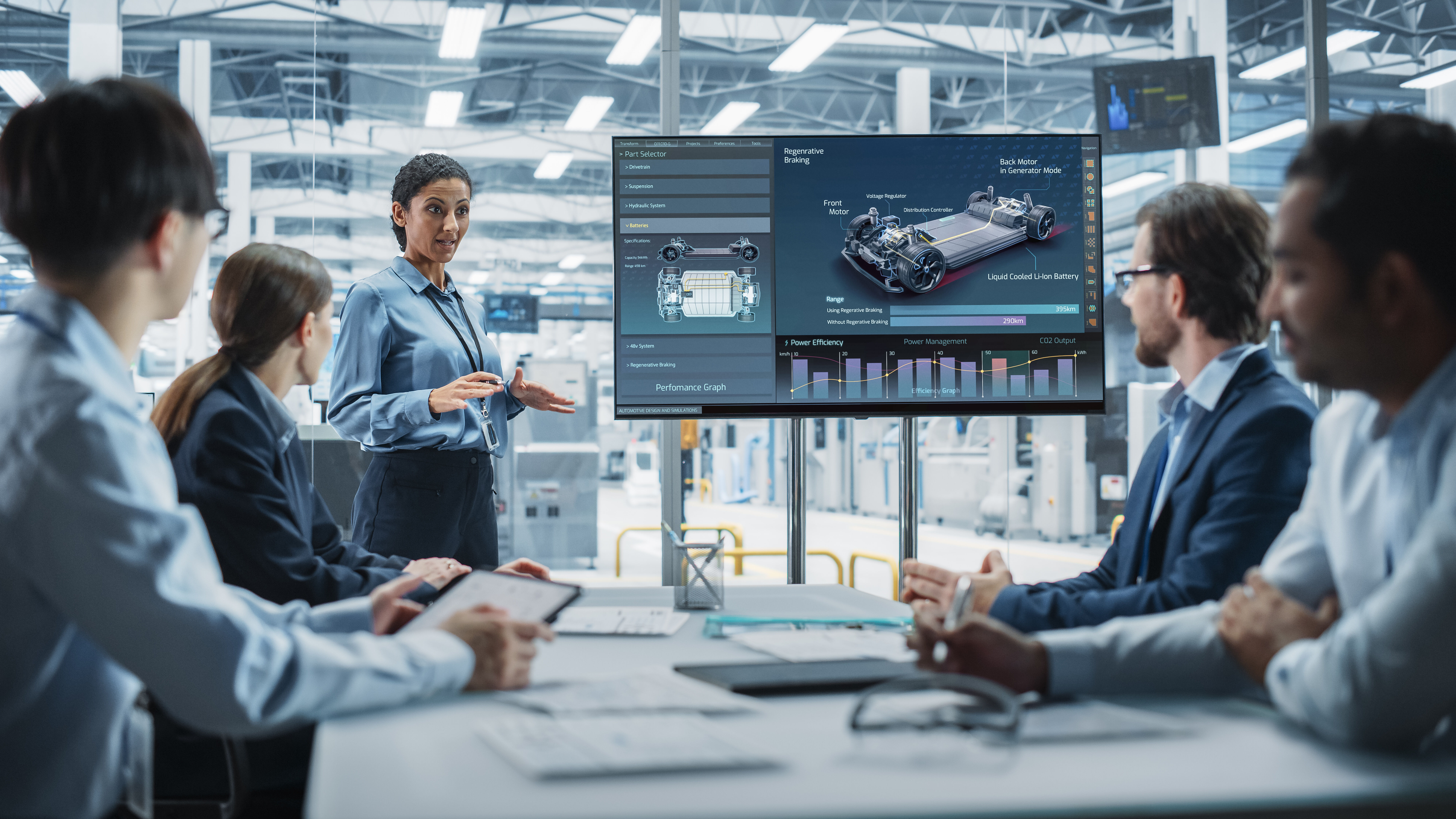
Transformation ohne Tempolimit
BUILD, BOOST, RE:THINK – ein Automobilzulieferer etabliert weltweit ein neues Produktionssystem mit OPEX-Ausrichtung
Beim Entwickeln und Vorantreiben von Marktinnovationen zählt ein deutsches Familienunternehmen bereits zur TOP-Liga. Doch nun gilt es, die über 50 internationalen Standorte des Elektronik- / Mechatronik-Spezialisten mit einem neuen, einheitlichen Produktionssystem auf aktuelle wirtschaftliche Herausforderungen und Zukunftsmärkte auszurichten.
Gemeinsam mit EFESO schafft das Unternehmen nicht nur die Rahmenbedingungen für den Wandel. Mit spielerischen Elementen wie einem OPEX-Award initiiert es weltweit über 300 Verbesserungsprojekte und spart bereits in der Anlaufzeit des neuen Systems rund 30 Millionen EUR ein.
Herausforderung
Ein weltweit etablierter Automobilzulieferer wappnet mit einem neuen Produktionssystem seine Werke in 20 Ländern rund um die Welt für aktuelle und zukünftige Marktveränderungen. Mittels einer strikten OPEX-Ausrichtung sollen Effizienzdenken und Kooperation sowohl in den Werken als auch im gesamten Unternehmen etabliert werden.
MEHREFESO Lösungsansatz
Mit dem BUILD, BOOST, RE:THINK-Prinzip adressiert EFESO die entscheidenden Elemente für erfolgreiche Transformation in der Industrie. In diesem Fall konzentrierte sich das Projektteam dabei auf drei Handlungsfelder: das neue Produktionssystem, eine entsprechend angepasste Unternehmensorganisation sowie das Thema „Shopfloor Leadership“.
MEHRLessons Learned
Die regelmäßige Kommunikation von Fortschritten und Erfolgen in den Werken sowie im Werksverbund erwies sich als wichtiger Beschleuniger der Transformation. Zudem stehen die Betrachtung von Reifegrad und Performance für jedes Werk im Vordergrund, was ein einheitliches, gemeinsames Verständnis der Ziele und Maßnahmen über Länder- und Kulturgrenzen hinweg ermöglicht.
MEHREFESO Erfolgsmodell
Mit einem Wettbewerb zwischen den Werken ermittelte das Unternehmen 300 Use Cases für effizientere Prozesse – und begeisterte die Teams rund um die Welt für OPEX.
MEHRGlobaler Werksverbund auf OPEX-Kurs
Traditionsbewusst und zukunftsorientiert agiert das Familienunternehmen in diesem EFESO-Projektbeispiel: Vom schwäbischen Stammsitz aus entwickelte sich der Hersteller elektronischer und mechatronischer Produkte im Laufe seiner rund einhundertjährigen Firmengeschichte zu einem innovationsstarken Player in der Automobilzulieferindustrie. Mit einem umfassenden Produktportfolio aus Steuer- und Bedienelementen sowie Sensoren erlangte das Unternehmen im Laufe der Zeit eine solide Stellung als Tier-1-Lieferant bei heimischen und internationalen OEM – und nahm neue Märkte und Themen wie die Elektromobilität oder das autonome Fahren rechtzeitig für sein weiteres Wachstum ins Visier.
Mit dieser Ausrichtung gelang dem Automobilzulieferer eine internationale Erfolgsgeschichte: mit ca. 20.000 Mitarbeitenden an über 50 Standorten ist er in 20 Ländern rund um die Welt vertreten und wird von OEM und Partnerunternehmen für Innovationsstärke und Qualität geschätzt. Bereits Anfang der 2020er-Jahre nahm das Unternehmen die geopolitischen und wirtschaftlichen Herausforderungen in der Automobilindustrie zum Anlass, Verbesserungspotenziale in allen Werken zu ermitteln und zu aktivieren. Die strategischen und operativen Stoßrichtungen dazu lauteten:
- Verwirklichung einer effizienten und kollaborativen Produktion.
Die Werke arbeiteten in einem veralteten Produktionssystem, das nicht standardisiert auf alle Standorte übertragen wurde. Somit organisierte und optimierte jedes Werk seine Fertigung selbst – dies funktionierte zwar jeweils an den Standorten gut, verhinderte aber den Blick auf das globale Maximum der Leistungen und Kapazitäten. Ein zeitgemäßes, einheitliches Produktionssystem für alle Werke sollte deren Effizienz steigern und das Gesamtoptimum des Werkverbundes erfassbar machen.
- Initiierung und Etablierung von Operational Excellence (OPEX).
Der Automobilzulieferer legte zudem viel Wert darauf, die technologischen Veränderungen mit einer Weiterentwicklung der Organisations- und Arbeitskultur zu flankieren. Mit den Prinzipien und Methoden einer Lean Transformation sollte der gesamte Werksverbund daher auf den Kurs kontinuierlicher Verbesserung im Sinne von OPEX gebracht werden.
- Motivierung und Qualifizierung der Belegschaft.
Mitarbeitende aus 20 Ländern über alle Sprachen und Kulturen hinweg auf einen einheitlichen Kurs in Richtung Effizienz und enger Zusammenarbeit auszurichten, war die dritte und möglicherweise anspruchsvollste Aufgabenstellung. Schließlich sollte mehr erzielt werden als eine reine Vermittlung des neuen Produktionssystems: die Belegschaft sollte von Anfang an in ein gemeinschaftliches, standortübergreifendes Projekt involviert werden, um von Tag eins an Verbesserungsvorschläge einbringen und Verantwortung für Aufgaben übernehmen zu können.
Mit dem Bewusstsein, dass diese Veränderungsschritte analog zur gravierenden Transformation des Automotive-Marktes schnell greifen und Ergebnisse erbringen müssen, setzte das Unternehmen einen engen Zeitrahmen von fünf Jahren vom Projektstart bis zum weltweit laufenden Produktionssystem. Mit EFESO holte es einen Umsetzungspartner an Bord, der mit der notwendigen Branchenexpertise sowohl für Tempo als auch Resultate sorgte: bereits nach dreieinhalb Jahren konnten die Projektziele erreicht und über 50 Standorte weltweit auf OPEX ausgerichtet werden.
In dreieinhalb Jahren werden über 50 Standorte weltweit auf OPEX ausgerichtet.
Mit Lean-Prinzipien zu Millionen-Einsparungen
Das Gesamtprojektteam umfasste insgesamt ca. 100 Personen: Projektverantwortliche des Unternehmens aller Führungsebenen arbeiteten mit 45 EFESO-Experten für OPEX und Change Management zusammen. Den methodischen Rahmen für alle Projektschwerpunkte und Maßnahmen setzte das BUILD, BOOST, RE:THINK-Prinzip von EFESO, welches drei Elemente für eine erfolgreiche Transformation adressiert (siehe Grafik): Die Verbesserungs- und Leistungsfähigkeit der Mitarbeiter bzw. Organisation sowie die Fähigkeit, zentrale Schlüsselelemente der Wertschöpfung – wie in diesem Fall das weltweite Produktionssystem – schnell zu integrieren und erfolgreich zu nutzen.
Toolbox für Effizienz in der Produktion
Je nach Projektkontext lassen sich BUILD, BOOST und RE:THINK unterschiedlich stark gewichten. So kann z.B. der Fokus eher auf „BUILD“ liegen, wenn im Unternehmen nur ein sehr geringes Lean-Knowhow vorhanden ist oder Lean nicht konsequent in der Linie / dem Shopfloor Management praktiziert wird. In diesem Fall konzentrierte sich das Projektteam auf die folgenden Handlungsfelder:
- Produktionssystem
Das neue System eröffnet den Mitarbeitenden den Zugriff auf unterschiedliche Informationen wie Kennzahlen, Zielabweichung sowie auf das umfangreiche Schulungsportal. Dies lässt sich leicht so konfigurieren, dass jedem Nutzer die für ihn relevanten Daten zur richtigen Zeit zur Verfügung stehen. Zudem befähigt das System alle Organisationsebenen, Bestandteil der Transformationsreise in Richtung operativer Exzellenz zu sein. Eine Lean-Toolbox befähigt die Teams dazu, die sechs eigens für dieses Unternehmen zusammengestellten Kernprinzipien der schlanken Produktion zu praktizieren: Zero Waste, Just in Time, Zero Defects, Empowered Teams, Zero Accidents, Learning Organisation. Dazu stehen 20 global definierte Vorlagen für Lean-Tools und Methoden in 12 Sprachen zur Verfügung.
- Organisation
Das Projektteam konzipierte eine neue Unternehmensorganisation für alle Standorte zur Unterstützung und Beschleunigung der Transformation. Dazu definierte es u.a. neue Rollen und Verantwortlichkeiten wie z. B. Lean- oder OPEX-Verantwortliche sowie -Multiplikatoren.
- Shopfloor Leadership
Zusätzlich startete das Unternehmen unter Anleitung des Projektteams ein speziell auf das neue Produktionssystem zugeschnittenes Bildungsprogramm mit mehreren Ausbildungsstufen und Trainingseinheiten. In den dreieinhalb Jahren konnten so mehr als 5.000 Mitarbeitende trainiert und 70 OPEX-Moderatoren ausgebildet werden. Diese treiben neue Praxisprojekte stetig voran und sorgen dafür, dass alle Werke von Erfolgen profitieren. Schon in der Anlaufzeit des neuen Systems kamen somit 300 Verbesserungsprojekte zusammen, mit denen der Automobilzulieferer rund 30 Millionen EUR einsparte.
> 5.000 Mitarbeitende wurden in dreieinhalb Jahren trainiert – und 70 OPEX-Moderatoren ausgebildet.
Kernelemente Transformation
Keine Option, sondern Pflicht: Erfolge teilen
Bei der Umsetzung des Projektes erwiesen sich die folgenden Erfahrungswerte als besonders erfolgskritisch:
Kommuniziere Erfolge schnell und konkret!
Mangelhafte Transparenz und Messbarkeit von Projektergebnisse bremsen motivierte Teams und somit den gesamten Transformationsprozess sukzessive aus. Eindeutige KPIs und deren regelmäßige Kontrolle und Kommunikation sind daher unverzichtbar in Projekten dieser Größenordnung. Dazu zählt auch, Fortschritte und Erfolge regelmäßig und konkret zu kommunizieren – auch über die Werksgrenzen hinaus. So lässt sich feststellen, wo Bedarf an weiterer Unterstützung / Trainings besteht.
Schaffe ein Bewusstsein für Leistungsfähigkeit und -potenzial!
Das Unternehmen erkannte, dass ein Bewertungssystem zu den getroffenen Maßnahmen besonders aussagekräftig ist, wenn es zwei Dimensionen erfasst: Reifegrad und Performance. Jedes Werk bricht seine OPEX-Ergebnisse auf diese Dimensionen herunter; zugleich lassen sich entsprechende Ergebnisse zur Gruppe / dem Werksverbund für die Management-Ebene aggregieren, z.B. mit KPI wie Ausschussrate, OEE, Mitarbeiterproduktivität, Durchlaufzeit.
Unterschätze niemals die kulturelle Dimension!
Eine Unternehmenstransformation in dieser Größenordnung sollte nicht ausschließlich als technologisches oder organisatorisches Projekt verstanden werden. In diesem Fall berücksichtigte das Projektteam interkulturelle Aspekte und die regionalen Unternehmenskulturen als ebenso erfolgskritisch und stellte Werte und Verhaltensweisen proaktiv und konstruktiv in Frage.
Sechs Dimensionen verschafften Klarheit über den Reifegrad der einzelnen Werke.
Wettbewerb um OPEX-Award initiiert 300 Verbesserungsprojekte
Schon in einem einzelnen Werk kann die Einführung eines neues Produktionssystems schnell auf Hürden bei Technologie, Unternehmenskultur und Knowhow stoßen – bei einem weltweiten Projekt erhöht sich das Risiko um den Faktor X, das eine solche Transformation im Sande verläuft. In beiden Fällen legt das Team von EFESO daher viel Wert darauf, Handlungssicherheit herzustellen: Anfangs setzen die Lean-, OPEX- oder Digitalisierungsexperten die Orientierungspunkte und Impulse für das Projekt, wechseln dann in eine Coach-Rolle und ziehen sich schließlich ganz aus dem Projekt zurück. Denn es gilt, auf lange Sicht tausende von Mitarbeitern zu kontinuierlicher Verbesserung zu befähigen – weit über den begrenzten Projekthorizont hinaus.
In diesem wie auch in vergleichbaren OPEX-Projekten trugen zwei Aspekte besonders zum erfolgreichen Projektabschluss bei. Bei „Performance und Reifegrad“ ist das Thema „Kennzahlmanagement“ zu betonen: das Unternehmen erfasst nun in einem Performance Management-System alle relevanten Fertigungsinformationen vom Shopfloor einzelner Werke bis hin zur Gesamtperformance des Werksverbundes. Mit einem Leadership-Scan erstellte das Projektteam zudem eine Reifegradbewertung, die anhand der Bedarfe des Produktionssystems des Automobilzulieferers abgeleitet wurde. Diese Bewertung entstand durch den Fokus auf sechs Dimensionen, zum Beispiel Führungsverhalten am Ort der Wertschöpfung, Visualisierung und faktengetriebene Entscheidungsfindung wie auch individuelle Mitarbeiterweiterentwicklung.
Als „Leistungs-Booster“ auf kultureller Ebene erwies sich noch während des Projektes ein OPEX-Award, mit dem die besten Optimierungsvorschläge zu Prozessen, Materialverschwendung etc. im Sinne der Lean-Prinzipien prämiert wurden. Hieran beteiligten sich die Teams aller Werke mit großer Motivation, so dass 300 Verbesserungsprojekte initiiert wurden und bereits in der Anlaufzeit des neuen Systems Einsparungen von rund 30 Millionen EUR erbrachten. Auch hier erfolgte eine äußerst transparente Kommunikation: ein unternehmensübergreifendes Benchmarking / Punkte-Ranking über alle Werke hinweg nach Art einer Fußball-Liga-Tabelle zeigte, welche Werke sich als Sieger in Kategorien wie Leistung, Transformationsreife oder Best Practice behaupten. Dieser Wettbewerb wird nach wie vor jährlich mit signifikanten Ergebnissen in der Leistungsverbesserung der Werke ausgetragen.