AUF DEM WEG ZUR „SCREENTIME ZERO“
Als Tochtergesellschaft von Pepperl+Fuchs, einem Hersteller von Automatisierungstechnologien, entwickeln wir Industrie-4.0-Lösungen für die Intralogistik mittelständischer Unternehmen. In diesem Fall beauftragte uns ein Automobilzulieferer, die Zulieferung bzw. Bereitstellung von Teilen an seine Produktionslinien möglichst „schlank“ zu gestalten. Das Ziel: „Screentime Zero“ – kein Werker sollte sich mehr an einem Rechner einloggen müssen, um Teilebuchungen vorzunehmen.
Das Unternehmen entschied sich dafür, seine bereits mittels Kanban organisierten Bestände und Regale in Zwischenlagern zu digitalisieren. Zu diesem Zweck sollten die Prozesse analysiert und optimiert werden und eine Komplettlösung entstehen, die sich auch in andere, bereits vorhandene Produktions- bzw. Intralogistikumgebungen integrieren lässt.
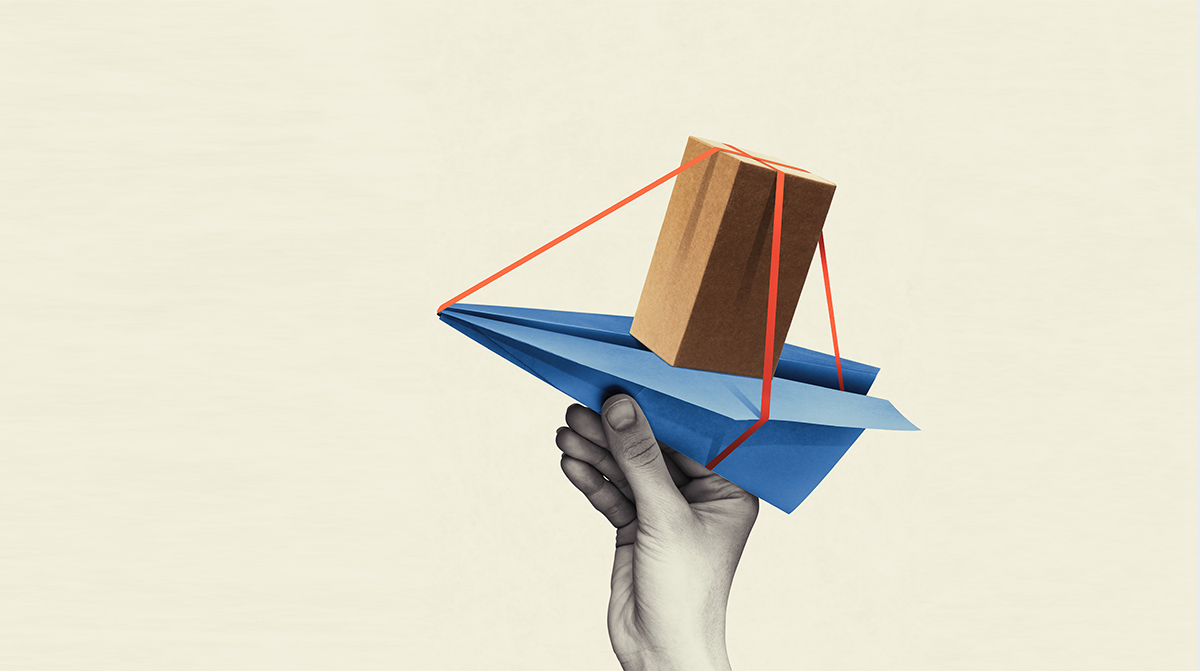
Smarte Regale: Materialbewegungen erkennen und intelligent verarbeiten
Um diese Aufgabenstellung zu lösen, kombinierten wir drei Technologien zu einer maßgeschneiderten IIoT-Lösung: Neben RFID-Systemen zur Identifikation von Behältern und Material nutzt diese Lösung speziell für Kanban-Regale entwickelte Sensorleisten zur exakten Lokalisierung und Erkennung von Materialbewegungen in Regalen. Die dabei gewonnen Daten werden mit einer prozessorientierten Cloud-Software verarbeitet.
In Summe konnten wir so die Kanban-basierte Wertschöpfungskette des Unternehmens vollständig digitalisieren. Dies sorgt nicht nur für transparentere, effizientere Prozesse in den Zwischenlagern, sondern ermöglicht nun die digitale Registrierung und „smarte“ Verarbeitung sämtlicher Materialbewegungen. Im Cloud-seitigen Backend ist zudem jederzeit ein synchrones, digitales Abbild des Regalbestandes erstellbar. Wie die Lösung im Detail funktioniert, veranschaulichen die folgenden Funktionen und Anwendungsbeispiele:
Materialbereitstellung mit auftragsspezifischer Erfassung
In der Produktion sind vier Formen der Bereitstellung üblich: Die klassische Methode ist Kanban, d.h., das Material liegt immer an der Linie und sobald Bedarf entsteht, wird ein Signal an die Quelle im Lager gesendet. Weitere Optionen sind die Just-in-Time-Produktion, die verschärfte Variante Just-In-Time-Sequence sowie schließlich die auftragsbezogene Kommissionierung. Alle vier Formen kann unsere Lösung unterstützen.
Bei sehr großer Variantenvielfalt macht es keinen Sinn, immer alle Materialien am Band zu haben. In diesem Fall bieten wir eine Hybridlösung und kombinieren Kanban mit einer auftragsspezifischen Bereitstellung. Wenn der Werker seine Manufacturing Order scannt, sind Kanban-Materialien vorrätig, aber auch ein Container mit den auftragsspezifischen Komponenten. Für den Logistiker ist das exakt der gleiche Workflow, aber es wird von der Logik im System anders gesteuert. Da die Manufacturing Orders für die nächsten Tage im System hinterlegt sind, lassen sich auch auftragsspezifische Materialien schon in der Linie bereitstellen, die man gewöhnlich erst beim Auftragsstart bereitstellen würde.
Materialzulieferung mit automatisierten Kommissionierungsaufträgen
In jeder Fertigung ist die Materialzulieferung an der Schnittstelle zwischen Lager/Intralogistik und Produktion ein wichtiger Ansatzpunkt für Prozessverbesserungen. Für reibungslose Arbeitsabläufe in der Linie sollte dazu jederzeit das richtige Material im (Kanban-)Zwischenlager zur Verfügung stehen. Fehlende Komponenten müssen sonst manuell im Lager entnommen werden, was bis zu 30 Minuten dauern kann und wertvolle Produktivzeit des Werkers kostet. Mehrmals täglich nötige manuelle Picks senken die Effizienz insgesamt enorm. Solche Situationen lösen wir auf, indem jede Entnahme aus dem Kanban-Regal registriert wird und bei Bedarf die IIoT-Lösung einen Kommissionierungsauftrag im Lager auslöst, ganz ohne Zutun des Mitarbeiters. Das funktioniert über optische Sensorleisten, die in die Regale verbaut sind und jede Materialbewegung tracken.
Materialflusssteuerung mit anonymisieren Containern
Ein weiterer Aspekt ist die Materialflusssteuerung. Viele unserer Kunden arbeiten mit Kanban-Containern, die eine feste Zuordnung auf das Material erhalten. Ist das Material verbraucht, wird genau der Container ins Lager zurückgebracht und wieder mit dem gleichen Material befüllt. Unser Ansatz ist, die Container stattdessen zu anonymisieren, d.h., das kommissionierte Material wird neu mit einem anonymen, leeren Container gleicher Größe gepaart, dem die entsprechende virtuelle Kanban-ID zugeordnet wird. Somit lassen sich Prozesse parallelisieren und Wiederbeschaffungszeiten enorm senken. Abhängig davon, wie weit das Lager von der Linie entfernt ist, kann das eine halbe Stunde bis zu einem halben Tag ausmachen. Durch schnellere Wiederbeschaffung lassen sich außerdem Puffergrößen reduzieren und damit wertvoller Platz in der Produktion einsparen. In unterschiedlichen Anwendungsszenarien konnten unsere Kunden ihre Fertigung somit um bis zu 10% ausdehnen.
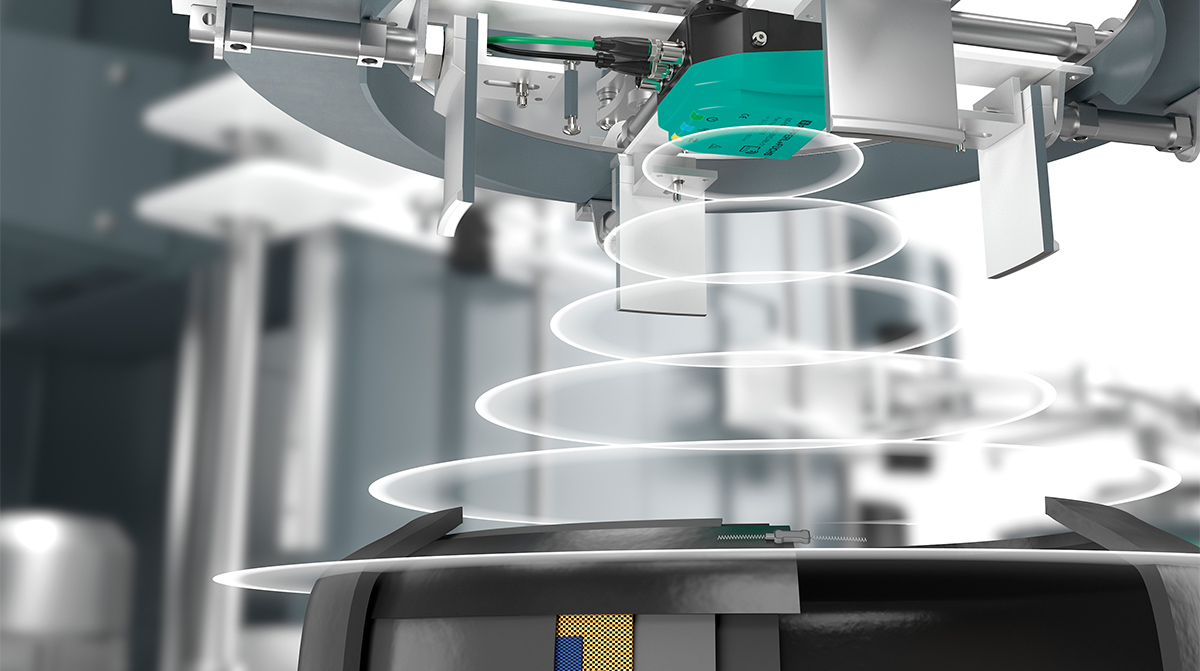
Parallele Versorgungsprozesse reduzieren Kosten
Neben den genannten Aspekten beeinflusst die Lösung auch die Prozessstabilität und die Produktqualität positiv. Dies zeigte sich im Falle eines weiteren Kunden, der hochindividuelle Schaltschränke fertigt, deren Komponenten sich stark ähneln: Um bei der Montage Verwechslungen zu vermeiden, wird dem Werker beim Scannen seiner Manufacturing Order an den Regalfächern per „Pick by Light“ angezeigt, wie viele Elemente er von welcher Sorte picken muss. Um Fehler auf der Put-Seite, wo die Materialien bestückt werden, zu vermeiden, scannt der Logistiker den Behälter. Daraufhin wird ihm die richtige Gasse angezeigt und er fügt die Teile dort ein. Das System verbucht den Behälter wiederum genau an der passenden Position.
Konkrete Ergebnisse aus der Anwendung der IIoT-Lösung sind z.B. eine Verringerung des Working Capital entlang des gesamten Prozesses im Werk von bis zu ca. 20%. Dies wird vor allem durch die durchgängige Materialverfügbarkeit und eine dynamisierbare Materialbereitstellung erreicht. Aber auch der manuelle Aufwand für die Materialsuche reduziert sich um mehrere Minuten pro Produktionsauftrag. Die Durchlaufzeit für die logistischen Materialversorgungsprozesse lässt sich je nach Entfernung zwischen Lager und Produktion um bis zur Hälfte reduzieren. Dies wird vor allem durch nun parallel ablaufende Versorgungsprozesse möglich, da diese automatisiert initiiert werden können. Zudem kann auch der Flächenbedarf für Regale in der Nähe des Montagebereichs um bis zu ca. 20% verringert werden, da das Material verbrauchsorientiert bereitgestellt wird.
In Zukunft sollen weitere Module wie ein „RFID to Cloud“-Service mit der beschriebenen Materialflusssteuerung zu einer umfassenden Intralogistic Solution Suite zusammengefasst werden. RFID-Leseköpfe könnten an beliebigen Stellen innerhalb der Produktion positioniert werden und Geschäftsprozesse triggern. So könnte bspw. ein Transportauftrag vollautomatisiert in SAP quittiert werden, sobald ein Stapler durch ein RFID-Gate fährt. Für eine Umsetzung von „Screentime Zero“ ist also noch weiteres Potenzial vorhanden.
Einsatzfeld: Automatisierungstechnik/Intralogistik
Herausforderung
Digitalisierung der Kanban-basierten Wertschöpfungskette eines Automobilzulieferers mit dem Ziel, die Prozesseffizienz in den Zwischenlagern zu steigern und eine „Screentime Zero“ in den Arbeitsschritten der Mitarbeiter zu erreichen.
Lösung
Erfassung sämtlicher Materialbewegungen mit einer speziell entwickelten Kombination von optischen Sensoren und Identifikationssystemen mit einer Cloud-Software; besseres Management der Intralogistikprozesse im Werk durch eine digitale Visualisierung des Regalbestandes in Echtzeit und die direkte Integration ins ERP-System.