"WE HAVE TO TACKLE SEVERAL CENTURY-LONG CHALLENGES IN PARALLEL"
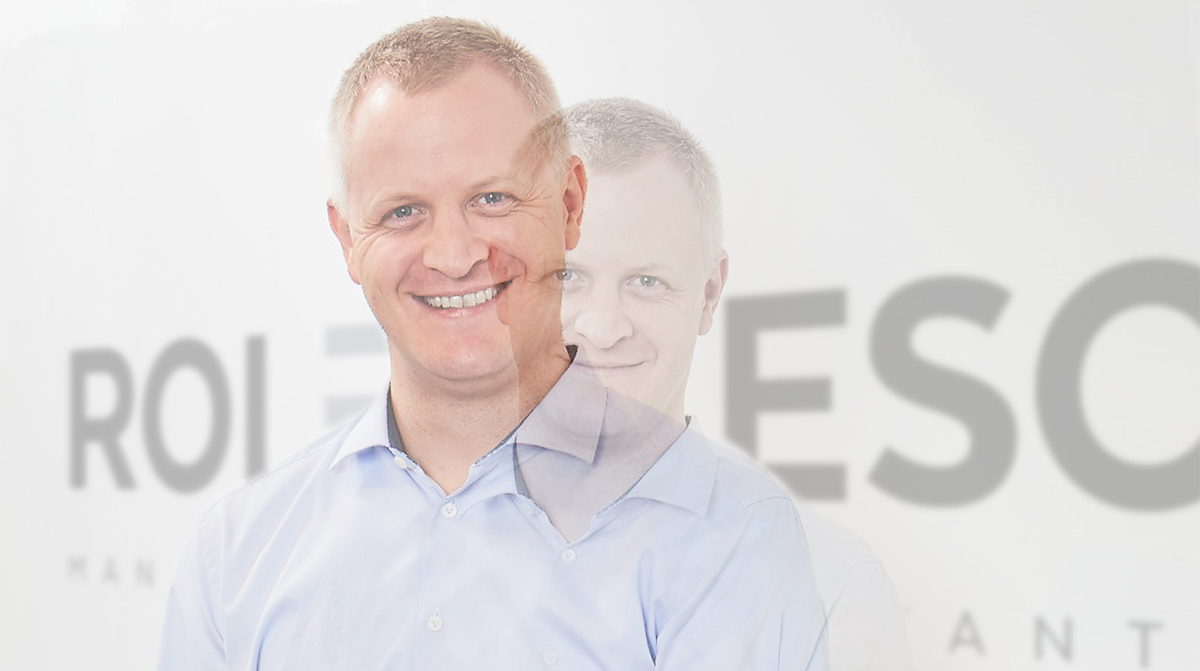
GERMANY
Interview with Sebastian Diers, Managing Director
Sebastian, what challenges will Germany have to overcome as an industrial location in the coming years?
In recent years, we have seen an unprecedented chain of several developments. Severe geopolitical and medical crises, risks of inflation and recession, regulatory changes.
If I limit myself to the area of this complicated situation in which we as EFESO support our customers, the questions of security of supply and, in a comprehensive sense, sustainability and resource efficiency of the production chains arise above all. In addition, resilience will become a strategic imperative in aligning supply chains over the next decade.
Another field is demographic change. Today, every second person in Germany is older than 45. Despite immigration and a rising birth rate, we are therefore running into a problem with skilled workers and qualifications, especially in areas such as digitalization and new forms of work. And finally, we also need tobe thinking about technological transformations, which strongly affect our key industries.
How well prepared is Germany for these developments, in particular with regard to the issues addressed by EFESO?
The answer depends on which area of our highly diversified economy we look at. The supply networks, dependencies and complexity, as well as the saturation and competitive intensity of the markets create specific scenarios. In addition, over the past 10–15 years, companies have addressed the issue of increasing the maturity of their organizations in very different ways. Resilience, robustness, and adaptive capacity vary.
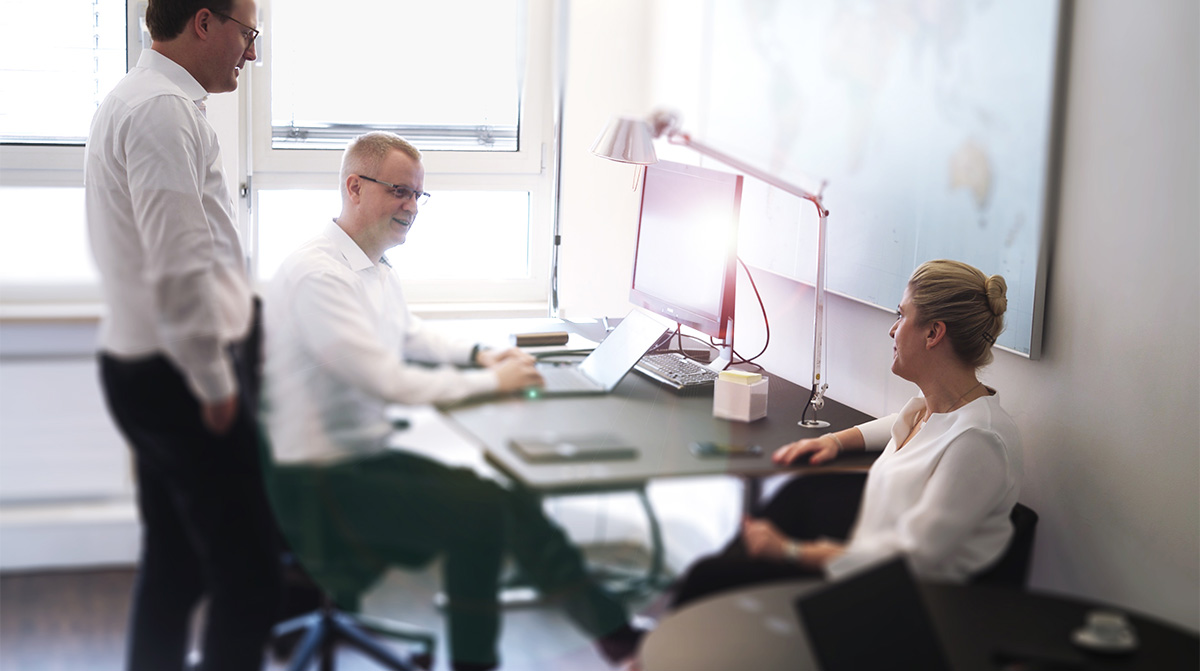
Resilience will become a strategic imperative
in the alignment of supply chains.
Are there also new challenges that are comparable across sectors?
A relatively new experience for most companies in Germany is that even enormously complex transformation projects can no longer be handled sequentially, but must be approached in parallel and networked. We no longer have time to spare; the future draws closer.
The other factor is that the development of a strategic target is becoming increasingly challenging. This process is characterized by great dynamism with regard to trends in customer behavior, technology, geopolitics or regulation. And of great uncertainty with regard to the framework conditions that I have already mentioned.
Therefore, it is only possible to update strategies and derive them from experience to a very limited extent. And we must increasingly look at our own role and position across sectors. Not only because most industries are characterized by convergence. But also because many future challenges can only be answered on a cross-sector basis. On the one hand, sustainability therefore requires trend-conscious and cross-industry strategies. And on the other hand, it requires their rapid and consistent implementation.
How can this implementation be described, and on what does its success largely depend?
The major challenge is to operationalize the mission statement that has been developed, anchor it at all levels of the organization, and ensure that the strategic guidelines for each area of the company areclear and systematically tracked.
We rely on a multi-stage process in which the strategic drivers are first precisely defined based on the target image. The focus can be on topics such as delivery capability, technology, sustainability, or access to critical resources. The strategic drivers are then examined from different perspectives, and the discrepancies between the strategic vision and the actual situation in the company must be clearly identified.
On this basis, central fields of action are defined, whereby a distinction can be made between three basic types: ensuring the stability of certain processes and structures, continuous improvement in areas such as capacity optimization, efficiency enhancement or resource consumption, and finally, break-through initiatives in areas that move the company forward and support the development of new capabilities. In addition to digitalization, these currently include the circular economy, ecosystem management, software centricity, and addressing the shortage of skilled workers.
Two fundamental areas have to be taken to account. Success depends on breaking down these fields of action into precise operational goals so that the process becomes controllable and measurable and provides clarity about the specific contribution that the individual areas can make. People are empowered to work openly, in a multidisciplinary and generalist way, on issues under challenging conditions – beyond silo structures and local egotisms. This approach and the view of the different types of fields of action also imply that the widespread equation of excellence and efficiency is falling short. This has a major impact both on the management systems and on the overall organizational design.
The widespread equation of excellence
and efficiency falls short.
Does this also have consequences for the consulting itself?
I believe that we must become architects of transformation. It is not by chance, that I choose this term. For a good architect, it is not only crutial to crasp a vision and cast it into an image, but also to bring it to fruition in terms of craftsmanship, to erect a building that will endure.
As consultants, we must therefore ensure that we are operationally effective and future-competent for our clients. First of all, this means assessing the complex initial situation and recognizing the blind spots in the design of the company. Where are the markets heading? How massive and how fast are the changes heading our way, and what interactions do we need to take into account? Are there common objectives that are consistent right down to the operational level?
What consequences arise both from the perspective of individual specialist topics and from a cross-thematic and cross-location perspective? What does this mean for structures, processes, technology, the people in the company? What contribution can and must individual departments make? On this basis, we then have to take a deep dive into the technical issues. And there is a very wide range of activities to be covered here, from supply chain management, footprint, operational excellence, R&D, forecasting, planning, digitalization and sustainability to human dynamics. It is only by combining the different skills that we can help companies defend their future viability.
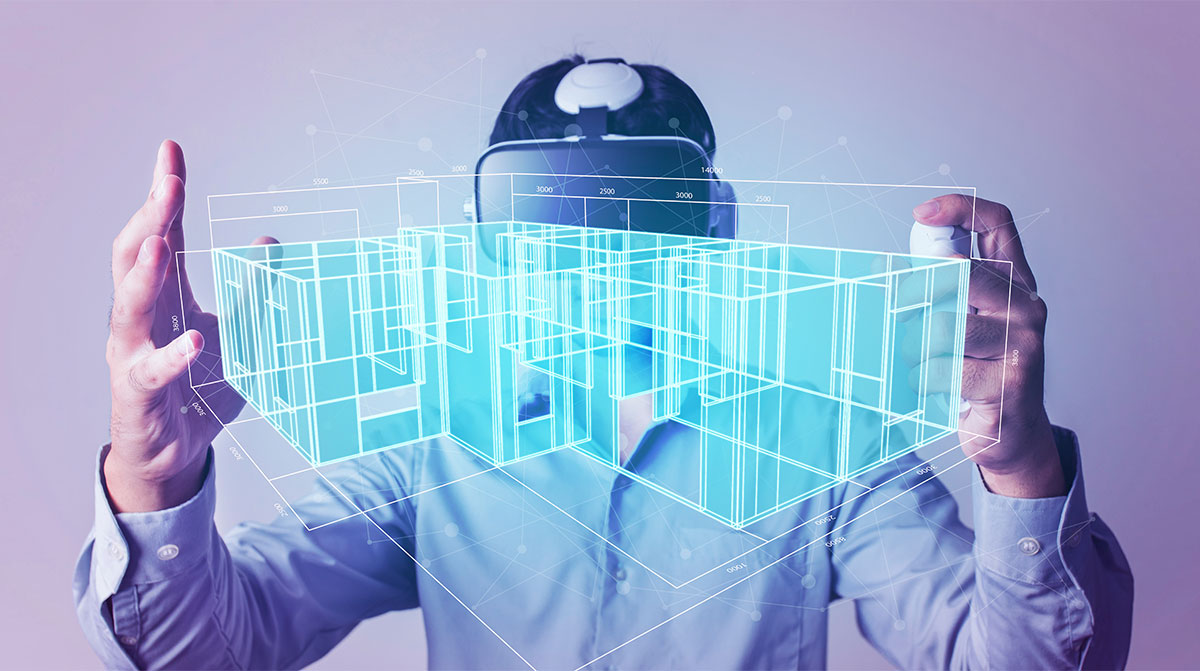
EFESO reference project from Germany: Quality improvement in the automotive industry
With the support of EFESO, one of the world’s leading automobile manufacturers established a completely new practice inspired by the team competition in soccer – and thus achieved unprecedented dynamism in rigid factory structures and work routines.
Challenge
A leading global automobile manufacturer wanted to mobilise and accelerate its entire network of nine factories in terms of cost and quality. To this end, the transfer of know-how between the plants was to be improved.
Approach
EFESO has established a completely new, soccer-inspired practice of competition for table leadership. The project team thus made rigid plant structures and work routines more dynamic. The joy of taking part, motivation and team spirit are now the focus.
Success model
EFESO and the project team implemented the principle of "learning from the best". This ensured not only that several good ideas for OEE optimization of a plant were efficiently generated. But also that they were applied across the whole network to 85%. There is also a KPI check and "spider web" performance review.
Learn more from the detailed case study.
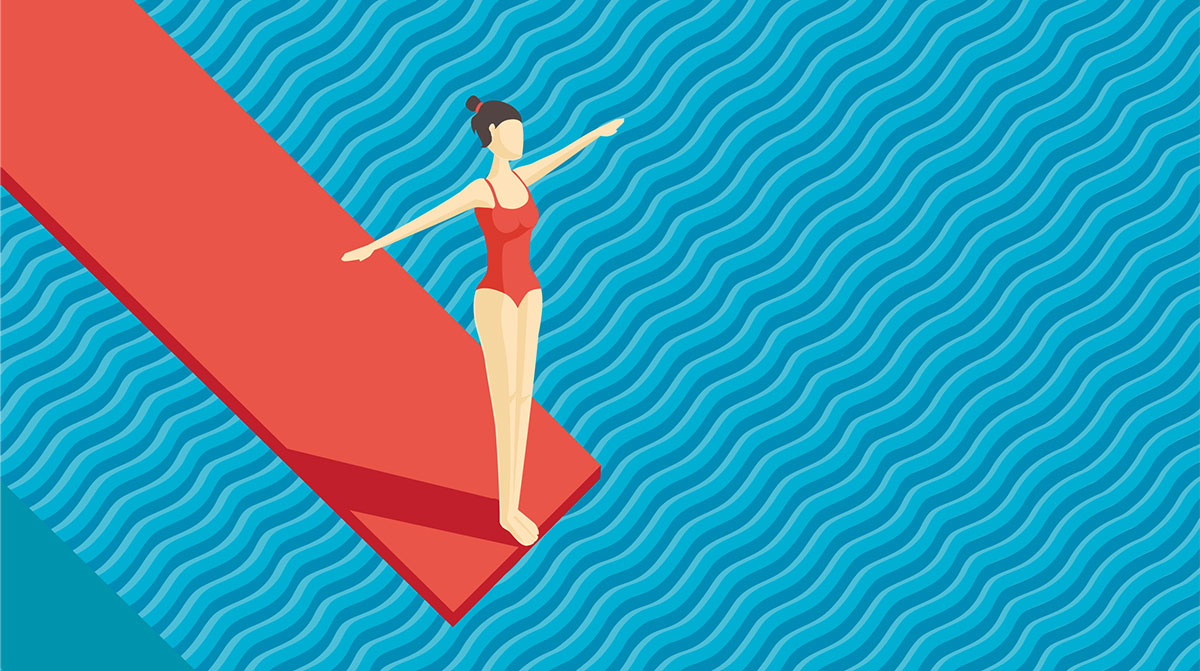
EFESO reference project from Germany: Software bots as assistants for value creation
A manufacturer of machinery and special machines has already achieved a high level of automation in its production processes. Now the company is setting its sights on further, cross-departmental goals for process automation. Together with EFESO, it is defining fields of application in the operations areain which Robot Process Automation (RPA) tools are to ensure time savings and relieve employees.
Challenge
The mechanical engineering company is redesigning its process landscape. Together with EFESO, it defines fields of application in eight departments where Robot Process Automation (RPA) tools are to save time and relieve employees.
Approach
After a cross-departmental kick-off event, EFESO deployed software bots via detailed recording, development and testing in all involved departments of the company. During the test phase, the previous, "real" process and the automated process ran in parallel according to the "tandem" principle.
Success model
Demand-driven development and implementation of RPA with a combination of technology and methodology expertise. The ROI of software bots is not only calculated for one or two pilots, but also for the sum of all use cases.
Learn more from the detailed case study.