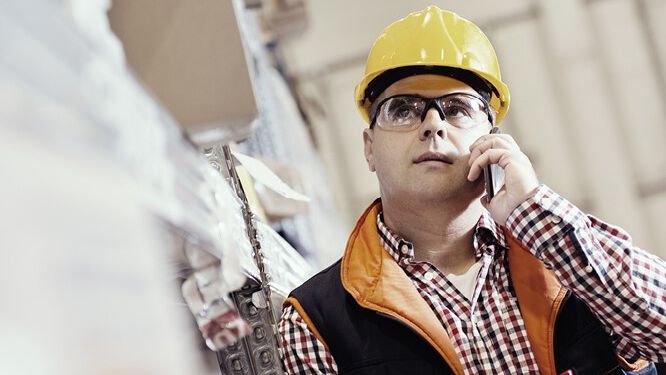
Intralogistik: Ausblick bis ins Jahr 2030
Technologische Orientierungspunkte für die ideale Logistik
Beschleunigt eine Datenbrille die Kommissionierung? Oder lohnt sich eher eine Investition in ein Pick by light-System? Bislang standen neue Technologien für die Intralogistik nicht weit oben auf der Prioritätenliste von Unternehmen. Denn der Kostenanteil der Logistik ist geringer als der anderer Arbeitsbereiche und deren Digitalisierungsbedarf in der Regel größer. Doch das ändert sich rapide: vom Pick-per-Voice-Tool bis zum autonomen Lagerroboter sind immer mehr Instrumente verfügbar. Wer das heute verfügbare Spektrum kennt, schützt sich vor Fehlinvestitionen – und wer es bis ins Jahr 2030 im Blick hat, kann bei jedem Technologiewechsel profitieren. Genau diesen Vorausblick verschaffte sich ein Global Player der Halbleiterindustrie. Gemeinsam mit EFESO entwickelte der Chiphersteller ein standortübergreifendes Intralogistik-Konzept bis zum Jahr 2030.
Herausforderung
Ein globaler Marktführer der Halbleiterindustrie stellt seine Intralogistik auf den Prüfstand. Für noch bessere Abläufe wird ein standortübergreifendes Technologie-Konzept für die Intralogistik bis zum Jahr 2030 entwickelt.
MEHREFESO Lösungsansatz
Statt Fiktion eine klar strukturierte, methodische Vorgehensweise. Guidelines schaffen Orientierungspunkte für den Weg zur idealen Logistik bis 2030.
MEHRLessons Learned
Nur konsolidierte Logistikfunktionen ermöglichen effiziente Prozesse und helfen, Synergiepotenziale zu identifizieren und zu nutzen.
MEHREFESO Erfolgsmodell
Komplexität auf das Wesentliche herunterbrechen: die Übersichtsmatrix des „morphologischen Technologiekasten“ führt Handlunsfelder und Zeitachsen auf einem DIN-A4 Blatt zusammen.
MEHRLogistik 4.0 methodisch planen
Bei dem Projekt gaben allerdings Strategie und Methodik anstelle von Science-Fiction Szenarien den Takt vor. Die Orientierungspunkte für den Blick in die Zukunft sollten eben nicht abstrakte Trendthemen wie Künstliche Intelligenz sein, sondern konkrete Technologien, die für das Unternehmen wirtschaftlich sinnvoll und standortübergreifend umsetzbar sind. Dabei wandte das Projektteam aus EFESO-Beratern und den Logistikentscheidern des Chipherstellers ein dreistufiges Verfahren an:
- Status Quo ermitteln
- Vision bis 2030 entwickeln (anhand eines Konzeptes für die ideale Logistik)
- eine Machbarkeitsplanung vornehmen (anhand der Gegebenheiten in den Werken inkl. einer Wirtschaftlichkeitsberechnung)
Status Quo ermitteln
Im ersten Schritt besuchte das EFESO-Team fünf repräsentative Standorte der Backend- und Frontend-Produktion des Unternehmens, um dort den Status Quo der internen Logistikprozesse festzuhalten. Die Produktion des Chipherstellers zeichnet sich durch einen hohen Industrie 4.0-Reifegrad aus, mit einem weit entwickelten Automatisierungsgrad und vernetzten Wertschöpfungsstufen zwischen den Fertigungslinien der Werke. Umso deutlicher erwies sich dazu die Logistik als Kontrastprogramm: Trotz verschiedener Leanansätze verwendete man dort digitale Technologien eher rudimentär. Der Informationsfluss lief papierbasiert, automatisierte Prozesse waren die Ausnahme und nicht die Regel. Die verschiedenen Lager für die Teilegruppen verteilten sich über das gesamte Areal oder befanden sich aus Platzgründen ausserhalb des Fabrikgeländes. Ein zentrales Logistikcenter gab es nicht. An manchen Standorten war die Logistik zudem outgesourct, die Abwicklung übernahmen externe Dienstleister.
Hinzu kam die Komplexität des Teilespektrums: Zigtausende unterschiedliche Microelektronikkomponenten und sehr viele Ersatzteile mussten vorgehalten und gelagert werden. Täglich produziert das Unternhemen hunderttausende Microchips, aber weil diese so klein sind, gibt es kaum Palettenbewegungen. Das erwies sich für das Projekt als wesentlicher Faktor. Schließlich sind Palletenbewegungen für die Logistik eine wichtige Kerngröße um festzustellen, ab wann sich eine Automatisierung rechnet. Bei täglich tausenden bewegten Palleten ist sie sinnvoll, bei weniger als hundert Paletten am Tag nicht.
Vision bis 2030 entwickeln
Im nächsten Projektschritt entwickelte das Projektteam eine „Vision“ für die Intralogistik, die sowohl konkrete Zielsetzungen als auch speziell für das Unternehmen geeignete Technologien benennt. Die Ziele sollten die zukünftigen Produktionsanforderungen sowie die sich verändernden Kunden- und Marktanforderungen berücksichtigen, insbesondere hinsichtlich:
- höchster Effektivität und Effizienz;
- der richtigen Geschwindigkeit bei der Erbringung von Dienstleistungen;
- einer Aufwärtskompatibilität von neuen technologischen Lösungen;
- acht "R´s“: Richtiges Produkt, Qualität, Zeit, Ort, Menge, Verpackung, Kosten und Informationen, kontrolliert durch KPIs.
Als weiteres wesentliches Element entwickelte das Projektteam einen sogenannten „morphologischen Kasten“. Dieser zeigt in einer Übersichtsmatrix die Hauptaktivitäten der Logistik, wie Handling, Transport, Lager und Informationsbereitstellung im Werk und benennt Technologien, die zu Verbesserungen führen könnten. Zugleich ordnet er diese Aktivitäten drei Zeitabschnitten für die Umsetzung zu.
Aus diesen beiden Elementen leitete der Chiphersteller seine individuelle Intralogistik-Vision bis 2030 ab. In realistischen Schritten kann das Unternehmen nun die technologische Weiterentwicklung voran treiben, ohne weitere, tatsächlich relevante Technologien aus dem Blick zu verlieren.
Im Idealfall vereint es außerdem alle Funktionen vom Wareneingang über die Lagerung bis hin zum Versand in einem geeigneten und zweckmäßigen Logistikgebäude, um so die notwendige Prozessqualität sicherzustellen. Für den späteren, optionalen Aufbau eines solchen „Warehouse 4.0“ formulierte das Projektteam die folgenden „Guiding Principles of Warehouse Optimization“:
- Errichte ein voll funktionsfähiges, konsolidiertes On-site Logistikzentrum.
- Gestalte dessen Prozesse durchgängig.
- Realisiere eine Logistik mit möglichst wenigen Prozessschritten.
- Setze state-of-the-art Technologien ein (insb. intelligente Datenanalyse) – sofern sie materielle und immaterielle Vorteile erzielen.
- Vermeide eine Lagerauslastung von über 85%, da dies zu Ineffizienz führt.
Machbarkeitsplanung vornehmen
Im letzten Schritt erstellte das Projektteam anhand der formulierten „Vision 2030“ für jeden Standort des Chipherstellers Machbarkeitsplanungen: Welche Technologie rechnet sich wo? Was ist für die nächsten fünf Jahre unrealistisch, aber vielleicht in zehn Jahren günstiger verfügbar und hilfreich im Einsatz? Dazu initialisiert das Unternehmen nun regelmäßig Pilotprojekte, zum Beispiel um Fahrerlose Transportsysteme zu testen oder die Alltagstauglichkeit von Datenbrillen, die den Lageristen Arbeitsaufgaben anzeigen. Dieses Vorgehen schützt vor Fehlinvestitionen und macht die Zukunft der Intralogistik „step-by-step“ erfahrbar.