LEAN’S LAST RACE?
Kein Managementansatz hat die Produktionssysteme in den letzten dreißig Jahren so stark geprägt wie das Lean Management. Doch obwohl Lean mittlerweile oft als Commodity gilt, wird sein wahres Potenzial bislang kaum ausgeschöpft. Dabei lassen neue Fortschritte in Technologie, Psychologie und Analytik die nächsten dreißig Jahre noch spannender erwarten als die letzten.
Als Usain Bolt am Abend des 16. August 2008 die Ziellinie des Pekinger Olympiastadions passierte, gelang ihm etwas, das es eigentlich nicht geben dürfte. Denn gerade hatte er die 100 Meter in exakt 9,69 Sekunden zurückgelegt. 0,03 Sekunden schneller, als es nach den Berechnungen führender Sportwissenschaftler für einen Menschen physikalisch möglich sei. Mit seinem Spitzenlauf stellte er nicht nur einen neuen Weltrekord auf, sondern auch die Annahmen zu den Grenzen der menschlichen Leistungsfähigkeit infrage.
Die Frage, wie weit man die Optimierung der eigenen Leistung noch vorantreiben kann, beschäftigt auch die Produktionsverantwortlichen in der industriellen Fertigung. Über Jahrzehnte hinweg galt Lean Production als das beherrschende Paradigma, wenn es darum ging, Durchlaufzeiten zu verkürzen, die Maschinenverfügbarkeit zu erhöhen oder Qualitätsstandards abzusichern. Durch die Anwendung von Lean-Prinzipien wie Abtaktung, Pull-Prinzip oder One-Piece-Flow versuchten sie die Effizienz ihrer Produktionssysteme immer weiter auszureizen. Doch mittlerweile haben andere Themen die schlanke Fabrik von der Management-Agenda verdrängt. Und manch einer glaubt angesichts dieser Entwicklung, dass Lean bereits die Grenze seiner Leistungsfähigkeit erreicht hat.
Tatsächlich jedoch stehen die meisten Unternehmen gerade erst am Beginn ihrer Lean-Entwicklung. Zum einen, weil sie bestehende Ansätze bislang oft noch nicht konsequent genug umsetzen und weiterentwickeln. Zum anderen, weil die Integration neuer Technologien in das Lean Management völlig neue Effizienzgewinne ermöglicht. Beides zusammen führt zu Potenzialen, die das bisher erreichte Produktivitätsniveau noch einmal verdoppeln könnten. Oder anders ausgedrückt: etwa so, als würde Usain Bolt die 100 Meter in 4,8 statt in 9,6 Sekunden laufen. Damit Lean in diese Rekordbereiche vorstoßen kann, muss es mehrere Evolutionsstufen durchlaufen:
9,6 SEKUNDEN VOM TOOL-KOFFER ZUM MANAGEMENTANSATZ
Geht man heute durch die Werkshallen deutscher Unternehmen, sind die Spuren des Lean Manufacturing allgegenwärtig. Arbeitsplätze sind nach dem 5S-Prinzip gestaltet, Plakate erinnern an die GPS-Gestaltungsprinzipien und Kanban-Boards dokumentieren aktuelle Ereignisse im Shopfloor. Der tiefere Blick in die Fabriken zeigt allerdings ein sehr viel heterogeneres Bild und nach wie vor zahlreiche Defizite:
So sind Produktionssysteme in der Theorie zwar oft sehr gut beschrieben. In der Praxis jedoch sind die bislang erreichten Effizienzsteigerungen zumeist das Ergebnis isolierter Verbesserungsprojekte und Point-Kaizens, die auf Ebene der klassischen Lean-Werkzeuge wie Materialsteuerungskonzepte, Kanban oder Gruppenarbeit angesiedelt sind. Dahinter steht meist ein falsches Verständnis von Lean als Toolbox, das zur kurzfristigen Realisierung bestimmter Kosten- oder Qualitätsziele eingesetzt wird.
Die Folge: Lean-Initiativen bleiben häufig in der Pilot-Phase stecken oder werden nach dem Erreichen des jeweiligen KPI-Ziels nicht konsequent weiterentwickelt. Da sich gleichzeitig allerdings die Anforderungen des Marktes rasant weiterentwickeln, etwa in Richtung individualisierter Produkte oder kürzerer Lead-Time, verpufft die Wirkung dieser einmaligen und statischen Lean-Initiativen meist, ohne eine nachhaltige Wirkung zu entfalten – zumal sie meist beschränkt sind auf einzelne Linien oder Arbeitsbereiche wie etwa die Montage.
8 SEKUNDEN VON DER WERTSTROM- ZUR GESCHÄFTSMODELLPERSPEKTIVE
Doch Wertschöpfung beginnt nicht erst in der Produktion. Und vor allem endet sie nicht dort. Das gilt umso mehr für smarte Produkte und Komponenten, die in der Lage sind, während ihres gesamten Lebenszyklus vom Herstellprozess bis hin zum Einsatz beim Endkunden Daten zu sammeln und zu kommunizieren. Lean muss dieser Entwicklung Rechnung tragen. Zum einem, indem es auch die indirekten Bereiche wie Logistik oder Instandhaltung in das Wertstromdesign einbezieht. Zum anderen, indem Wertstromanalysen neben dem Material- auch den Informationsfluss und die eingesetzten IT-Systeme einbeziehen, um informationstechnische Verschwendung zu erkennen und später abschalten zu können.
Gleichzeitig muss sich diese ganzheitliche Betrachtungsweise auch im Zielbild widerspiegeln. Statt also auf Kennzahlenebene, z.B. bei der Reduzierung der Durchlaufzeiten oder Ausfallzeiten, anzusetzen, müssen Lean-Initiativen danach fragen, wo sich die Geschäftsprozesse hin entwickeln. Wo liegen die Herausforderungen des Marktes? Muss ich schneller werden? Muss ich in Richtung Qualität eine Stufe höher? Ist das Thema Lieferflexibilität vielleicht wichtiger als Produktivität? Damit rückt das Lean Management automatisch näher an die Unternehmens- und Produktionsstrategie heran – weg von Lean als Werkzeug zur KPI-Optimierung hin zu einem strategischen Werttreiber.
Die Überführung dieser übergeordneten Zielbilder in konkrete Handlungen und Verhaltensweisen am Ort der Wertschöpfung und deren nachhaltige Verankerung zählt nach wie vor zu den größten Herausforderungen im Lean Management. Denn je weiter man den vielzitierten „Eisberg“ in Richtung „Lean Culture“ und „Lean Thinking“ hinabtaucht, desto mehr gerät Lean oft zur Philosophie. Tatsächlich jedoch gibt es sehr konkrete Maßnahmen, die dazu beitragen können, eine Kultur der kontinuierlichen Verbesserung im Unternehmen dauerhaft zu verankern:
Zum einen den systematischen Aufbau von Lean-Know-how im Shopfloor: Statt Wissen in externen Stabstellen oder Projektteams zu bündeln, sollte dabei durch die Ausbildung von Key Usern und Lean Influencern auf Mitarbeiterund Meisterebene die Lean-Expertise vor Ort dauerhaft gestärkt werden. Entscheidend ist dabei eine gezielte Qualifizierung der Mitarbeiter. Niemand muss 97 Lean-Methoden kennen. Stattdessen sollten Trainings an die tatsächlichen Qualifizierungsbedarfe angepasst werden und am echten Objekt bzw. im laufenden Betrieb erfolgen.
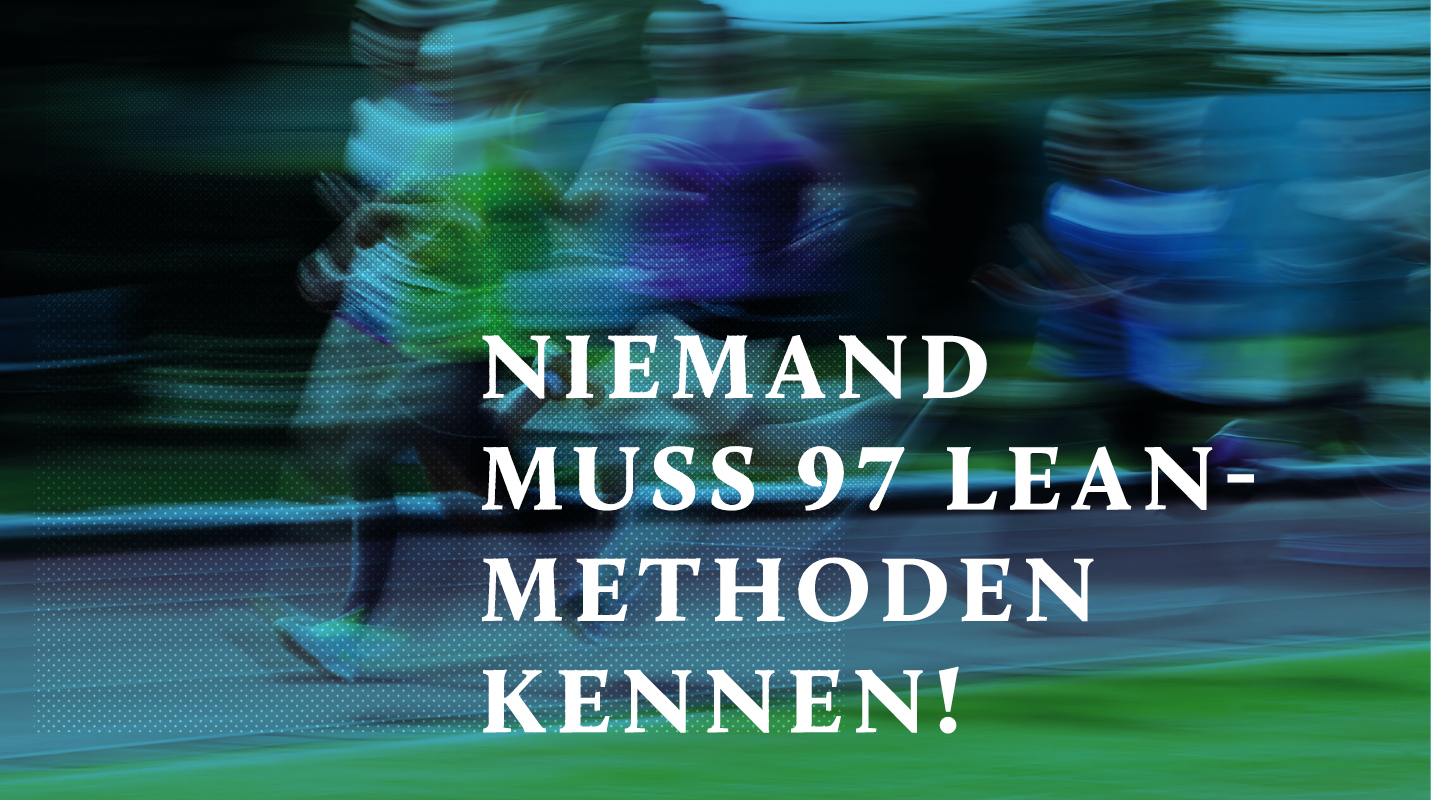
Zum anderen gilt es, abstrakte Zielvorgaben in konkrete Kennzahlen und Prozessparameter zu übersetzen, die für den Mitarbeiter im Shopfloor verständlich und tatsächlich beeinflussbar sind. Die Grundlage dafür bilden Kennzahlenkaskaden, mit denen Soll-Ist-Abweichungen auf allen Unternehmensebenen eindeutig und transparent erfasst werden können. Sie ermöglichen gleichzeitig, Problemlösungsprozesse anzustoßen, die durchaus eine Verbesserungsrichtung (jedoch nicht die Lösung) klar vorgeben und dadurch die Mitarbeiter bei der täglichen Verbesserungsroutine unterstützen. Zentrales Führungsinstrument ist dabei das Shopfloor Management. Richtig umgesetzt, sichert und stabilisiert es nicht nur die operative Steuerung der wertschöpfenden Prozesse über alle Unternehmenshierarchien hinweg, sondern fördert auch fortlaufende Prozessverbesserungen bei gleichzeitiger Entwicklung von Mitarbeitern und deren Problemlösungsfähigkeiten.
6 SEKUNDEN VON KOMPLEXITÄTSREDUKTION ZU KOMPLEXITÄTSAUSLAGERUNG
An dieser Stelle erfolgt eine Zäsur. Denn hier endet der Bereich der konventionellen Optimierungen, die unter Ausschöpfung und ständiger Weiterentwicklung der bekannten Lean-Prinzipien erreicht werden können. Was nun folgt, ist der Eintritt in eine neue Phase des Lean Manufacturing, die zwar auf den gleichen Grundprinzipien beruht, jedoch einen entscheidenden Paradigmenwechsel vornimmt: Wo bei Lean bislang versucht wurde, die Komplexität zu reduzieren, indem man komplexe Systeme und Prozesse in einfache, operativ besser beherrschbare Einheiten zerlegt, ermöglichen digitale Technologien, diese Komplexität auszulagern und vom Benutzer fernzuhalten.
So ersetzen etwa im Rahmen des digitalen Shopfloor Management sensorgestützte Echtzeitdaten und intelligente Apps dezentrale Excel-Lösungen, manuelle Listen und handschriftliche Karten. Gleichzeitig kann durch die Bereitstellung von Echtzeitdaten sowohl die Reaktionsgeschwindigkeit als auch die Fehlerrate im Shopfloor deutlich verbessert werden. Nahezu alle Operationen entlang des Wertstroms lassen sich auf diese Weise digital aufwerten: Ob prädiktive Instandhaltungslösungen, selbststeuernde Logistiksysteme oder Mensch-Maschine-Kollaboration im Rahmen der Arbeitsplatzgestaltung – die Kombination aus Industrie 4.0 und Lean ermöglicht Optimierungspotenziale, die etwa so hoch liegen, wie das, was bislang in dreißig Jahren konventionellem Lean-Manufacturing realisiert wurde. Wirksam werden diese Effekte allerdings nur dann, wenn sie auf den Prinzipien eines schlanken Prozesses aufbauen. Andernfalls nämlich schaffen digitale Technologien neue Komplexität anstatt sie vom Nutzer fernzuhalten. Oder wie es der ehemalige Telefónica CEO Thorsten Dirks einmal so treffend formulierte: „Wenn Sie einen Scheißprozess digitalisieren, dann haben Sie einen scheiß digitalen Prozess.“ Am Ende dieser schrittweisen Lean-Evolution steht die Vision eines vollständig digitalisierten, schlanken Wertstroms, der von der Entwicklung über die Produktion bis hin zur Logistik alle direkt oder indirekt an der Wertschöpfung beteiligten Informations- und Materialflüsse synchronisiert und die darin enthaltenen Informationen nutzbar macht. Ansätze dieser Vision sind schon heute im digitalen Prozesszwilling erkennbar.
Entlang dieses Wertstroms werden sich die einzelnen Prozessschritte immer mehr in Richtung autonomer Systeme verlagern, die Prozessabweichungen nicht nur erkennen, sondern selbstständig Lösungen finden, etwa im Sinne einer präskriptiven Logik. Und hier wird es spannend. Denn da, wo Prozesse sich zunehmend selbst steuern, muss Lean beginnen, bestimmte Grundprinzipien neu zu bewerten. Wie sinnvoll ist etwa ein ziehendes System im Zeitalter prädiktiver Systeme?
Vor diesem Hintergrund müssen Lean-Experten einerseits offen bleiben für neue Technologien und sich andererseits von starren Regeln und Methoden lösen. Stattdessen geht es darum, im Sinne des Lean-Gedankens Experimente zuzulassen und darüber neue Prozessoptimierungen zu ermöglichen. Ausgangspunkt ist dabei immer der Kundennutzen, der durch Smart Products und produktnahe Services immer näher an die Entwicklungs- und Herstellungsprozesse heranrückt. Eine Fragestellung für ein solches Experiment kann etwa lauten, wie individuelle Kundenanforderungen ohne zusätzlichen Planungsaufwand an den Arbeitsplätzen realisiert werden können. Und spätestens hier verlässt Lean die Produktion und wird zu einem unternehmensübergreifenden Managementansatz.
DAS RENNEN IST NOCH NICHT VORBEI!
Am Ende angelangt ist Lean damit natürlich nicht. Denn dass ein System nicht mehr optimiert werden kann, ist schon vom Prinzip her nicht möglich. Es wird also auch in Zukunft neue Entwicklungsstufen und Bereiche geben, in die Lean dank neuer Technologien vorstoßen kann. Ein Ende der Rekorde ist somit nicht in Sicht.
Usain Bolt kann das egal sein. Er hat seine Spikes mittlerweile an den Nagel gehängt.
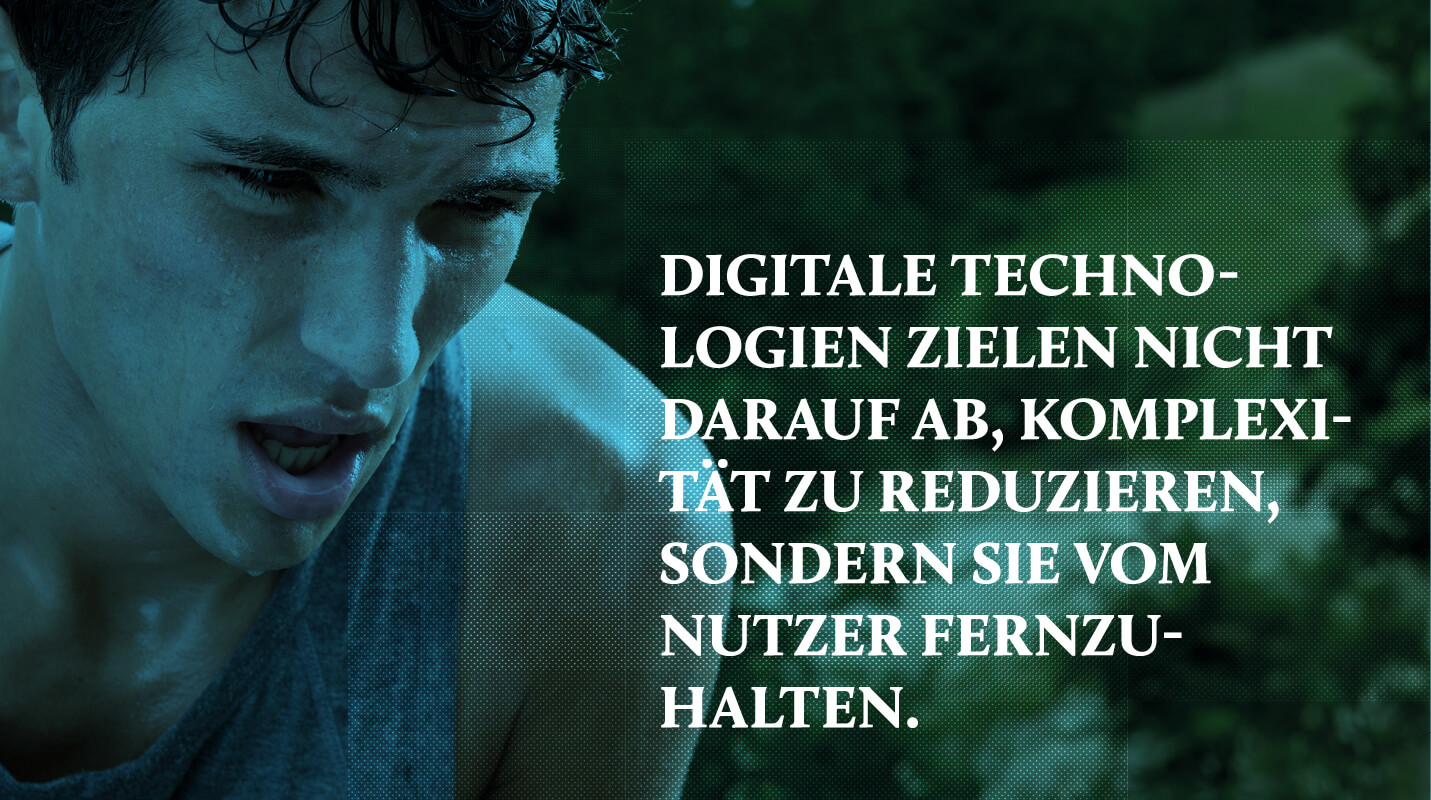
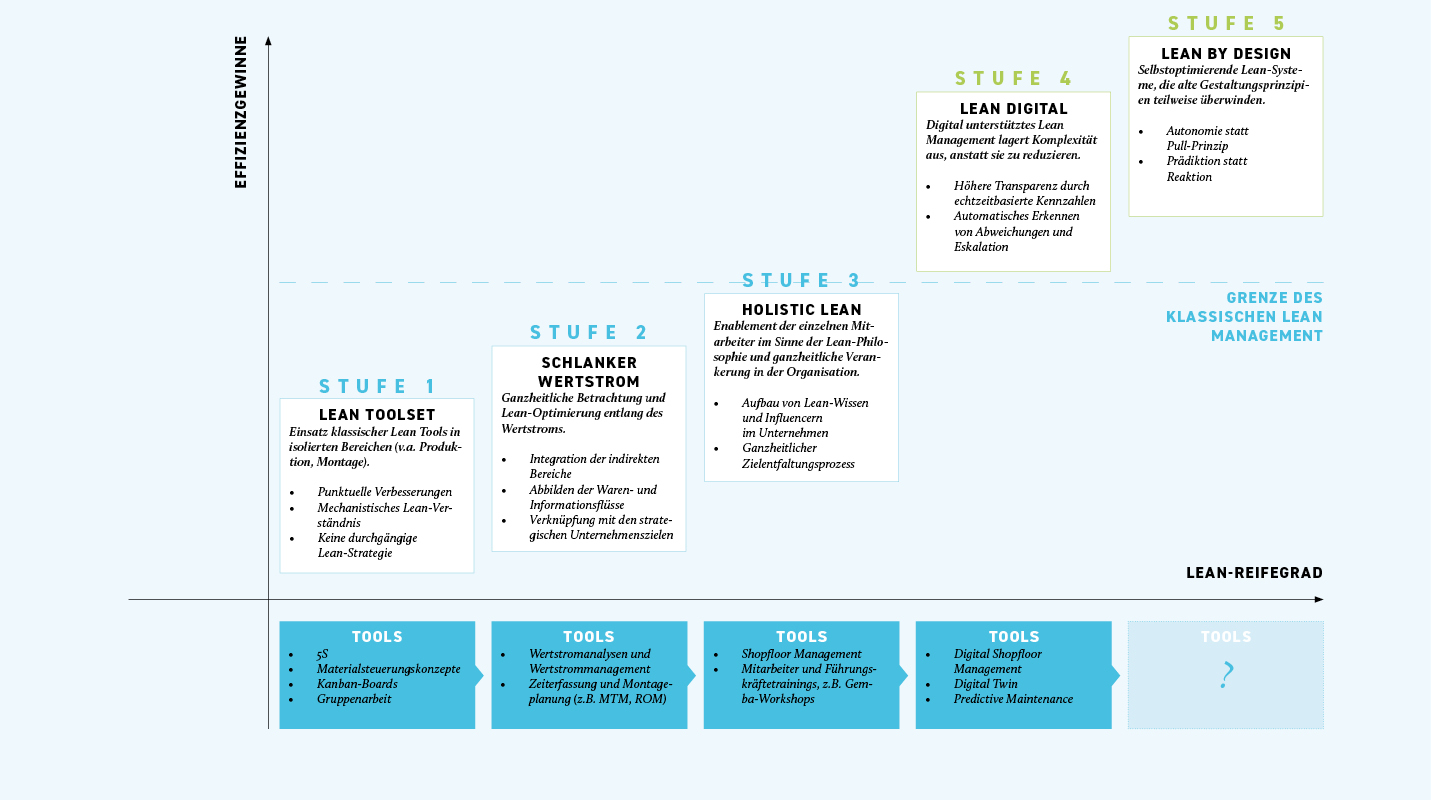
DER WEG ZUR SCHLANKEN PRODUKTION
DIE VORAUSSETZUNGEN FÜR LEAN-PROJEKTE KÖNNEN ÄUSSERST VIELFÄLTIG SEIN. JE NACHDEM, OB EIN UNTERNEHMEN SICH SCHON SEIT JAHREN MIT DEM THEMA BESCHÄFTIGT ODER AUFGRUND DES SCHNELLEN WACHSTUMS DIE WEITERENTWICKLUNG SEINES PRODUKTIONSSYSTEMS KOMPLETT VERNACHLÄSSIGT HAT.
Ob die Maßnahmen einzelne Baureihen eines Produkts betreffen oder den globalen Produktionsverbund eines Unternehmens. Ob Flexibilitätssteigerung und kundenindividuelle Fertigung oder Gesamtanlageneffektivität im Vordergrund stehen. Doch so unterschiedlich die Rahmenbedingungen im Einzelnen sind, gelten i.d.R. gewisse Erfolgsfaktoren, die auf alle Arten von Lean-Projekten übertragbar sind. Dazu zählen neben einer systematischen Zieldefinition in Einklang mit der Unternehmensstrategie beispielsweise die gezielte Qualifizierung von Mitarbeitern sowie die Implementierung von Maßnahmen und Strukturen zur dauerhaften Verankerung der Lean-Prinzipien in der Gesamtorganisation. Aus diesen übergreifenden Gestaltungsprinzipien lässt sich ein Vorgehensmodell zur Einführung schlanker Produktionssysteme ableiten, das als Blaupause für alle Arten von Lean-Projekten herangezogen werden kann.
MODUL 1: DIAGNOSE, BENCHMARKING UND POTENZIALERMITTLUNG (CURRENT STATE)
Inseln der Effizienz
Als der Lean-Production-Ansatz in den 1990er Jahren nach Europa kam, war er eng verbunden mit dem Instrument der „Point Kaizens“. Die Idee dahinter war simpel: Statt eine aufwendige Neukonfiguration des Produktionssystems vorzunehmen, sollten zunächst über vereinzelte Optimierungsmaßnahmen in klar abgegrenzten Bereichen schnelle Lean-Erfolge erzielt werden, die sich anschließend zu einem Gesamtsystem zusammenfügen. Die erhofften Effekte blieben jedoch weitgehend aus. Denn die optimierten Bereiche konnten zwar im Kleinen durchaus Erfolge vorweisen. Ohne Anbindung an den übrigen Wertstrom verpufften diese jedoch, weil etwa vorgelagerte Arbeitsplätze nicht im gleichen Zyklus arbeiteten und dadurch Stillstände am nachgelagerten Arbeitsplatz verursachten. Es entstanden Inseln der Effizienz – in einem Meer der Verschwendung.
Die Einführung der schlanken Produktion auf Basis von Point Kaizens ist daher heute weitgehend abgelöst von einem systematischeren Ansatz, der nicht auf Arbeitsgruppen-, sondern auf Wertstrom- bzw. Organisationsebene ansetzt. Folgt man dieser systematischen Vorgehensweise, beginnt ein Lean-Projekt zunächst mit einer umfassenden Analyse des bestehenden Produktionssystems. Dies umfasst drei zentrale Elemente:
Ermittlung des Lean-Reifegrads
Über standardisierte Assessments und Methoden-Scans wird zunächst der Lean-Reifegrad einer Organisation ermittelt. Neben dem klassischen Prozessdesign und den eingesetzten Methoden in der Produktion bewertet dieser auch die indirekten Bereiche wie etwa Einkauf, Entwicklung, Instandhaltung oder Shopfloor Management. Darüber hinaus wird auch die „Lean Capability“, also die Fähigkeit zur Veränderung auf Ebene des Managements, etwa in Bezug auf Attention, Mindset, Zielsysteme oder die Qualität der Führungskräfte auf den unteren Ebenen, überprüft. Hieraus ergibt sich ein erstes qualitatives Bild zur Beantwortung der Frage: Wo stehen wir und wie weit sind wir eigentlich von Best Practice weg?
Quantitative Potenzialableitung
Auf Basis dieser qualitativen Betrachtung der eigenen Systeme lässt sich anschließend mithilfe standardisierter Berechnungsmethoden das technische und betriebswirtschaftliche Potenzial der möglichen Lean-Maßnahmen ableiten. Insbesondere Letzteres ist entscheidend, um die notwendige Attention für die Maßnahmen auf Management-Ebene zu erzeugen und die notwendige Rückendeckung aus der Managementebene für die nachgelagerten Umsetzungsstufen zu sichern.
Externe Benchmarks
Neben der internen Potenzialermittlung helfen auch externe Benchmarks dabei, das wirtschaftliche Potenzial von Lean-Maßnahmen zu bewerten. Sie liefern zudem wichtige Hinweise für die Auswahl und Ausgestaltung der eingesetzten Werkzeuge und sparen durch die Übernahme von Best Practices Zeit in der Konzeptionsphase.
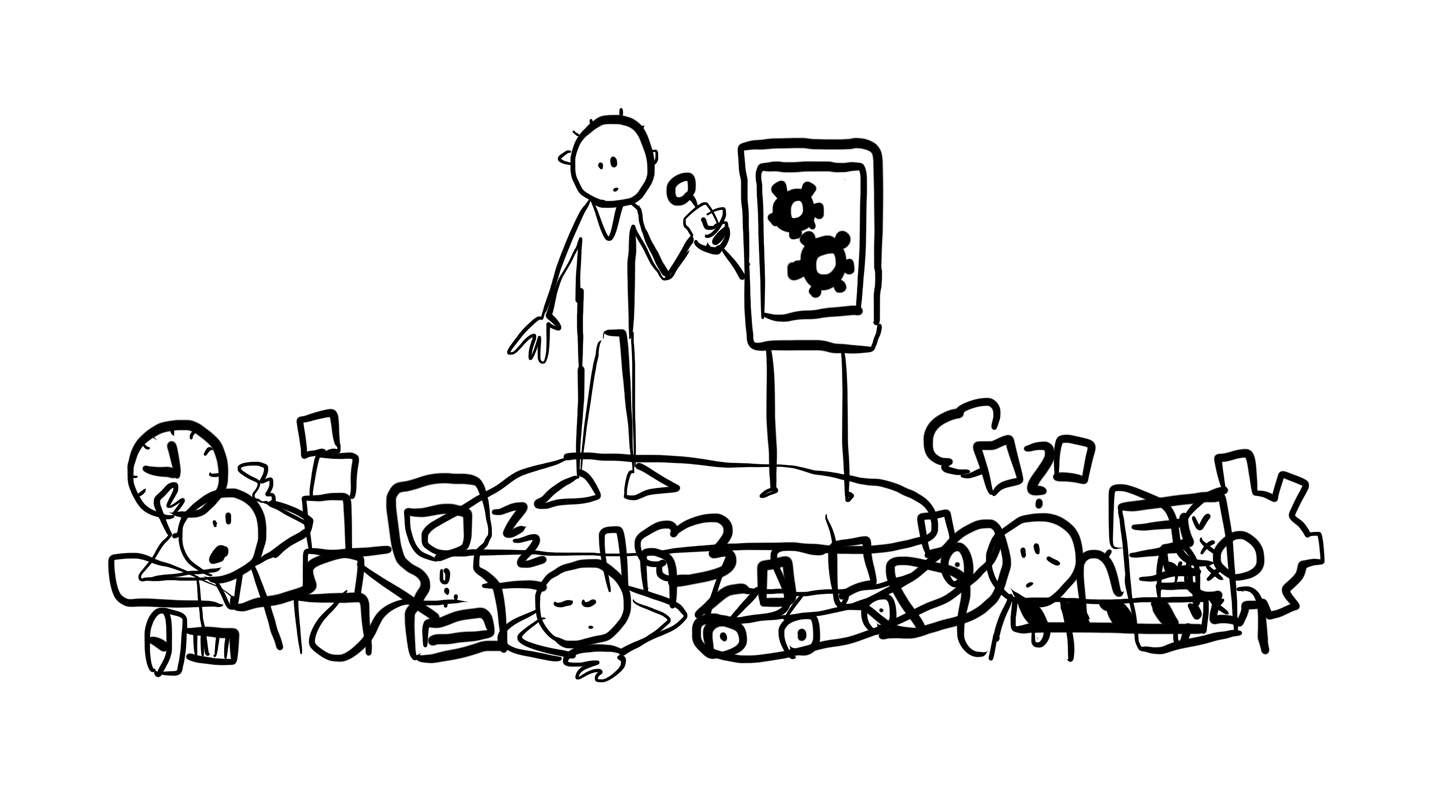