beziehung zwischen OEM und Zulieferer beim Verbrennungsmotor eine klare „Einkäufer–Verkäufer“-Konstellation, können die Automobilhersteller nun zwei Strategien verfolgen: a) selbst die Entwicklungskompetenz für elektrische Antriebe aufbauen und eigene Produktionskapazitäten etablieren oder b) sämtliche Komponenten von Zulieferern zukaufen und sich auf die Systemintegration konzentrieren.
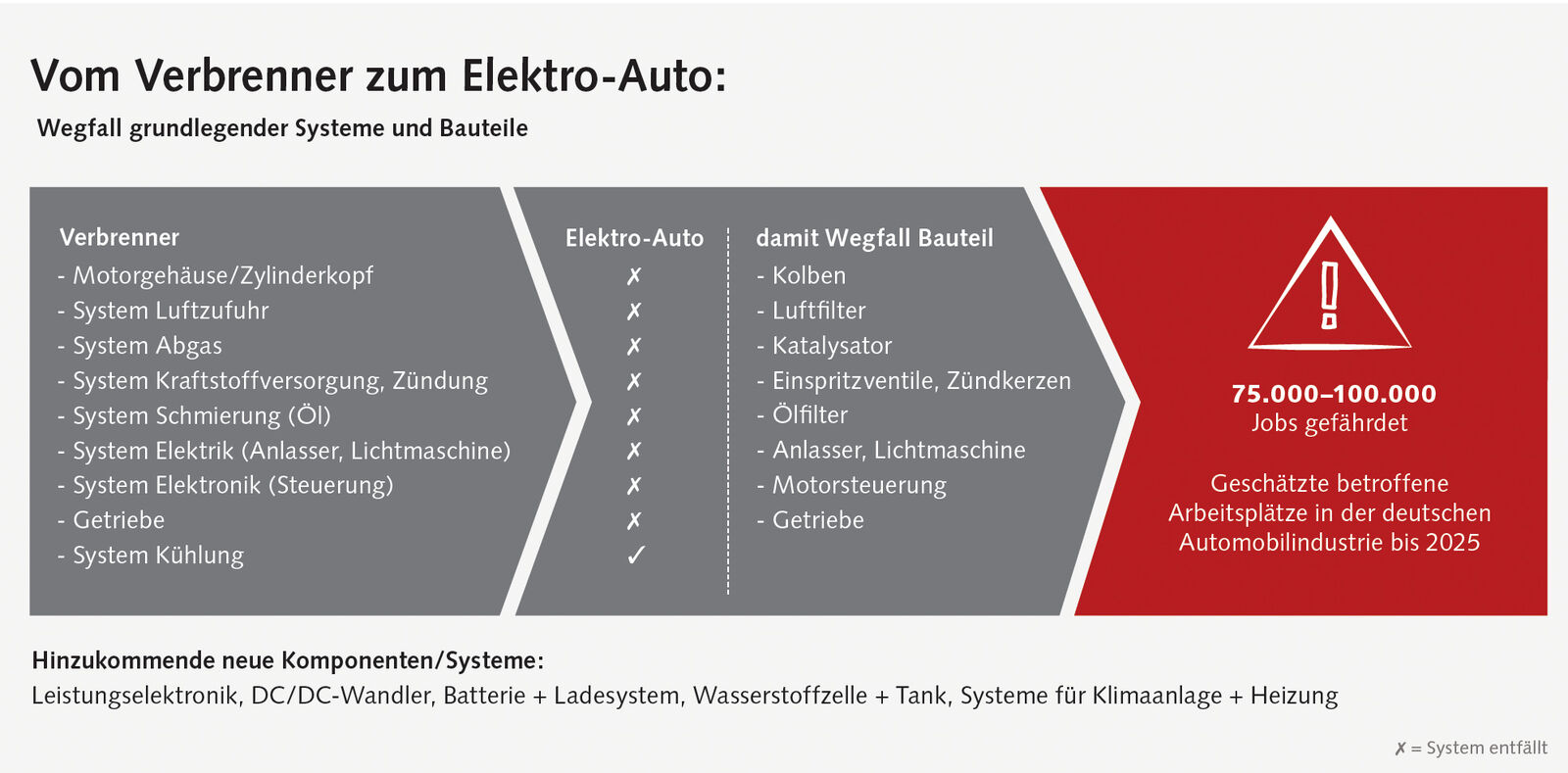
Software statt Selbstzündung: neue Kompetenzen in F&E
Die Vision des „iCar“ von Apple sollte man keinesfalls als nebensächliche Episode der Automobilgeschichte einstufen, in der die Fantasie mit dem IT-Konzern durchging oder als eine Phase von Größenwahn. Tatsächlich ist es keine Frage, ob ein Silicon-Valley-Riese wie Apple ein eigenes Fahrzeug produzieren kann – sondern zu welchem Zeitpunkt er dies tatsächlich tun möchte. Schließlich fertigen auch die etablierten OEMs wie VW bereits heute ihre Fahrzeugmodelle nach dem Baukastenprinzip: Ähnlich wie bei Handys und Computern bestellt man die Komponenten, setzt im eigenen Werk alles zusammen und kümmert sich dann um die Vermarktung – ein Geschäft, das sich mit rund 25 Prozent Eigenwertschöpfung betreiben lässt. Wird nun der Verbrennungsmotor durch Hybrid-Technologien ergänzt bzw. langfristig durch den elektrifizierten Antriebsstrang abgelöst, vereinfacht das zusätzlich den Einstieg neuer, branchenfremder Wettbewerber im Automobilbau.
Für die etablierten Automobilzulieferer hat das mehrere Implikationen. Sie können, etwa durch Entwicklungspartnerschaften, an diesem Kompetenzaufbau teilhaben und sich so enger an ihre bisherigen Kunden auf Herstellerseite binden. Auf lange Sicht könnten sich die Automobilhersteller jedoch auch am Beispiel General Motors orientieren und inhouse Kompetenzen für Batterien und E-Motoren selbst aufbauen, um mehr Unabhängigkeit zu erreichen. GM investiert bereits seit sieben Jahren erhebliche Summen in eine hauseigene Batterie- und Elektromotorfertigung: Als Resultat produziert das Unternehmen aktuell in Detroit je nach Nachfrage flexibel zwischen 58 und 158 Elektroautos am Tag, die teilweise bereits eine Reichweite von bis zu 500 Kilometern bieten.
Um sich nicht von der elektromobilen Strategie ihrer OEM-Kunden abhängig zu machen, sollten Zulieferer also in jedem Fall einen „Plan B“ verfolgen, d.h. Kooperationen mit Batterieherstellern sowie Unternehmen aus dem Maschinenund Anlagenbau aufbauen. Deren Ziel sollte nicht nur ein gegenseitiger Know-how-Transfer sein, sondern auch die Entwicklung gemeinsamer Produkte und Services rund um den elektrischen Antriebsstrang mit hohem Alleinstellungsmerkmal, um mit dieser „E-Kompetenz“ langfristig ein attraktiver Partner für OEMs zu sein.
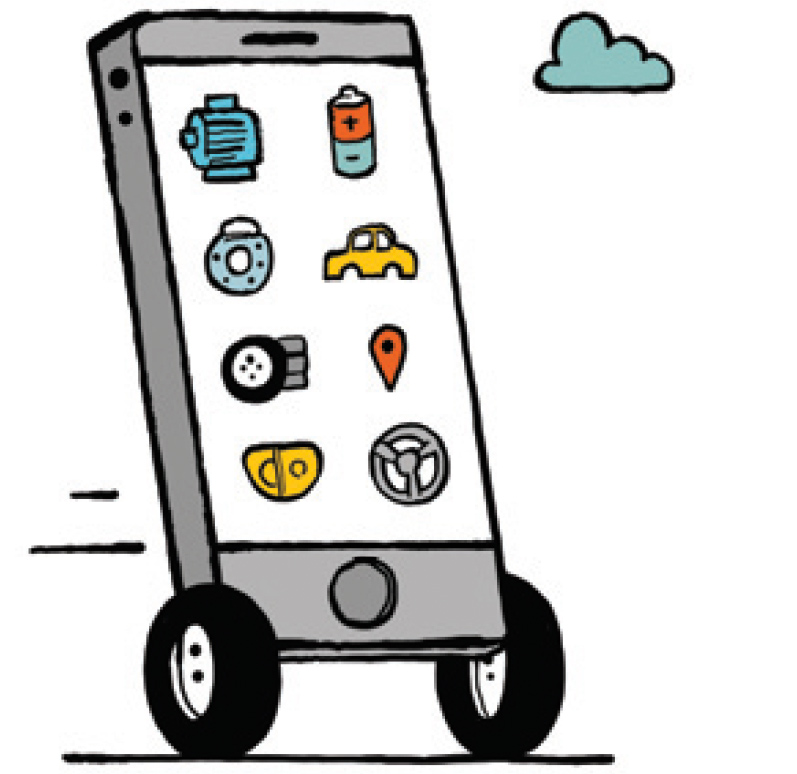
„Das reine Elektrofahrzeug ist eher mit einem Smartphone als einem konventionellen Auto vergleichbar.“
Michael Jung
Zudem konkurriert die Automobilindustrie bereits mit der IT-Branche um wertvolle Mitarbeiter, insbesondere IT- und Elektrotechnik-Spezialisten. Für die F&E-Abteilungen von OEMs und Zulieferern wird sich diese Situation in den nächsten Jahren weiter verschärfen. Denn Elektronik und Software wachsen immer stärker zusammen, etwa für das (teil-)autonome Fahren: Hierzu ist Sensorik aus dem Elektronikbereich notwendig, während die gewonnenen Daten per Software verarbeitet werden. Vor allem das reine Elektrofahrzeug ist daher – entwicklungstechnisch gesehen – eher mit einem Smartphone als einem konventionellen Auto vergleichbar: Das softwaregesteuerte Management der Energieverbräuche von Infotainment, Fahrassistenzsystemen, Heizung, Licht etc. wird in Koordination mit der Weiterentwicklung der Batterietechnologien zum entscheidenden Erfolgsfaktor für die Reichweite bzw. Leistungsfähigkeit und damit die Attraktivität des Fahrzeugs beim Endkunden. Entsprechend schnell muss die Automobilindustrie sich beim Recruitment als Wettbewerber der IT-Branche verstehen – und jetzt Hochschul- und Ausbildungsinitiativen starten bzw. fördern, die dem Fachkräftebedarf entsprechen. Wer diese Entwicklungen ignoriert, riskiert in jedem Fall den kapitalen Motorschaden für sein Geschäftsmodell.
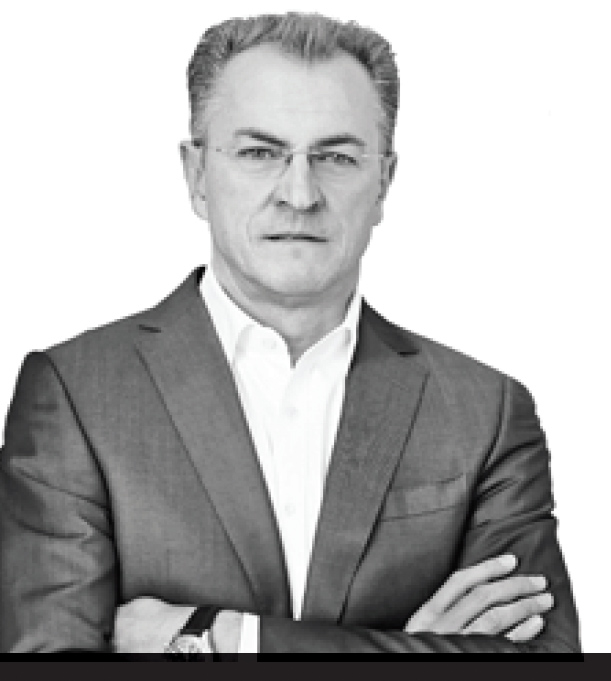