Beratung Schlanke Produktion
Die Fokussierung auf den Wertstrom und die Vermeidung jeglicher Verschwendung im Wertschöpfungsprozess sind die Kernelemente einer Schlanken Produktion.
Nahezu jedes Unternehmen hat entlang dieser beiden Maximen Produktionssysteme eingeführt, Prozesse in Produktion und Logistik verschlankt und damit Produktivitätssteigerungen erreicht.
Der tiefere Blick in die Fabriken zeigt jedoch ein sehr heterogenes Bild und nach wie vor zahlreiche Defizite:
- Produktionssysteme sind oft sehr theoretisch und wenig praxistauglich beschrieben oder veraltet und werden werkspezifisch unterschiedlich interpretiert und umgesetzt
- Die Einführung hat häufig nur Projektcharakter und wird primär von Zentralstellen gepusht, Roll outs in der Fläche fehlen
- In Lean-Methoden qualifizierte Führungskräfte über alle Ebenen sind nur selten zu finden
- Managementsysteme zur kontinuierlichen Verbesserung der Zielabweichungssteuerung sowie zur strukturierten Problemlösung, z.B. Shop Floor Management sind häufig nicht voll entwickelt
- Indirekte Funktionen und Support-Bereiche sind meist „out of scope“
- Zielsysteme und Verbesserungsroutinen sind stark von interner Optimierung statt Umsetzung von Markt- und Kundenanforderungen geprägt
- Einheitliche und vor allem globale Standards sind primär hinsichtlich Technologien, weniger auf der Prozessebene zu finden
- Anwendungsfelder für die Nutzung digitaler Technologien und der vorhandenen „Datenschätze“ sind häufig nicht definiert, eine Digital-Roadmap fehlt. Zumeist gibt es verschiedene „Proof of Concepts“, also digitale Einzellösungen, die jedoch keiner konsistenten Strategie folgen und nicht skalierbar sind.
Diesen Schwachstellen gegenüber stehen jedoch anspruchsvolle Ziele, die über die Operations-Funktionen zu erfüllen sind:
- Hohe Reaktionsgeschwindigkeit über kurze Durchlaufzeiten und stabile Prozesse
- Flexible und zugleich wirtschaftliche Erfüllung individueller Kundenanforderungen bei hohem Qualitätsanspruch
- Permanenter Beitrag zur EBIT-Steigerung und Stärkung der Wettbewerbsposition
- Fähigkeit zur horizontalen und vertikalen Vernetzung und Integration in globale Produktionsnetzwerke
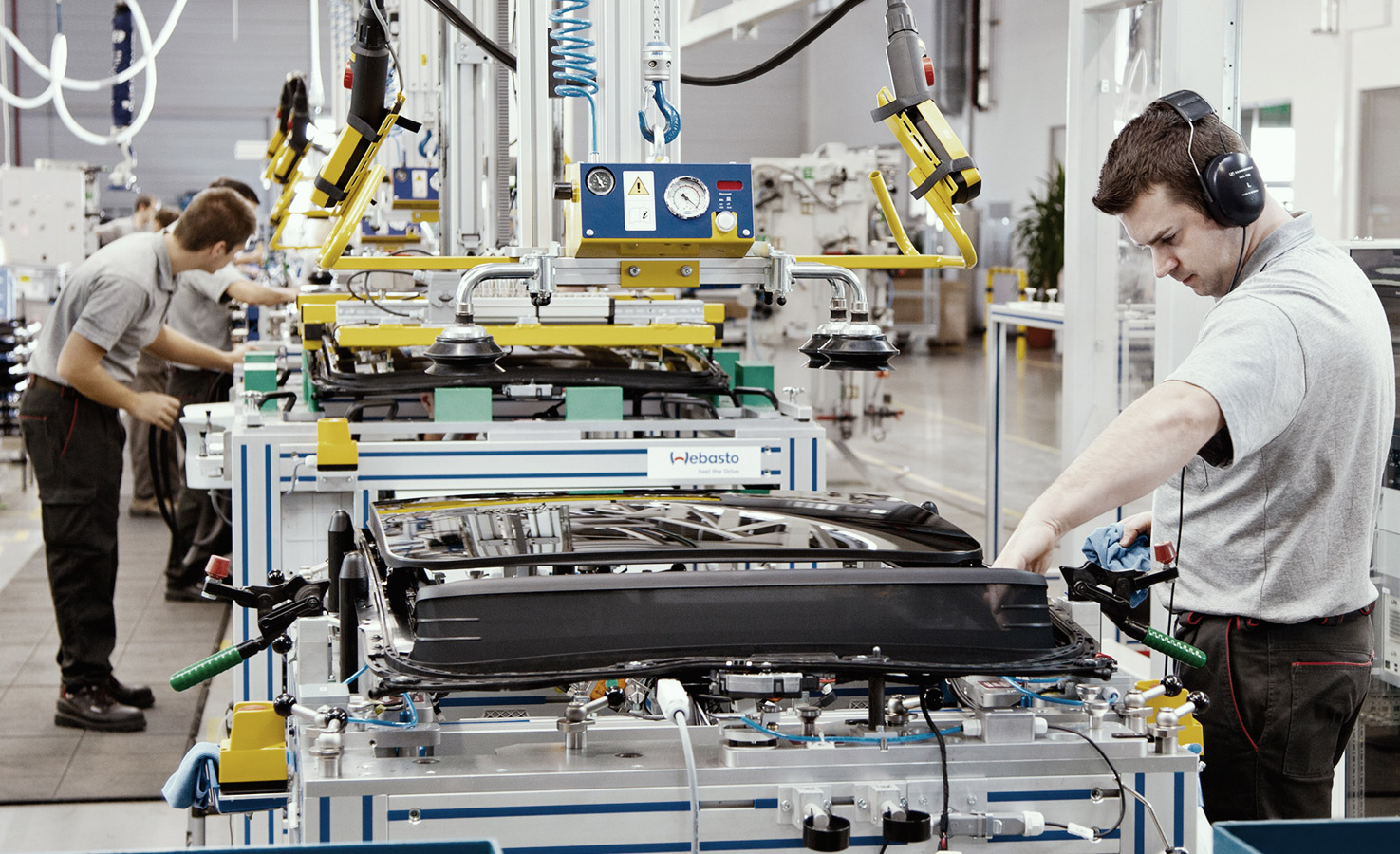
Lean Management Beratung
Die Berater:innen der EFESO begleiten die Einführung von Schlanker Produktion von der ersten Diagnose bis zur nachhaltigen und ergebniswirksamen Umsetzung. Dabei nutzen sie einen modular aufgebauten Beratungsansatz, der sowohl auf Ebene einzelner Werke als auch in einem globalen Produktionsverbund greift.
Dabei stehen drei Dimensionen gleichermaßen im Fokus:
- Aufbau eines Lean-Managementsystems als inhaltlichen und methodischen Rahmen sowie Implementierung einer Lean-Organisation
- Etablierung einer Lean-Kultur (Mindset & Behavior) in Kombination mit einem exzellenten Führungs-System
- Umsetzung eines Performance-Managementsystems zur kontinuierlichen Messung der Verbesserungserfolge und der Lean-Reifegradentwicklung
1: Diagnose, Benchmarking und Potenzialermittlung (Current State)
Der erste Schritt eines Lean-Transformations-Programmes ist eine schnelle und strukturierte Diagnose der Ausgangssituation mit folgenden Methoden und Schwerpunkten:
- Standardisierte und modular aufgebaute Werks-Assessments in direkten und indirekten Funktionen
- Einsatz von Scanning-Tools zur Bewertung von Lean-Reifegrad und digitalem Status Quo
- Bewertung der Führungssysteme, Lean-Qualifikation und Change-Kapabilitäten
- Internes und externes Performance-Benchmarking
- Differenzierte und fundierte Potenzialableitung
2: Etablierung Top Management Attention
Zeitgleich zur Aufnahme des Status Quo in den Werken wird ein wesentlicher Erfolgsfaktor für die Lean Transformation geschaffen - die Sicherstellung des Verständnisses von Lean auf Ebene der Führungskräfte sowie die Definition und Verankerung der entsprechenden Rollen und Verantwortlichkeiten im Projekt und Tagesgeschäft:
- Lean- und Digital-Initial-Trainings für Top-Management und Führungskräfte der ersten und zweiten Ebene
- Besuche von Best-Practice-Unternehmen und Austausch mit deren Management
- Erarbeitung der Kommunikationsstrategie
- Festlegung der Führungssysteme, Rollen und Verantwortlichkeiten
- Informationsveranstaltungen für die Belegschaft mit Bekenntnis zur Lean-Reise
3: Strategieabgleich und Zielbild (Vision and Target)
Um ein Lean-Transformationsprogramm strategiekonform und ausgerichtet an den Kunden- und Markterfordernissen umzusetzen, ist die Entwicklung einer Lean-Vision und eines Zielbildes sowie die Schaffung des inhaltlichen und methodischen Rahmens, z.B. in Form eines Produktionssystems erforderlich.
Dies erfolgt in folgenden Schritten:
- Workshops mit dem Management zur Ableitung der Ziele, Anforderungen und Rahmenbedingungen aus der Unternehmens- und Produktionsstrategie
- Management-Workshops zur Definition von Zielzustand und „Transformations-Leitplanken“: Lean-Vision, verbindliche Lean-Grundsätze und -Prinzipien, Kombination von Lean und Digital, Integration indirekter Bereiche
- Verabschiedung einer Lean-Organisation: zentrale und dezentrale Rollen & Verantwortlichkeiten
- Entwicklung bzw. Weiterentwicklung Produktionssystem („Lean und Digital“, „Praktischer Ratgeber statt theoretisches Werk“)
- Roadmap zur Einführung und Detailplanung der ersten Transformationsphase
- Festlegung eines kaskadierten KPI-und Scan-Systems zur Erfolgsmessung und Reifegradverfolgung
4: Pilotierung und Start Qualifizierung in der Fläche (Quick Impact)
Als ersten Schritt zur Umsetzung empfehlen wir die Durchführung von kurz getakteten Verbesserungsinitiativen mittels derer sowohl die Grundlogik unterschiedlicher Lean- und Digital-Prinzipien als auch deren Effekte einfach und schnell sichtbar werden. Das schafft Transparenz, Verständnis und Akzeptanz und wird durch flankierende Qualifizierungsmaßnahmen ergänzt. Hierbei liegt der Fokus auf dem Training des mittleren Managements sowie in der Ausbildung von Lean-Expert:innen und -Mulitiplikatoren.
Die einzelnen Module in dieser Projektphase sind exemplarisch:
- Strukturunabhängige Kurzfristmaßnahmen zur Sensibilisierung der Basis (Point-Kaizen-Ansatz) und Sichtbarmachung erster Veränderung: z.B. OEE-Verbesserung, Arbeitsplatzstandards, Bestandsreduzierung
- Leuchtturmprojekte zur Verschlankung von Prozessen und Einführung von Lean-Konzepten (Prozess-Ansatz): z.B. Taktoptimierung, Fließkonzepte, Pull-Steuerung
- Digital-Piloten zur Erstanwendung smarter (IoT) Technologien (System-Ansatz): z.B. Predictive Maintenance, digitale Q-Regelkreise, Smart Logistics, Smart Tooling, real time performance tracking
- Policy Deployment von Management bis Shop Floor, z.B. durch Shop-Floor-Management Piloten (physisch und digital), Aufbau von KPI-Systemen und dezentrale Problemlösungskompetenz
- Zielgruppenspezifische Qualifizierung: Lean- und Digital-Methoden, Transformations- und Führungs-Know-how, Expertenausbildung und
- Programme zur Ausbildung von Lean-Expert:innen und Multiplikatoren nach dem Train-the-Trainer-Ansatz
- Aufbau einer Best-Practice-Sammlung
- Planung des Roll outs (lokal bis global)
5: Roll out und Absicherung Nachhaltigkeit (Sustainable Results)
Nach der Durchführung der Piloten und der Qualifizierung der mittleren Managementebene und Expert:innen ist die Basis für den flächendeckenden Rollout im Werksverbund geschaffen. Dies ist im Einklang mit den Schwerpunkten aus dem Produktionssystem zu planen und durch den die Verankerung von Rollen und Verantwortlichkeiten (Projekt und Linie) sicherzustellen.
- Lessons learned aus Pilotprojekten und Ausrollen in weitere/ größere Umfänge (Wertstrom-Ansatz, cross-funktionale Projekte)
- Train-the-Trainer-Konzepte mit zunehmender Verantwortung interner Ressourcen
- Etablierung der zentralen und dezentralen Lean-Organisation inklusive Integration und Synchronisation mit der Linienorganisation
- Verankerung der Verbesserungskonzepte in den Fachbereichen und im Tagesgeschäft
- Aufbau von Ausbildungskonzepten für Nachwuchsführungskräfte
- Aufbau von Kompetenznetzwerken und Förderung der internen Vernetzung, Initiierung von Award-Konzepten, Best-Practice-Sharing-Plattformen
Zahlreiche EFESO-Projekte zeigen, dass durch die konsequente Verschlankung und Standardisierung von Prozessen sowie die darauf aufbauende, gezielte Nutzung digitaler Technologien und Analytics-Tools erhebliche Potenziale zur Verbesserung der operativen Performance gehoben werden können. Dabei setzt EFESO nicht auf standardisierte Ansätze, sondern bietet Ihnen maßgeschneiderte Programme auf dem Weg zur Schlanken und Digitalen Fabrik.
Unsere praxiserfahrenen Berater:innen, die Trainer:innen aus unserem Learning-Campus sowie unser Eco-System zu führenden Technologieanbietern unterstützen Sie auf dem Weg zu operativer Exzellenz aus einer Hand.