QUALITÄT IST KEIN LUXUS
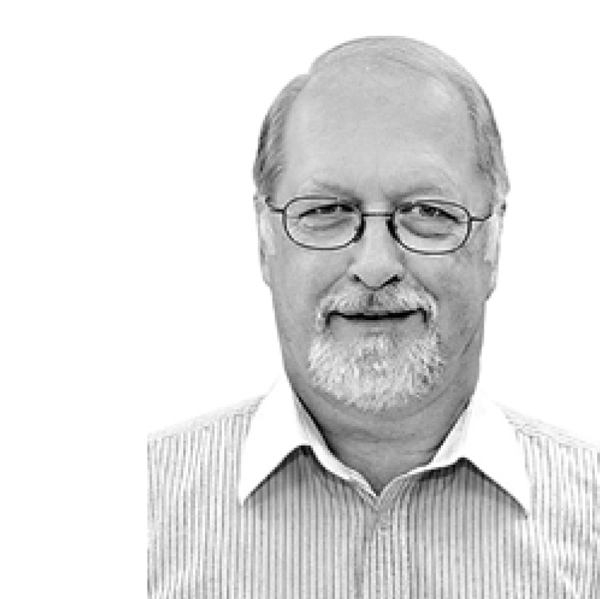
Mit verbesserter Qualitätssicherung greift der Automobilhersteller Brilliance nach dem chinesischen Premium-Segment
Heiß laut, umkämpft und extrem hochtourig: Chinas Automotive- Markt gleicht einem NASCAR-Rennen. Der Unterschied: In China befinden sich deutlich mehr Akteure auf einer deutlich unübersichtlicheren Strecke. 90 in- und ausländische OEMs konkurrieren derzeit auf diesem Markt, in den kommenden drei bis fünf Jahren sind Überkapazitäten von bis zu 10 Millionen Fahrzeugen möglich. Dem damit zu erwartenden Margendruck begegnen viele Hersteller bereits mit Konsolidierungsstrategien. Denn auch in China gilt, dass hohe Absatzzahlen und geringe Preise nicht die ausschlaggebenden Kriterien für eine Pole- Position im Markt sind, sondern eine gute Fahrzeugqualität und ein solides Markenimage über den langfristigen Erfolg entscheiden. Genau diese Ziele hat sich der 2002 gegründete, staatliche Automobilhersteller Brilliance gesetzt, der bereits zu den chinesischen Top 10 OEM zählt. Das Unternehmen möchte seine bislang auf die Mittelklasse, Minivans und Kleintransporter beschränkte Fahrzeugpalette schrittweise hin zum chinesischen Premium-Segment erweitern und dabei die Qualität signifikant steigern.
Drei Schaltstufen zur messbaren Qualitätsverbesserung
Bislang litt das Markenimage unter einer veralteten Technik und schlechten Crashtestergebnissen. Um den Wandel zur Luxusmarke zu vollziehen, muss Brilliance also vor allem einen raschen, signifikanten und nachhaltigen Qualitätsfortschritt in allen Produktionsbereichen wie Presswerk, Rohbau, Lackiererei, Endmontage und dem Motorwerk erreichen. Hierfür nutzt der Automobilhersteller seit Juni 2012 die Expertise der ROI Management Consulting AG. „Die guten Erfahrungen mit ROI in der Vergangenheit haben mich überzeugt, auch dieses Mal wieder das Team an Bord zu holen“, sagt Franz Gollmann, Leiter Central Quality bei Brilliance Automotive.
Während des gesamten Projektes überprüft das ROI-Team anhand unterschiedlicher KPIs wie den Audit Scores für das Gesamtfahrzeug, den Gewährleistungsund Kulanzkosten sowie der Dauer der Nachbearbeitung pro Modell, welche messbaren Qualitätsergebnisse erreicht wurden. Entsprechend sind in insgesamt drei Projektphasen so viele qualitätsrelevante Verbesserungspotenziale wie möglich zu identifizieren und schnell in die tägliche Anwendung zu bringen. Bereits abgeschlossen ist die Analysephase, in der das Team mit Hilfe von Lean Scans die Prozesse der gesamten Fertigungskette identifizierte und teilweise neu definierte. Besondere Aufmerksamkeit erhielten dabei Messpunkte wie das Prozessdesign und die Qualität von Karosserien und Teilen. Aber auch die Prozess- und Fertigungsmanagement- Standards sowie die Mitarbeiterkompetenzen kamen auf den Prüfstand.
„Gute Fahrzeugqualität und ein solides Markenimage entscheiden über den langfristigen Erfolg.“
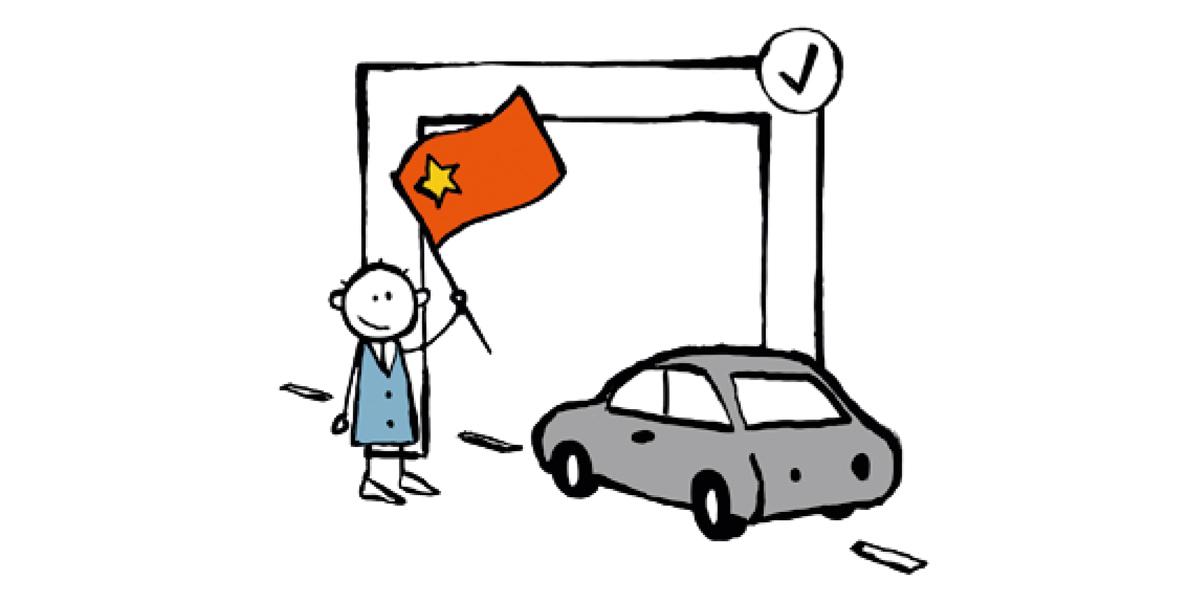
In der zweiten Phase standen die Mitarbeitertrainings und Pilot-Implementierungen verbesserter Fertigungsabläufe im Vordergrund. Nach der Methode der 5S-Arbeitsgestaltung optimierte das Projektteam dabei Arbeitsplätze in verschiedenen Gewerken (z.B. Rohbau und Montage) der Brilliance-Fertigung. Zum einen hinsichtlich Ordnung und Sauberkeit, um eine störungsfreie Umgebung zu schaffen und das Risiko von Arbeitsunfällen zu senken. Zum anderen, um die Basis für die Herstellung qualitativ verbesserter Fahrzeuge zu erhalten. Die Mitarbeiter nahmen die neue Arbeitsplatzgestaltung sehr positiv an. „Bis dato waren viele Arbeitsplätze unübersichtlich und ohne jegliches visuelles Management, was zu ineffizientem Arbeiten und in der Folge zu Qualitätsmängeln führte“, berichtet Gollmann. „Die Belegschaft soll in Zukunft sehr sensibel Verbesserungschancen erkennen. Dazu haben wir Qualitäts-Gates von der Karosseriepresse bis zur Endmontage eingeführt. Zusammen mit Qualitätsregelkreisen und der Einführung einer strukturierten Problemlösungsmethodik wollen wir sicherstellen, dass die Mängelquote immer weiter sinken wird.“ In der dritten Projektphase erfolgt aktuell der Roll-Out aller identifizierten Verbesserungsmaßnahmen in beiden Fabriken. Dazu sorgt das Projektteam mit einem gezielten Coaching der Brilliance- Mitarbeiter dafür, dass die neuen Prozesse stabil und adaptiv für zukünftige Veränderungen sind. „Wir bilden derzeit 12 Mitarbeiter als Multiplikatoren aus, um die ersten Erfolge möglichst rasch auf alle Produktionsbereiche auszuweiten. Tatsächlich haben nicht nur die Methoden wie 5S und die strukturierte Problemlösungstechnik ‚A3‘ bereits sehr gute Ergebnisse erbracht, sondern es ist auch gelungen, die chinesischen Kollegen für ein ganz neues Qualitätsverständnis zu sensibilisieren. Dadurch hat sich der Nacharbeitsaufwand bereits jetzt an manchen Stellen deutlich verringert. Dies zeigt sich beispielsweise bei den Rohbaukarossen des neuesten Zhonghua Modells“, betont Gollmann.
„Mithilfe von eingeführten Qualitäts-Gates sollen Mitarbeiter zukünftig sehr sensibel Verbesserungschancen erkennen.“
Interkulturelles Fahrwerk als Erfolgsfaktor
Neben den ersten Erfolgen bei messbaren KPIs der Qualitätssicherung profitieren alle Beteiligten von Erfahrungen im interkulturellen Austausch. Schließlich hatte die Brilliance Belegschaft zuvor fast keine westlichen Produktionsstandards kennengelernt, außerdem sind die Arbeits- und Kommunikationsprozesse noch von typischen chinesischen Strukturen geprägt: Bürokratie und Parteifunktionäre in Management Funktionen können Arbeitsabläufe erschweren, ohne sich an Meilenstein-Pläne gebunden zu fühlen. Somit dauert es auch viel länger als in westlich strukturierten Firmen, verbesserte Prozesse zu implementieren und ein echtes Qualitätsbewusstsein zu schaffen. Generell überwiegen jedoch die positiven ‚lessons learned‘ des Projektes, die Franz Gollmann hervorhebt: „Die Brilliance- Mitarbeiter sind sehr motiviert, lernwillig und liefern bei guten, klaren Arbeitsanweisungen auch gute Ergebnisse. Ein klarer Erfolgsfaktor sind auf jeden Fall gemischte Teams, die gemeinsam an einer Aufgabe arbeiten.“
Diesen interkulturellen Ansatz unterstützt das ROI-Team mit einer Kombination aus chinesischen Consultants und deutschen Beratern mit jahrelanger Erfahrung bei asiatischen OEM und Zulieferern. So gelang es dem Projektteam bei Brilliance, nach gemeinsamen ‚A3‘- Problemlösungs- Workshops im Rohbau, ein langwieriges Problem mit unregelmäßigen Spaltmaßen an der Fahrzeugkarosse zu optimieren und zu stabilisieren – ein weiterer Schritt in Richtung chinesischer Premium- Klasse.
„Ein klarer Erfolgsfaktor sind gemischte Teams, die gemeinsam an einer Aufgabe arbeiten.“
Brilliance China Automotive Holdings Limited
ist einer der führenden Automobilhersteller Chinas, vor allem in den Segmenten Minivans und Kleintransporter. 2003 gründete der Konzern ein Joint Venture mit BMW, die BMW Brilliance Automotive Ltd, um BMW 3er und 5er Limousinen in China zu produzieren.
www.brillianceauto.com