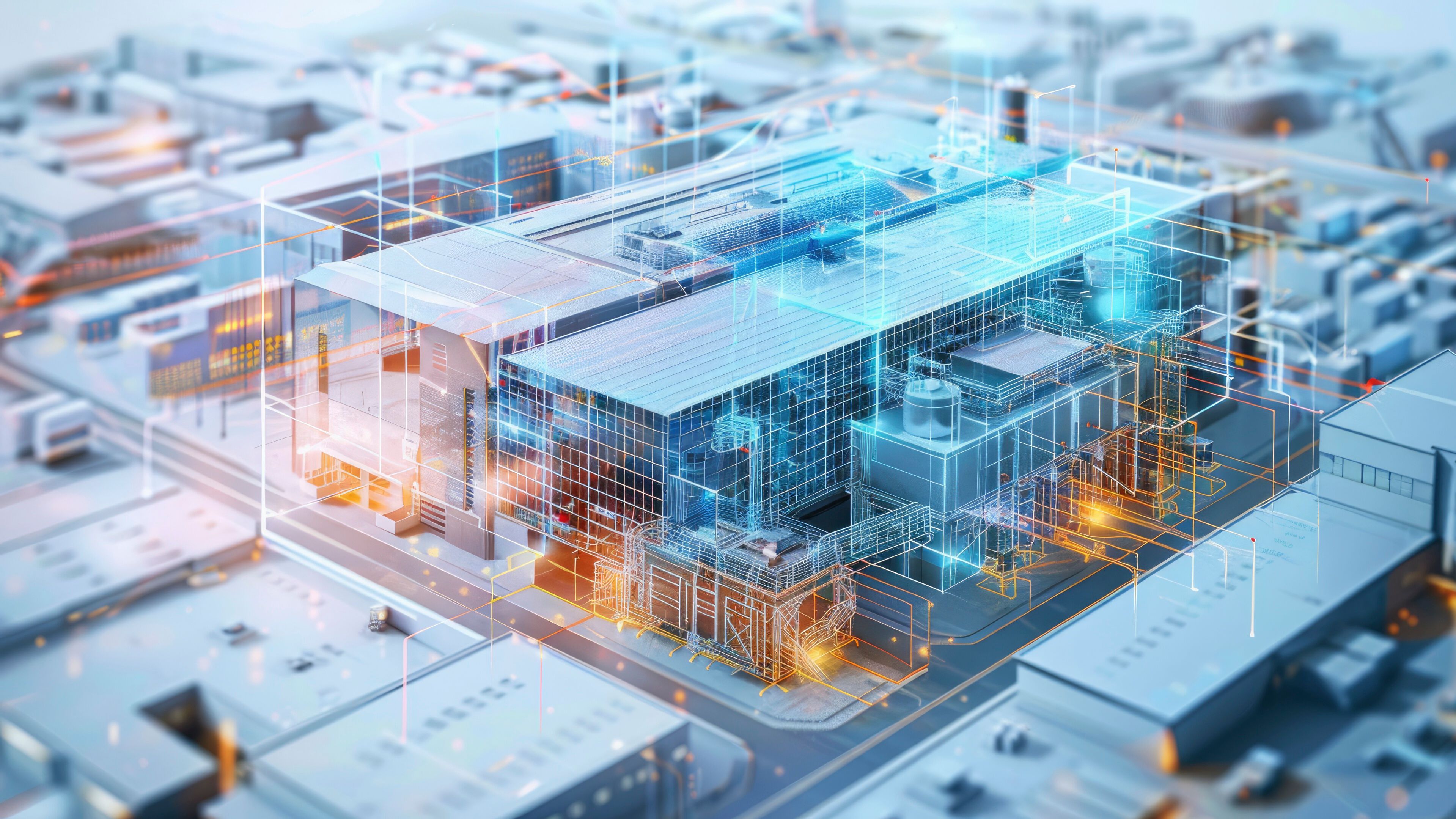
Neustart für die Greenfield-Planung
Ein Hersteller von Elektronikkomponenten stellt die Planung einer mehrstöckigen Fabrik auf den Prüfstand – und schafft in kurzer Zeit die Grundlagen für einen optimalen Produktionsstart
Bei der Erschließung von Zukunftsmärkten ist Zeit erfolgsentscheidend. So auch in diesem Projekt im Nahen Osten, mit dem ein Unternehmen der Elektronikindustrie seine Top-Positionierung in einem noch unerschlossenen Markt absichern will.
Gemeinsam mit EFESO stellt das Unternehmen das bereits erstellte Konzept und Fabriklayout für den Greenfield-Neubau eines Werkes in Frage – jedoch in einem außergewöhnlich knappen Zeitfenster: die Bauarbeiten am Fundament sind bereits im Gange, als das ursprüngliche Planungskonzept modifiziert wird. Mit einem fokussierten Vorgehen und einer Visualisierung der zukünftigen Fabrik in Form eines digitalen Gebäude- und Prozesszwillings gelingt der Neustart der Planungsphase.
Herausforderung
Ein Hersteller von Elektrotechnikrodukten expandiert in einem unerschlossenen Markt im Nahen Osten. Gemeinsam mit EFESO verbessert das Unternehmen ein Konzept und Fabriklayout für den Greenfield-Neubau eines Werkes grundlegend. Dazu steht dem verantwortlichen Task-Force-Team ein sehr geringer Zeitraum zur Verfügung.
MEHREFESO Lösungsansatz
Mit einem „One Stop Shop“-Lösungsansatz erfasst die Task-Force alle Planungsstränge. Zudem visualisiert sie die zukünftige Fabrik in Form eines digitalen Gebäude- und Prozesszwillings und zeigt somit schnell erhebliche Verbesserungspotenziale bei der Raumnutzung, der Gestaltung des Materialflusses und weiteren Aspekten in der Fertigung und internen Logistik auf.
MEHRLessons Learned
Eine sorgfältige Vorbereitung erlaubt es, unter Zeitdruck effektive und klare Entscheidungen treffen zu können. Zudem sollten alle Projektbeteiligten so früh wie möglich in die Arbeit des verantwortlichen, sorgfältig zusammengestellten Projektteams mit einbezogen werden.
MEHREFESO Erfolgsmodell
Der One Stop Shop-Lösungsweg zeigte schnell Verbesserungspotenziale im Fabriklayout des neuen Standortes auf. So konnte das Unternehmen Planungsschieflagen identifizierte und zugleich einen klaren Informationsfluss zwischen allen Projektbeteiligten sicherstellen. Zusätzlich beschleunigte eine Best Practice Tour in europäischen Werken den Wissenstransfer.
MEHRNeuer Werksstandort soll Expansion beschleunigen
Der Bedarf an spezialisierten Elektronikprodukten für Smart City-Einsatzfelder wie die Energieversorgung, Gebäudetechnik und Mobilität nimmt rund um die Welt stetig zu. In diesen und weiteren Märkten befindet sich ein Hersteller von Elektrobauprodukten seit einigen Jahren auf Expansionskurs: mit rund 10.000 Mitarbeitern ist das Unternehmen bereits im Nahen Osten, Asien, Afrikas und Europa präsent. Aufgrund der steigenden Nachfrage nach Niedrig-/Hochspannungssystemen, Ladetechnologien für die E-Mobilität und weiteren Elektrotechniklösungen erweitert das Unternehmen seinen Werksverbund um einen Standort im Nahen Osten.
Mit dem Greenfield-Projekt errichtet es ein neues, mehrstöckiges Fabrikgebäude inkl. eines hochautomatisierten Rohwarenlagers in einer Industriestadt. Die Grundfläche der gesamten Fabrik sollte ursprünglich 45.000 Quadratmeter auf drei Etagen betragen und mehrere Produktions- und Montageeinrichtungen beherbergen; zusätzlich ist ein direkt angeschlossenes, neues Verwaltungsgebäude vorgesehen.
Das Unternehmen entwickelte ein tragfähiges Konzept für das Fabriklayout, welches generelle Bedarfe der Fertigung und Intralogistik angemessen berücksichtigte. Allerdings entdeckte das Management-Team rechtzeitig weitere Optimierungspotenziale in der Layoutplanung. Um im fertiggestellten Gebäude jegliche Flächen so effizient wie möglich für eine hochflexible Fertigung nutzen zu können, beauftragte das Management eine „Task-Force“ von EFESO mit einer umfassenden Prüfung aller Planungselemente zur Gebäude- und Infrastruktur sowie zu den realisierbaren Betriebs- und Logistikprozessen. Zwei Rahmenbedingungen setzten in diesem Fall die Messlatte für den Projekterfolg besonders hoch:
- Zeitdruck: Im Oktober verschaffte sich die Task-Force den ersten Eindruck vom Status Quo vor Ort – doch der Termin für den Beginn der Bauarbeiten war für den Januar des Folgejahres fix vorgegeben. Das Projekt startete, während die Baugrube bereits ausgehoben wurde. Entsprechend knapp fiel der Zeitraum für Veränderungen am Konzept aus. Zum Vergleich: ein bereits eng kalkuliertes Zeitfenster in ähnlichen Projekten liegt bei sechs bis zehn Monaten, im Durchschnitt sind zehn bis zwölf Monate üblich.
- Produktionsstart auf TOP-Level: Im Gegensatz zu den zeitlichen Vorgaben waren die Kosten kein limitierender Faktor. Um mit dem „Besten vom Besten“ bei der Arbeitsplatzgestaltung und der technologischen Ausrüstung zu starten, legte der Elektronikhersteller viel Wert auf einen schnellen Know-how-Transfer aus vergleichbaren, globalen Best Practice Projekten.
Genau diese Expertise für eine erfolgreiche Projektverwirklichung – von der Konzeptionsphase bis zur Umsetzung optimaler Operationsprozesse im neu entstandenen Werk – brachte das EFESO-Team mit ein.
In nur vier Monaten muss die Task-Force klare Strukturen und Vorgaben zur Verbesserung des Konzeptes schaffen.
„One Stop Shop“-Lösung erfasst alle Planungsstränge
Zum Projektstart erweiterte sich die Task-Force auf insgesamt ca. zwölf Personen: den Produktions-, Logistik- und Gebäudeexperten von EFESO standen nun die entsprechend verantwortlichen Mitarbeiter aus den Funktionsbereichen des Unternehmens zur Seite. Die Arbeitspakete bzw. Zielvorgaben für dieses Team lauteten:
- Analyse und Bewertung des bestehenden Konzepts einschließlich der aktuellen Arbeitsabläufe, des Materialhandlings und des Gebäudekonzepts;
- Überprüfung und Identifizierung von Planungsinkongruenzen zwischen verschiedenen Wertströmen;
- Ausarbeitung und Bewertung von Verbesserungsalternativen mit den Schwerpunkten Raumnutzung, Kostenauswirkungen und Prozessverbesserung;
- Erstellung des Produktionskonzeptes und Fabriklayouts sowie Definition der exakten Fabrikanforderungen;
- Identifikation der idealen Lagersysteme und Materialversorgungskomponenten.
Virtuelle Fabrik zeigt neue Spielräume auf
Um diese Ziele im vorgegebenen Zeitfenster zu erreichen, musste die Task-Force möglichst frühzeitig ein gemeinsames Verständnis von den räumlichen und gestalterischen Elementen zwischen allen Projektbeteiligten sicherstellen.
Aufgrund der unterschiedlichen und teilweise miteinander gekoppelten Raum- und Prozesseigenschaften visualisierte das Team daher detailliert die zukünftige Fabrik: am Rechner entstand ein digitaler Zwilling des kompletten Fabrikgebäudes inkl. der Ausstattung an den Arbeitsplätzen sowie im Warehouse. Auf dieser Basis konnte das Team alle Planungsszenarien und die Auswirkungen von auch kleinen Veränderungen auf die Arbeitsprozesse im gesamten Fertigungs- und Logistikbereich präzise simulieren. So ermittelte es bereits in dieser frühen Projektphase, dass das Flächenangebot nicht zum vorgegebenen Flächenbedarf für das Produktionsvolumen einer wichtigen Produktgruppe passte. Die Simulation zeigte auf, wie sich der Flächenbedarf von 52.000 auf 45.000 Quadratmeter verringern ließe.
Diese Visualisierung trug maßgeblich dazu bei, dass die Task-Force in einem „One-Stop-Shop“-Ansatz alle Planungsstränge – Gebäude, Verwaltung, Lager- und Logistikkonzept, Produktionsprozesse – aus einer Hand und mit wenigen Schnittstellen analysieren und koordinieren konnte. Besondere Aufmerksamkeit schenkte sie dabei den folgenden drei Handlungssträngen.
Auf 45.000 virtuellen Quadratmetern simulierte das Team u.a. exakte Fertigungs- und Logistikprozesse.
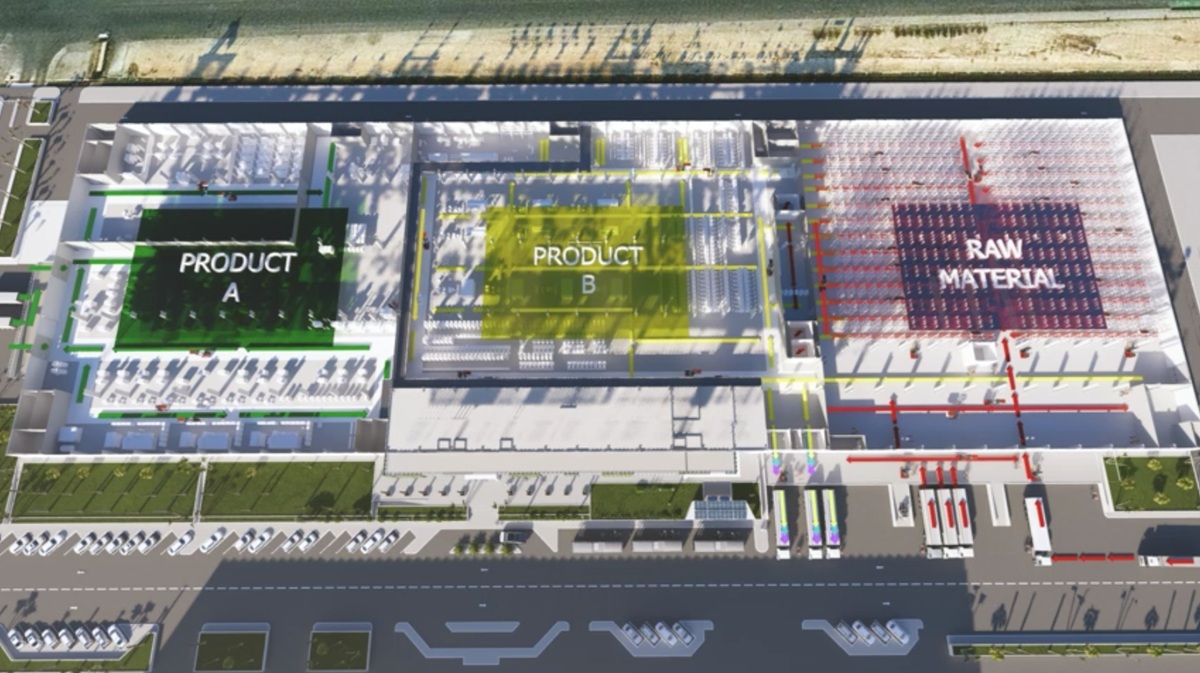
Handlungsstrang 1: Operations Excellence
- Verbesserung des Operations Footprint.
- Identifikation geeigneter Industrie 4.0-Technologien für das Werk.
- Simulation des Materialflusses zur Layout-Optimierung.
- Identifikation zukunftsorientierter Montagekonzepte.
Schwerpunkte in der Simulation späterer Operations-Prozesse:
- Abbildung eines umfassenden Wertstromdesigns.
- Definition eines Intralogistikkonzeptes inkl. zeitgemäßer Ausstattung.
- Darstellung von Schnittstellen in der Fertigung, z.B. bei Behälterkonzeption und Maschinenlayoutanpassung.
Handlungsstrang 2: Building Excellence
- Erstellung energieeffizienter MEP (Mechanical, Electrical and Plumbing)-Konzepte.
- Konzeption eines nachhaltigen Gebäudes im Einklang mit den ESG-Anforderungen.
- Entwicklung eines flexiblen und modularen Gebäudelayouts.
- Fokussierung auf CapEx (Capital Expenditure)-optimierte Lösungen.
Schwerpunkte in der Simulation späterer Operations-Prozesse:
- Anforderungen an das Gebäude, etwa zu Bodenplatten, Sprinkleranlagen etc.
- Anforderungen an die Infrastruktur.
- Eigenschaften / Belastbarkeit des Stromnetzes.
- Berücksichtigung von Vorgaben bei Energieeffizienz und Nachhaltigkeit
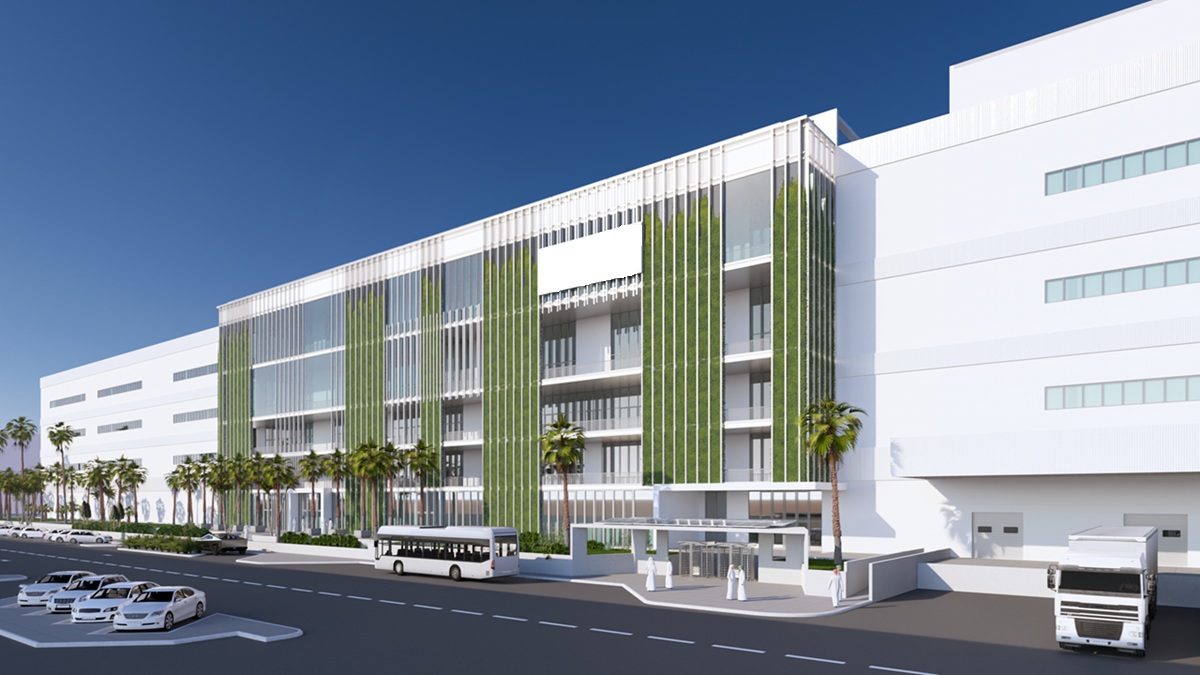
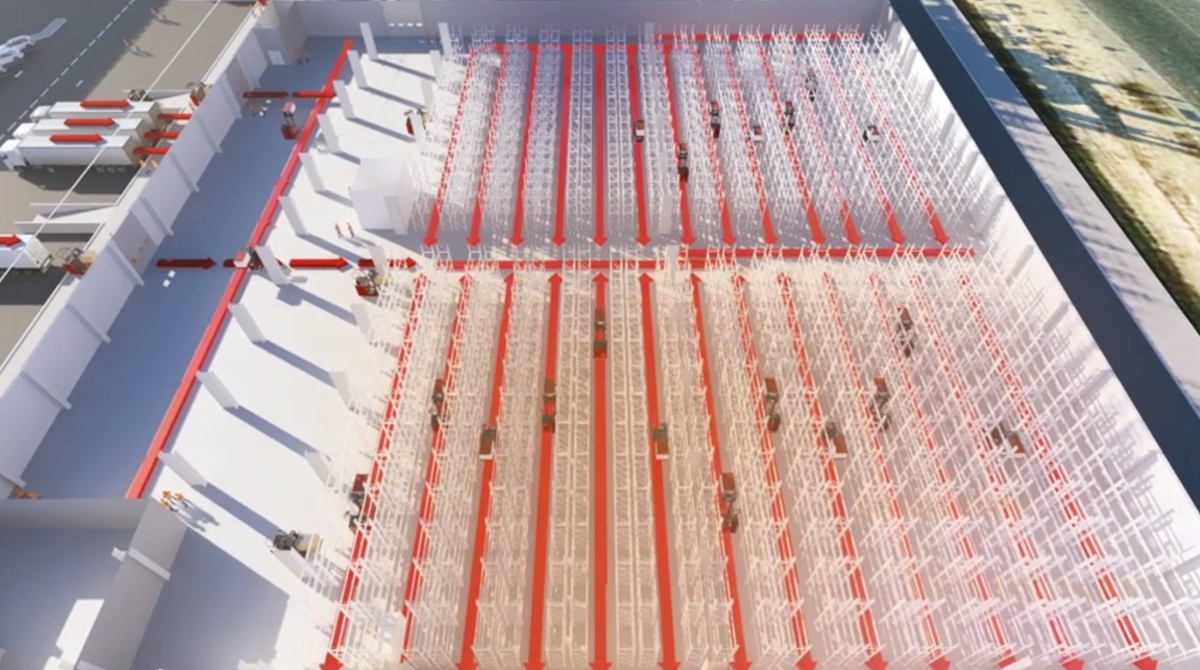
Handlungsstrang 3: Warehouse Excellence
- Identifikation bedarfsgerechter und CapEx-optimierter Lagertechnik.
- Entwicklung eines hybriden Materialverteilungssystems für hohe Flexibilität bei Veränderungen.
- Integration dieser Punkte in das Produktionskonzept.
Schwerpunkte in der Simulation späterer Operations-Prozesse:
- Visualisierung des Logistikkonzeptes und der Technologieauswahl.
- Darstellung und Prüfung der Anforderungen an die Infrastruktur.
- Darstellung der Schnittstellen zwischen Gebäude, Infrastruktur und Produktion.
Schnelles und effektives Handeln dank gründlicher Vorbereitung
Bei der Umsetzung des Projektes erwiesen sich die folgenden Aspekte als erfolgsentscheidend:
Befähige das Projektmanagement, klare Entscheidungen zu treffen – vom ersten Tag an!
Effektive Entscheidungen zu treffen, insbesondere unter Zeitdruck, erfordert eine sorgfältige Vorbereitung und die Fähigkeit, schnell konsistente und umfassende Informationen zu verarbeiten. Dies sollte mit einer fundierten Informations- und Datenanalyse unterstützt bzw. ermöglicht werden. Hier ist eine Skizzierung von Szenarien hilfreich, da sie die Auseinandersetzung vom Abstrakten ins Konkrete verlagert. Ebenso sind klare Prioritäten und Entscheidungskriterien zu formulieren, um schnell und zielgerichtet agieren zu können.
Caste das ideale Team!
Selbst bei einem sehr ambitionierten Zeitrahmen sollte man keine Zeit damit sparen, das richtige Team aus erfahrenen Fachleuten für das Projekt zusammenzustellen. Ein gut gecastetes Team kann schnell auf unerwartete Herausforderungen reagieren, kreative Lösungen entwickeln und sicherstellen, dass Projekte oder Problembereiche effizient und erfolgreich gemeistert werden.
Hole alle Stakeholder mit ins Boot!
Alle Projektbeteiligten sollten so früh wie möglich in die Arbeit der Task-Force bzw. des verantwortlichen Projektteams involviert werden. Eine klare Kommunikation und Einbeziehung der relevanten Teams und Stakeholder fördern das Verständnis und die Akzeptanz von Entscheidungen. Dies kann durch regelmäßige Meetings und Updates sowie das Einrichten von Feedback-Schleifen erreicht werden. Die frühzeitige und kontinuierliche Zusammenarbeit mit den relevanten Parteien sichert zudem ab, dass alle an einem Strang ziehen und dieselben Ziele verfolgen.
In drei Best-Practice-Werken in Europa erhalten die Mitarbeiter Ideen für die Fabrikgestaltung.
Wissenstransfer bei Werksbesuchen
Mit dem One Stop Shop-Lösungsweg zeigte die Projekt-Task-Force schnell Verbesserungspotenziale im Fabriklayout des neuen Standortes auf. Sie identifizierte Planungsschieflagen und stellte zugleich als alleiniger „Point of Coordination“ einen klaren Informationsfluss zwischen allen Projektbeteiligten sicher. Dieses Vorgehen verhinderte Diskrepanzen im weiteren Bauprojekt, die zu Ineffizienz oder höheren Kosten geführt hätten.
Ein weiterer positiver Effekt für die Weiterführung des Projektes über die Planungsphase hinaus ergab sich daraus, dass die Task-Force bei einer „Best Practice Tour“ in wenigen Tagen drei Werke in Europa besuchte. Dort erlebten die Mitarbeiter des Elektronikherstellers mustergültige Produktions- und Logistikabläufe in der Praxis.