Schritt für Schritt zum virtuellen Prozesszwilling
Neue Chancen für die präzisere Analyse und Gestaltung von Wertschöpfungsnetzwerken
- Digital Twins in der Industrie
- Digital Twin für einen Prozess aufbauen: So wird´s gemacht
- Neue Optionen zur Bewertung, Steuerung und Qualifizierung von Lieferanten
Digitale Zwillinge, also virtuelle Modelle, die ihre physische Entsprechung möglichst umfassend und in Echtzeit abbilden, gehören zu den besonders beeindruckenden Beispielen für Industrie 4.0 und das Internet der Dinge. Die transformative Rolle dieses Ansatzes wird in den kommenden Jahren mit Sicherheit noch wesentlich deutlicher werden, wenn er sich auf breiter Front durchsetzt. Bis dahin ist es allerdings noch ein weiter Weg. Wirft man einen Blick darauf, wo Digital Twins, die diesen Namen tatsächlich verdienen, zum Einsatz kommen, dann sieht man insbesondere den Bereich hochkomplexer Investitionsgüter: Windräder und Turbinen, Kraftwerkelemente und spezielle Maschinen. Hier lohnt sich der Aufwand für den Aufbau eines digitalen Zwillings und hier besteht auch die Möglichkeit, genügend Betriebs- und Zustandsdaten zu sammeln, um ein valides Abbild zu entwerfen. Und hier bietet der digitale Zwilling einen wirklichen Mehrwert.
Denn wenn man beispielsweise zu einer Flugzeugturbine, die sehr teuer, kritisch und langlebig ist, einen Digital Twin aufbaut, kann man im Idealfall sehr genau voraussagen, wann es zu einer Materialermüdung oder Funktionsstörung kommt, wann die Turbine präventiv überholt werden muss und welche Umweltbedingungen besonders kritisch ist. Damit spart man natürlich sehr viel Geld, denn es gibt nichts Teureres als ein im Hangar stehendes Flugzeug. Und darüber hinaus kann man auch lernen, wo generell die Schwachstellen der Konstruktion sind, und daraus wichtige Schlüsse für die zukünftige Fertigung ziehen.
So weit, so gut, spannend und vielversprechend. Und dennoch greift diese Interpretation eines Digital Twin viel zu kurz. Denn mit dem oben beschriebenen Ansatz gewinnt man durchaus wertvolle Erkenntnisse im Hinblick auf die Optimierung eines Produktes und seine Wartung. Aber einen richtigen Optimierungshebel erhält man erst, wenn nicht nur das Produkt, sondern der gesamte Prozess oder sogar das gesamte Wertschöpfungsnetzwerk verbessert ist. Erst wenn Digital Twins für Prozesse und nicht nur für Produkte etabliert sind, kann man das ganze Potenzial der Digitalisierung und Vernetzung heben.
Den Startpunkt bildet die Definition von Prozessparametern, die einen Einfluss auf die Performance der Anlage haben können.
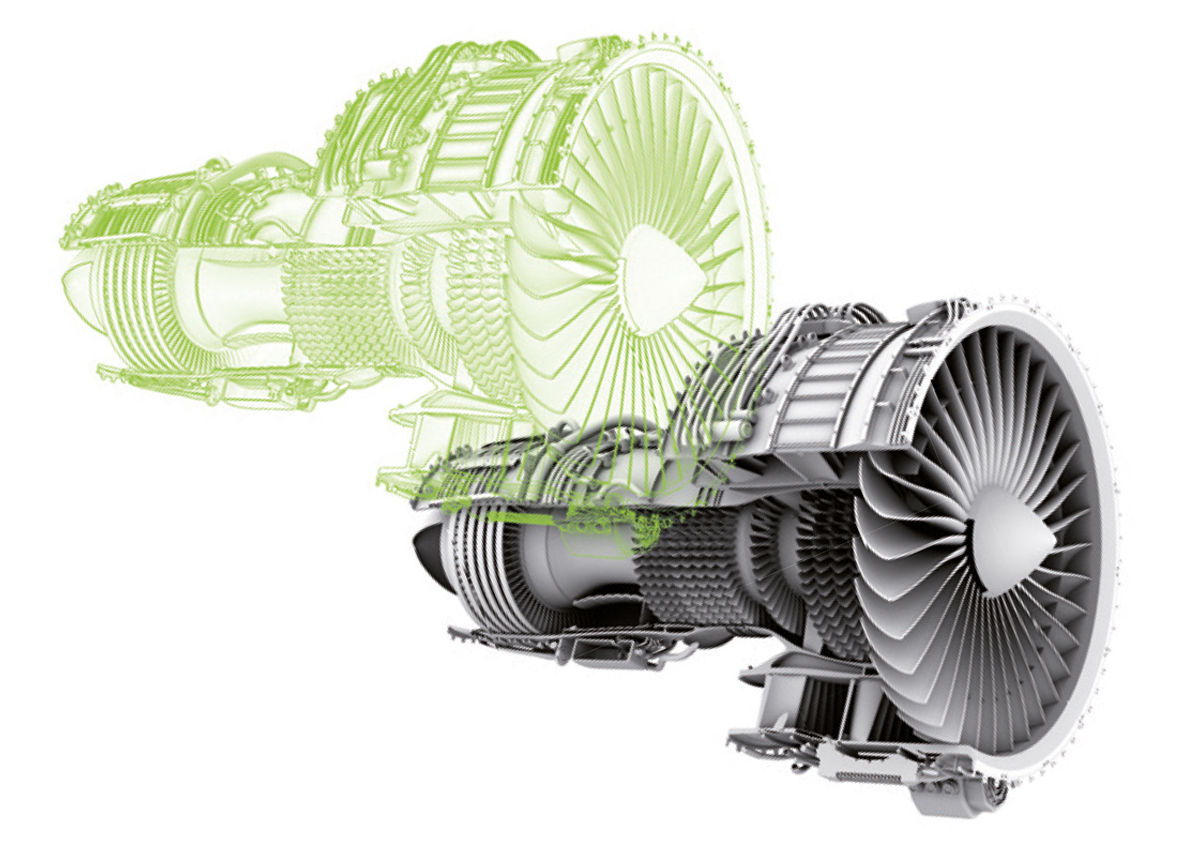
Effizienz- und Qualitätssteigerung sind bei weitem nicht die einzigen Vorteile, die mit einem "Digital Process Twin" erreicht werden können.
Wie kann man sich den Aufbau eines Digital Twin für einen Prozess vorstellen?
Nehmen wir beispielsweise eine Fertigungsanlage für Armaturentafeln in der Automobilindustrie, in der Polyurethan-Schaum verarbeitet, also geformt und gehärtet wird. Dabei hat man häufig eine verhältnismäßig niedrige Effizienz und hohe Ausschussrate, gerade vor dem Hintergrund der sehr hohen Standards der Branche. Das Problem liegt hier nicht auf der Ebene des Produktes, sondern auf der Ebene des Prozesses. Um diesen Prozess zu verbessern, wird nun ein Digital Twin aufgebaut.
Den Startpunkt bildet dabei die Definition von Prozessparametern, die potenziell einen Einfluss auf die Performance der Anlage haben können. Die Ableitung dieser Werte ist erfahrungsbasiert und kann zunächst weit über hundert unterschiedliche Parameter erfassen, die im weiteren Analyseverlauf reduziert oder auch ergänzt werden können. Im zweiten Schritt gilt es dafür zu sorgen, dass die vorhandenen Prozessdaten richtig aggregiert und aufbereitet werden, Daten, die erfassbar sind, aber bislang nicht aufgenommen wurden, gesammelt werden oder dass bislang nicht erfasste, aber im Hinblick auf die definierten Parameter notwendige Daten durch zusätzliche Sensorik gemessen werden. Die auf diese Weise generierte Datenbasis wird anschließend in einer Cloud-Anwendung zusammengeführt und analysiert. Auf dieser Grundlage entsteht nun ein Modell, das den zu verbessernden Prozess möglichst genau abbildet: die relevanten Parameter, deren Wechselwirkungen und kritische Werte. Besonders interessant dabei ist, dass dieses Modell auch weit über das eigene Unternehmen hinausreichen kann – wie der Prozess selbst. So kann er im obigen Beispiel auch zum Logistiker, der den Schaum transportiert, oder sogar zum Hersteller des Schaums reichen. Denn die Problemursachen – etwa die für das empfindliche Polyurethan gefährlichen Temperaturschwankungen – können an jeder Schnittstelle der Wertschöpfungskette entstehen. Im Ergebnis erhält man ein digitales Prozessabbild, das den gesamten physischen Prozess in Echtzeit überwacht und ein frühzeitiges Eingreifen auf Basis kritischer Prozessparameter erlaubt – einen „Digital Process Twin“.
Die Effizienz- und Qualitätssteigerung
sind die naheliegenden, doch bei Weitem nicht die einzigen Vorteile, die mit einem „Digital Process Twin“ erreicht werden können. So bietet der Ansatz völlig neue Möglichkeiten in der Bewertung, Steuerung und Qualifizierung von Lieferanten. Denn durch den Einsatz der virtuellen Prozessmodelle lassen sich die tatsächlichen Strukturen und Prozesse in der Wertschöpfungskette sehr viel präziser und tiefgreifender analysieren als mit den heute üblichen Checklisten und Lean-Manuals. Damit hat man einerseits einen sehr guten Hebel zur Qualifizierung der Lieferanten. Andererseits können neue Partner wesentlich schneller und einfacher integriert werden, was Abhängigkeiten reduziert und den Aufbau neuer lokaler Produktionsstätten erleichtert. Damit werden virtuelle Prozesszwillinge auch zu einem eminent strategischen Faktor beim Aufbau eines smarten Supply Chain Managements.