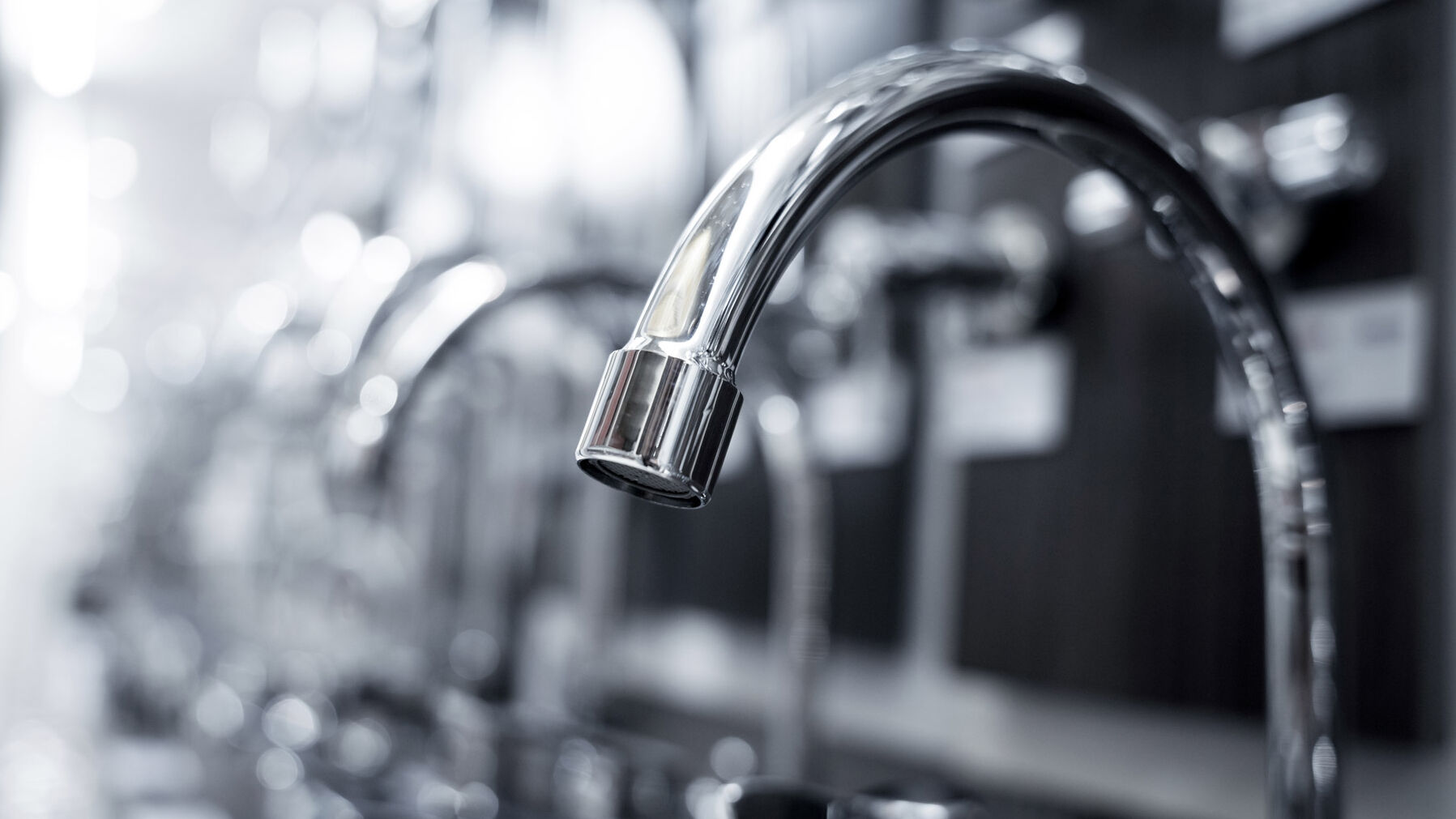
Standortsicherung dank schlanker Wertströme
Effizienzsteigerung und Kostensenkung bei einem Armaturenhersteller
Ein namhafter Hersteller von Premiumarmaturen will seine Spitzenposition im internationalen Wettbewerb stärken. Die Standortsicherung in Deutschland hat dabei oberste Priorität: mit harten Zielen für den gesamten Operations-Bereich und mit der Unterstützung von EFESO stellt sich ein Werkstandort als Fabrik der Zukunft komplett neu auf.
Herausforderung
Ein Hersteller von Premiumarmaturen bringt mit EFESO die Prozesse und Strukturen eines Werkes auf ein neues Leistungsniveau. Die ambitionierten Projektziele sind über einen Bottom-up-Ansatz mit Vor-Ort-Optimierungen nicht erreichbar – eine komplette Neuausrichtung der traditionell gewachsenen, funktionalen Produktionsstrukturen ist notwendig.
MEHREFESO Lösungsansatz
Das Projektteam kombinierte eine umfassende Initiative zur Komplexitätsreduktion mit einer wertstrombasierten Gestaltung der Produktions- und Logistikprozesse – und erreichte so eine maximale Reduktion der Herstellkosten. Die Zero-Base-Dimensionierung der indirekten Funktionen sowie deren Integration in die Wertströme führte zu schlankem Overhead.
MEHRLessons Learned
Die frühe Entwicklung eines Zielbildes der „Schlanken Fabrik der Zukunft“ macht die Dimension der Veränderungsbedarfe transparent. Zudem sollten die Mitarbeiter intensiv eingebunden und in der Anwendung von Lean-Prinzipien qualifiziert werden.
MEHREFESO Erfolgsmodell
Die Fokussierung auf eine wertstromorientierte und schlanke Produktionsstruktur sowie deren konsequente physische Umsetzung im Shopfloor erwiesen sich als wesentliche Erfolgsfaktoren im Projekt.
MEHRZiel: die OEE über 85% bringen.
Ambitionierte Ziele für ein leistungsstarkes Werk
Die Marke hat weltweit mit Qualitätsprodukten „Made in Germany“ einen hohen Bekanntheitsgrad erreicht. Um diese Erfolgsgeschichte mit weiteren Kapiteln fortzusetzen, beschloss die Unternehmensleitung die weitreichende Restrukturierung eines deutschen Werkstandortes. Dazu formulierte sie klare Zielsetzungen: Herstellkosten sowie Bestands- Durchlaufzeiten sollen deutlich sinken, wobei eine Gesamtanlageneffektivität (OEE, Overall Equipment Effectiveness) jenseits der 85% angestrebt wird.
Zudem galt es, die bereits hohe, weiter zunehmende Kundennachfrage zu erfüllen, also steigende Volumina mit den bereits vorhandenen Kapazitäten zu realisieren. Hierbei sollten u.a. nicht nur die Produktivität der Mitarbeiter um 25% steigen, sondern auch der Servicegrad und die Ablieferqualität im Werk auf ein neues Niveau gebracht werden – etwa mit einer signifikanten Erhöhung des Anteils der fehlerfrei hergestellten Produkte.
Um diese und weitere Ergebnisse zu realisieren, holte die Werksleitung EFESO als Umsetzungspartner mit an Bord. Ein gemeinsames Projektteam mit Produktions- und Logistik-Experten durchleuchtete die Prozesse im Werk vom Shopfloor bis zum Boardroom.
Alle direkten und indirekten Funktionen im Werk werden neu gestaltet.
Komplette Neuausrichtung der Werksstrukturen
Das Team sah sich beim Projektstart mit einer besonders komplexen Aufgabenstellung konfrontiert, in der drei Handlungsstränge miteinander in Einklang zu bringen waren:
- Die Kundenzufriedenheit zu sichern und zu steigern, insbesondere über den Servicegrad, die Ablieferqualität und eine kürzere Time to Market durch einen verbesserten Industrialisierungsprozess.
- Alle zentralen Ratio- & Effizienz-KPI zu verbessern, etwa bei Fertigungs- und Qualitätskosten sowie bei den Lagerbeständen und Durchlaufzeiten.
- Gemeinsam mit allen Mitarbeitern einen weitreichenden Transformationsprozess umzusetzen.
Die Benennung der Ziele für jeden einzelnen Teilbereich erwies sich dabei noch als einfach umzusetzen. Eine größere Hürde lag darin, diese drei Handlungsstränge bei der Maßnahmenumsetzung simultan zu koordinieren, so dass am Ende das bestmögliche Ergebnis erreicht wird.
Die richtigen Dinge machen – und die Dinge richtig machen.
Vier Module für simultane Verbesserungen
Um diese Herausforderungen zu meistern, kombinierte das Projektteam eine umfassende Initiative zur Komplexitätsreduktion („die richtigen Dinge machen“) mit einer wertstrombasierten Gestaltung der Produktions- und Logistikprozesse („die Dinge richtig machen“). Damit erreichte es nicht nur eine maximale Reduktion der Herstellkosten. Die Zero-Base-Dimensionierung der indirekten Funktionen wie Qualität, Instandhaltung oder logistische Steuerung führte darüber hinaus zu einem schlanken Overhead. Ihre Integration in die Wertströme verbesserte die Kostenposition zusätzlich.
Dabei unterteilte das Team das Gesamtprojekt in mehrere Module, die in der Umsetzung weitestgehend parallel abliefen:
Modul 1: Komplexitätsreduktion
- Ermittlung der wesentlichen Komplexitätstreiber in Produktion und Logistik, z.B. nicht abgeschlossene Verlagerungen, Produkte mit geringem Wertschöpfungsanteil, gewachsene Zulieferbeziehungen im Werksverbund, einfache manuelle Produktionsprozesse.
- Darauf aufbauend: Definition der künftigen Kernkompetenzen, Portfolio-Bereinigung, Optimierung der Intercompany-Lieferbeziehungen, Verbesserung der Auslaufsteuerung.
Modul 2: Neue Werkstruktur - Konzept zur Neuausrichtung der Produktions- und Logistikprozesse nach Lean Manufacturing Prinzipien
- Abstimmung der Anforderungen aus dem zentralem Supply Chain Management an das Werk: Make-to-stock, Make-to-order, differenzierte Service-Level, Einsteuerung neuer Projekte.
- Definition der Future Value Streams und Entwicklung eines Werkssegmentierungskonzeptes, z.B. Segmente für komplexe High Runner, einfache High Runner, Low Runner. Dies beinhaltete die Zuordnung der Betriebsmittel und Personalkapazitäten zu den Fertigungseinheiten.
- Festlegung der Steuerungspunkte, Bevorratungsebenen, Abgrenzung Push-Pull-Steuerung.
Beispiel zur Definition von Future Value Streams
Modul 3: Effizienzsteigerung in den indirekten Bereichen
- Ermittlung von Verschwendungspotenzialen in Funktionen wie Instandhaltung, Logistik, Qualität, Werkzeugbau.
- Quantifizierung von Potenzialen durch Zero-Base-Ansatz und EFESO-Benchmarks.
- Definition von Ansätzen zur Neuorganisation und Integration in die Fertigungssegmente, inkl. Re-Dimensionierung der erforderlichen Kapazitäten.
Modul 4: Organisationsentwicklung und Qualifizierung
- Entwicklung der Werksorganisation, abgeleitet aus dem Value-Stream- und Segmentierungskonzept.
- Erstellung eines Führungs- und Zielsystems zur Steuerung der autonomen Einheiten.
- Erstellung von Anforderungsprofilen an Segmentleiter und Spiegelung mit dem Stand der Qualifizierung.
- Definition neuer Rollenbeschreibungen und Ableitung darauf ausgerichteter, zielgruppenspezifischer Qualifizierungsprogramme.
Parallel zur Konzepterarbeitung und der physischen Veränderung der Werkstruktur wurde ein umfassendes und stringent gesteuertes Programm zur Umsetzung strukturunabhängiger Maßnahmen mit schnellem Payback / ROI aufgesetzt:
- OEE-Steigerungsprogramm
- Qualitäts- und Prozessstabilisierungsinitiative
- Bestandsmanagement
- Lean-Piloten in der Montage mit One-Piece-Flow
- TPM-Initiative
- Lean Administration
Veränderungsbedarf transparent machen
Bereits in den frühen Projektphasen erwiesen sich die folgenden Vorgehensweisen und Erfahrungen als wichtige Hebel zur Umsetzung der Ziele:
- Die frühe Entwicklung eines Zielbildes der „Schlanken Fabrik der Zukunft“ macht die Dimension der Veränderungsbedarfe, insbesondere in den physischen Abläufen in Produktion und Logistik greifbar. Dieses Zielbild erwies sich als wesentlicher Referenzpunkt für die strukturierte Konzept- und Realisierungsplanung des Werkes. Der Lean-Bezug lieferte außerdem wichtige Hinweise auf Komplexitätstreiber und Ansatzpunkte, wie sich diese reduzieren bzw. ganz vermeiden lassen.
- Transformationsmanagement und Leadership sind entscheidend für den Projekterfolg. Die intensive Einbindung der Mitarbeiter sowie deren parallele Qualifizierung in Lean-Prinzipien ermöglich eine hohe Akzeptanz der gemeinsam erarbeiteten Lösungen und motiviert zur Mitwirkung. Zudem räumt ein überzeugtes Commitment und Statement der Führungsmannschaft zum Zielkonzept Bedenken zur Seite und verhindert Kompromisslösungen.
Das Bild der „Fabrik der Zukunft“ schärft den Blick für das Wesentliche.
Erfahrungen aus Best-Practice-Werken nutzen
Die Fokussierung auf eine wertstromorientierte und schlanke Produktionsstruktur sowie deren konsequente physische Umsetzung im Shopfloor erwiesen sich als wesentliche Erfolgsfaktoren im Projekt.
Die Überzeugung der Führungskräfte und Mitarbeiter für das Zukunftskonzept und dessen erfolgreiche Umsetzung gelang durch Besuche von Best-Practice-Werken, ein sehr erfahrenes Beraterteam, sowie eine intensive Kommunikation aller Akteure im Transformationsprozess. Somit konnte der Armaturenhersteller die gesetzten Ziele erreichen – und den Werkstandort optimal auf zukünftige Herausforderungen im internationalen Wettbewerb vorbereiten.