Überlebensfaktor Perfektion
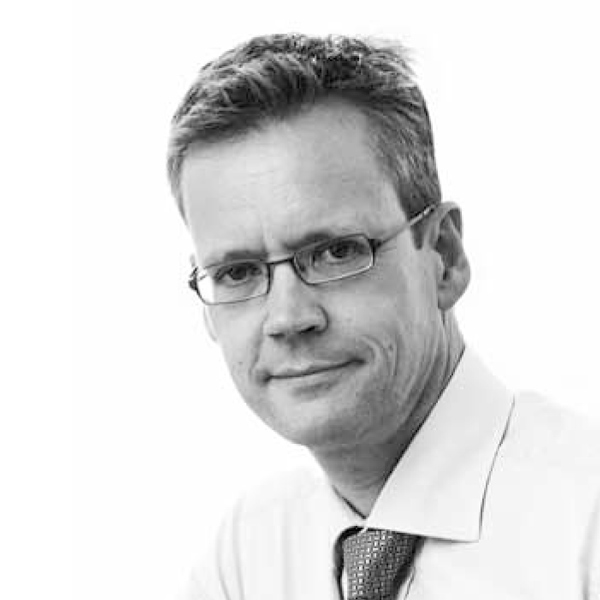
Operative Exzellenz (OPEX) als Motor der Wertsteigerung
Ein profitables, effizient organisiertes Unternehmen gleicht einer hochwertigen Uhr: Bei aller Präzision sind noch immer Verbesserungsmöglichkeiten in der Gestaltung des Uhrwerks vorhanden. Auch Unternehmen müssen ständig nach neuen Ansätzen suchen, mit denen sie ihr Innenleben, also ihre Organisations- und Prozessstrukturen, weiter perfektionieren. Nur so überleben sie in einer fortschreitenden, hochdynamischen Globalisierung.
OPEX zielt auf die kontinuierliche Verbesserung operativer Strukturen und Prozesse im Unternehmen ab – über die gesamte Wertschöpfungskette hinweg.
Ein solcher Weg ist der Ansatz der ‘Operational Excellence‘ oder ‚operativen Exzellenz‘, kurz OPEX. OPEX zielt auf die kontinuierliche Verbesserung operativer Strukturen und Prozesse im Unternehmen ab. Und das nicht nur in einzelnen Teilbereichen, sondern über die gesamte Wertschöpfungskette hinweg. Dabei stehen Effizienz (Aufgaben/Prozesse richtig machen) und Effektivität (die richtigen Aufgaben/Prozesse machen) im Fokus. Bei OPEX geht es jedoch um weit mehr als kurzfristige Gewinnsteigerungen und höhere Mitarbeiterproduktivität. Es geht um das Verständnis, Bestandteil eines Wertschöpfungskreislaufs zu sein und in jeglicher Position fortlaufend zu dessen Evolution beizutragen – sei es über Prozessstabilität, Verbesserungsideen oder ein routiniertes Fehlermanagement. Im Vordergrund steht auch die Motivation, Wissen zu erwerben, zu teilen und über alle Fehlschläge und Erfolge hinweg zu neuer ‘Exzellenz‘ weiterzuentwickeln. Im Idealfall entstehen autonome Wertströme. Und egal, an welcher Stelle der Wertschöpfungskette Brüche oder Verbesserungspotenziale auftreten, schließen bzw. nutzen die zuständigen Mitarbeiter diese direkt und ohne Intervention des Managements. Klingt zu schön, um wahr zu sein? Tatsächlich gibt es einige Gründe dafür, dass sich die meisten Unternehmen operative Exzellenz zwar wünschen, doch nur die wenigsten sie in der Praxis umsetzen.
OPEX als Lean-Erweiterung
Aufgrund von Gemeinsamkeiten zwischen OPEX und Lean Management Ansätzen werden die Begriffe oft gleichgesetzt. Tatsächlich unterscheiden sie sich aber. Das fängt bei der jeweiligen Philosophie an und zeigt sich vor allem in der praktischen Umsetzung. ‚Lean‘ bzw. die Forderung nach ‚schlanken Prozessen‘ war einst das Credo der Effizienzsteigerung in der Fertigung. Heute assoziieren Unternehmen damit zuweilen Projektkonzepte, die nach der ‚Rasenmähermethode‘ arbeiten (zum Beispiel nur auf Kostensenkungen fixiert sind) und die nicht die individuellen Branchenanforderungen berücksichtigen. Oftmals führt auch die krampfhafte 1:1 Übernahme von Lean-Konzepten aus der Produktion in ungeeignete Tätigkeitsbereiche zu mageren Resultaten. Dies liegt aber weniger an den Lean- Prinzipien als an einer mangelhaften Umsetzung. Tatsächlich bieten Lean-Prinzipien oft eine gute Ausgangsbasis, um mit OPEX substanzielle Verbesserungen zu erreichen. Denn OPEX erweitert Lean sinnvoll. Nicht nur, weil der Begriff wertfreier, philosophisch unbelasteter und damit leichter in ganz unterschiedliche Anwendungsfelder transportierbar ist. Der entscheidende Vorteil ist der größere Methoden-Baukasten. Er enthält Lösungen für Unternehmen aller Branchen, die unter steigendem Kostendruck,überlasteten Kapazitäten oder mangelhaftem Know-how-Transfer leiden – seien es Fertigungsunternehmen, Finanzdienstleister oder öffentliche Institutionen.
Das branchenübergreifende Plus von OPEX ist eben keine Effektivitätssteigerung durch gnadenloses ‚Cost-Cutting‘. Kosten sollen zwar auf ein vernünftiges, marktgerechtes Niveau sinken und dort langfristig gehalten werden. Sie sind aber nur einer von vielen weiteren Ansatzpunkten im Unternehmen, ohne dass es dazu Endpunkte im Sinne eines ‚Projektabschlusses‘ gibt. Natürlich misst man die Ergebnisse von OPEX-Maßnahmen auch an harten Kennzahlen wie Umsatzrenditen oder Kundenreklamationen. Der zentrale Unterschied zu Ansätzen wie Lean liegt jedoch im Anspruch, die gesamte Wertschöpfungskette permanent zu verbessern. Das führt letztendlich auch zu einer zeitgemäßen perspektivischen Erweiterung: In hochvolatilen Märkten und bei unvorhersehbaren Ereignissen, die die Wirtschaftssysteme im Wochen- oder sogar Tagesrhythmus in neue Richtungen driften lassen, greifen Fünf- Jahres-Strategien schlichtweg nicht mehr.
Vier Ansatzpunkte für operative Exzellenz
Bei der erfolgreichen Implementierung von OPEX hilft es zu verstehen, dass man OPEX nicht verordnen kann. Wie bei allen tiefgreifenden Veränderungen ist es einfach, dem Anspruch ständiger Verbesserung und Fehlervermeidung zuzustimmen – aber schwierig, dies auch tatsächlich zu tun. OPEX ist eine Einstellungssache, weswegen sich ein OPEX-Ansatz in der Umsetzung auf vier Erfolgsfaktoren konzentrieren sollte:
• Management Commitment auf allen Hierarchieebenen
• Integration der Mitarbeiter
• Ergebnisorientierter Expertenaustausch
• Maßgeschneiderte Tools
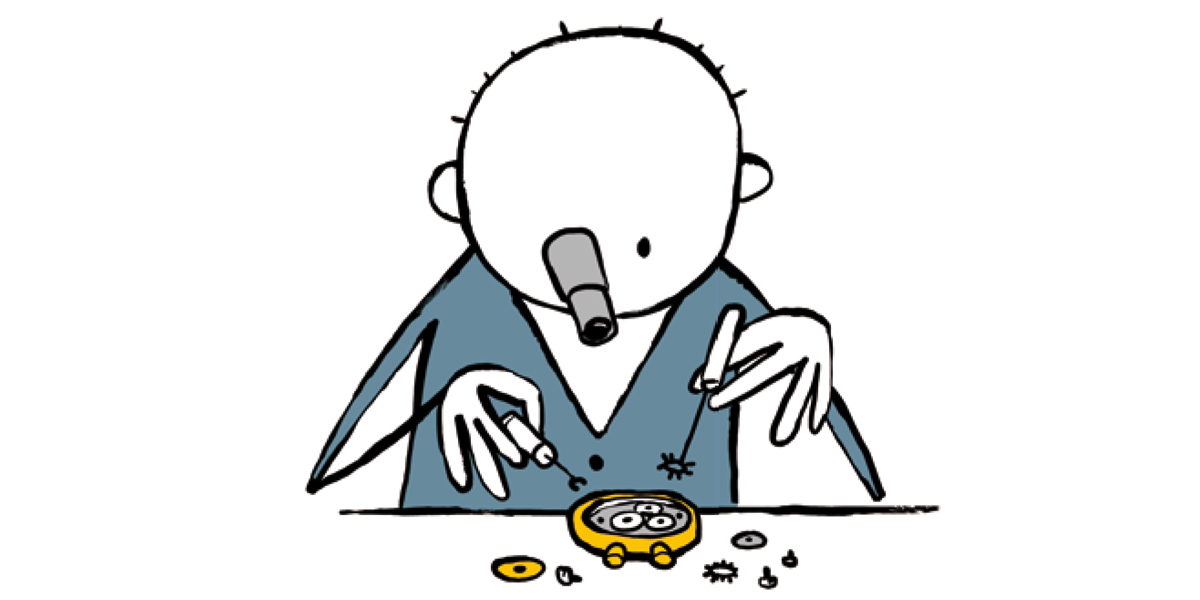
Das Top-Management sollte in der Kommunikation und im Handeln zeigen, dass es zu 100 Prozent hinter OPEX steht. Es beobachtet außerdem, ob alle Führungsebenen den eingeschlagenen Kurs Top-Down mittragen und scheut keine Konfrontation, falls dem nicht so ist. Schließlich gilt auch für die OPEX-Umsetzung, dass bei der Realisierung von Verbesserungschancen und der Fehlerbehebung keine Zeit zu verschwenden ist.
Bei der erfolgreichen Implementierung von OPEX hilft es zu verstehen, dass man OPEX nicht verordnen kann.
Alle Führungskräfte sollten daher klare Ziele vorgeben, sich regelmäßig vergewissern, ob diese auch verstanden wurden und – Erfolge ebenso wie Fehler – klar und unmittelbar kommunizieren.
Integration der Mitarbeiter
Die Lern- und Veränderungsbereitschaft der Mitarbeiter für OPEX sollte vom ersten Tag an gefördert werden. Denn fast jeder Mitarbeiter kann aus dem Stand Missstände oder Verbesserungspotenziale benennen. Leider sind die gängigen Erfahrungsmuster, dass genau dies unerwünscht ist bzw. ohne nennenswerte Konsequenzen ‚verpufft‘. Führungskräfte sollten also immer die enge Verbindung der kulturellen und strukturellen Ebene im Auge behalten und dabei den abteilungsund unternehmensübergreifenden Austausch suchen. Wie lässt sich die Produktqualität bei gleichzeitig fallenden Qualitätskosten nachhaltig steigern? Warum macht das eine andere Fachabteilung, ein Auslandsstandort, ein Konkurrent oder ein Zulieferer besser?
Ergebnisorientierter Expertenaustausch
Methodisch bewähren sich dafür immer wieder Best-Practice-Programme, in denen einzelne Mitarbeiter in Experten-Rollen den Know-how- Austausch über Unternehmensund Ländergrenzen hinweg fördern. Experten können auch externe Berater mit speziellem Know-how sein, das nur zeitlich begrenzt in einem einzelnen Projektabschnitt benötigt wird. Und last but not least sind die Kunden die vielleicht wichtigsten Experten, die über Reklamationen oder das ‚Pull- Prinzip‘ einen direkten Einfluss auf Prozessverbesserungen ausüben sollten. Streng genommen ist also jeder Mitarbeiter und Kunde ein Experte für seine jeweilige Aufgabe – in der Hektik des operativen Alltages geht es folglich darum, den Informationsfluss all dieser ‚Expertisen‘ produktiv zum Zirkulieren zu bringen.
Maßgeschneiderte Tools
Den richtigen Schliff erfahren die gewählten Maßnahmen mit den passenden Tools, vor allem zur Strukturierung und Visualisierung des Informationsaustausches. Ein sehr einfaches und sinnvolles Struktur-Tool ist die tägliche, fünf- bis zehnminütige Absprache zur Performance. Hier sollte man ein gemeinsames Verständnis zu Zielen sicherstellen, konkrete Roadmaps aufstellen aber auch Raum für Ideen und Verbesserungsvorschläge schaffen. Zur Visualisierung von OPEXrelevanten Informationen eignen sich zum Beispiel in der Fertigung Schautafeln mit Kennziffern, die sich auf zeitliche Indikatoren und den Wertfluss konzentrieren.
Alle OPEX-Facetten nutzen
Wer einzelne Fer tigungsabschnitte, Prozessabläufe seiner Supply Chain oder Kreationsphasen in der Entwicklung bis auf das kleinste Effizienz- Stellschräubchen analysiert, hat bereits einen meilenweiten Vorsprung vor Wettbewerben, die diese Prozesse noch mehr oder weniger dem Zufall überlassen. Wer den Zusammenhang zwischen diesen Elementen sieht und diesen für ständige Verbesserungen nutzt, lebt bereits eine operative Exzellenz. Doch OPEX-Profis schaffen sogar mehr: Sie verändern Bereiche, die unterhalb des Wahrnehmungsradars liegen. Zum Beispiel das Schnittstellenmanagement zwischen einzelnen Funktionsgliedern der Wertschöpfungskette. Das betrifft beispielsweise das Energie- und Ressourcenmanagement. Hier investieren einige Unternehmen heutzutage punktuell viel Geld und Zeit, um ‚stille‘ Verschwendungen in Teilbereichen zu vermeiden. Richtig lohnend ist aber erst der Blick auf das Gesamtbild: Gibt es Abläufe, die für sich genommen effizient sind, neu kombiniert aber Schnittstellen vermeiden und damit noch effizienter sein könnten? Werden Materialien als Abfall entsorgt, die man in anderen Bereichen recyceln könnte? Exakt in derartigen Fragestellungen liegt der Schlüssel zur Perfektion.
OPEX-Profis verändern Bereiche, die unterhalb des Wahrnehmungsradars liegen.